Advanced Polymers for Practical Use
The need for improved, more cost effective satellite and land-based electronic applications has prompted the development of a high performance, low-cost substrate for printed circuits. This advancement in liquid crystal polymers (LCPs) is also ideal for high barrier packaging for foods and beverages, high performance tubing, barrier layers for cryogenics, and high temperature electrical insulation.
The technology for multilayer printed circuit boards was developed under a Small Business Innovation Research (SBIR) contract between NASA's Goddard Space Flight Center and the polymer division of Foster-Miller, Inc., of Waltham, Massachusetts. The commercial viability that resulted from the original research was so substantial that Foster-Miller created a spinoff company, Superex Polymer, Inc., also of Waltham, Massachusetts.
LCPs have a propensity to self-align during the liquid state, forming oriented regions that can be further constructed into fiber, film, or molded parts. Because of this alignment capacity, once an LCP layer is formed, its structure persists, becoming resistant to such stresses as melting heat. LCP thin layers can be incorporated into blends that offer more favorable performance and cost-competitive advantages over other materials.
Because of Superex's efforts in processing LCPs, exceptionally strong, stiff, and lightweight tubing is being manufactured for endoscopic instruments. The tubing was the winner of the prestigious R&D 100 Award and has been licensed to a medical equipment company.
LCPs can also be used as a "super barrier" packaging material. This is partly due to their oxygen transmission level—six to eight times higher than ethylene vinyl alcohol under humid conditions. By using LCPs as thin high barrier layers, their properties can prevent oxygen from deteriorating the taste of precooked and packaged food. Also, the LCP water vapor transmission level exceeds many fluoropolymers. Additionally, LCP films have excellent barrier properties for carbon dioxide, nitrogen, and other gases. Compared with polymers typically used for packaging, the price of LCP resin is high, but its proportionately higher properties give LCPs favorable performance tradeoffs, according to Rick Lusignea, president of Superex Polymer, Inc.
New processing and packaging technology is advancing, such that layering of various films, along with LCP, is possible to create bottles, trays, and jars. Packaging applications targeted for LCPs include: multilayer films for all-plastic retort pouches and bag-in-boxes with long shelf-lives; multilayer food trays with a shelf-life of one year; LCP barrier layers for disposable medical bags; LCP laminates for use in high-barrier bags for industrial chemicals; plastic liners for reusable steel tanks; and LCP-based plastic lids for snack food cups and trays to replace metal lids.
Superex is pioneering blow-molding machinery, bolstering the company's prospects for moving into a variety of key markets.
There are still many other possible applications for this technology, including the use of LCP laminates in compact, high-speed computers, robust high-density circuit boards, multilayer boards, microwave and high-speed digital circuit boards, multichip modules, and flexible printed circuits.
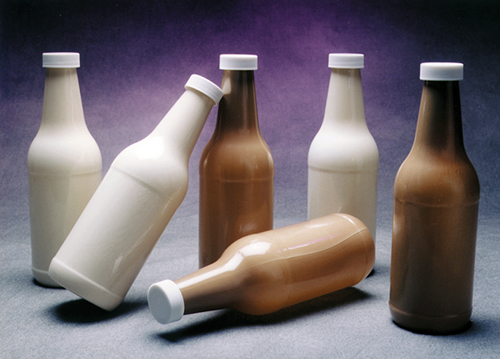
Superex Polymer, Inc.’s liquid crystal polymers can be used in the production of bottles.
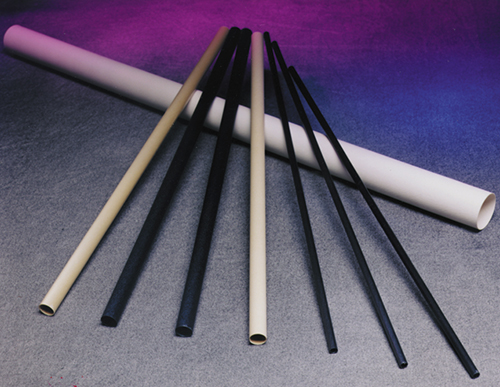
Superex Polymer, Inc.’s liquid crystal polymers can be used to produce exceptionally strong, stiff, and lightweight tubing for such uses as endoscopic instruments.