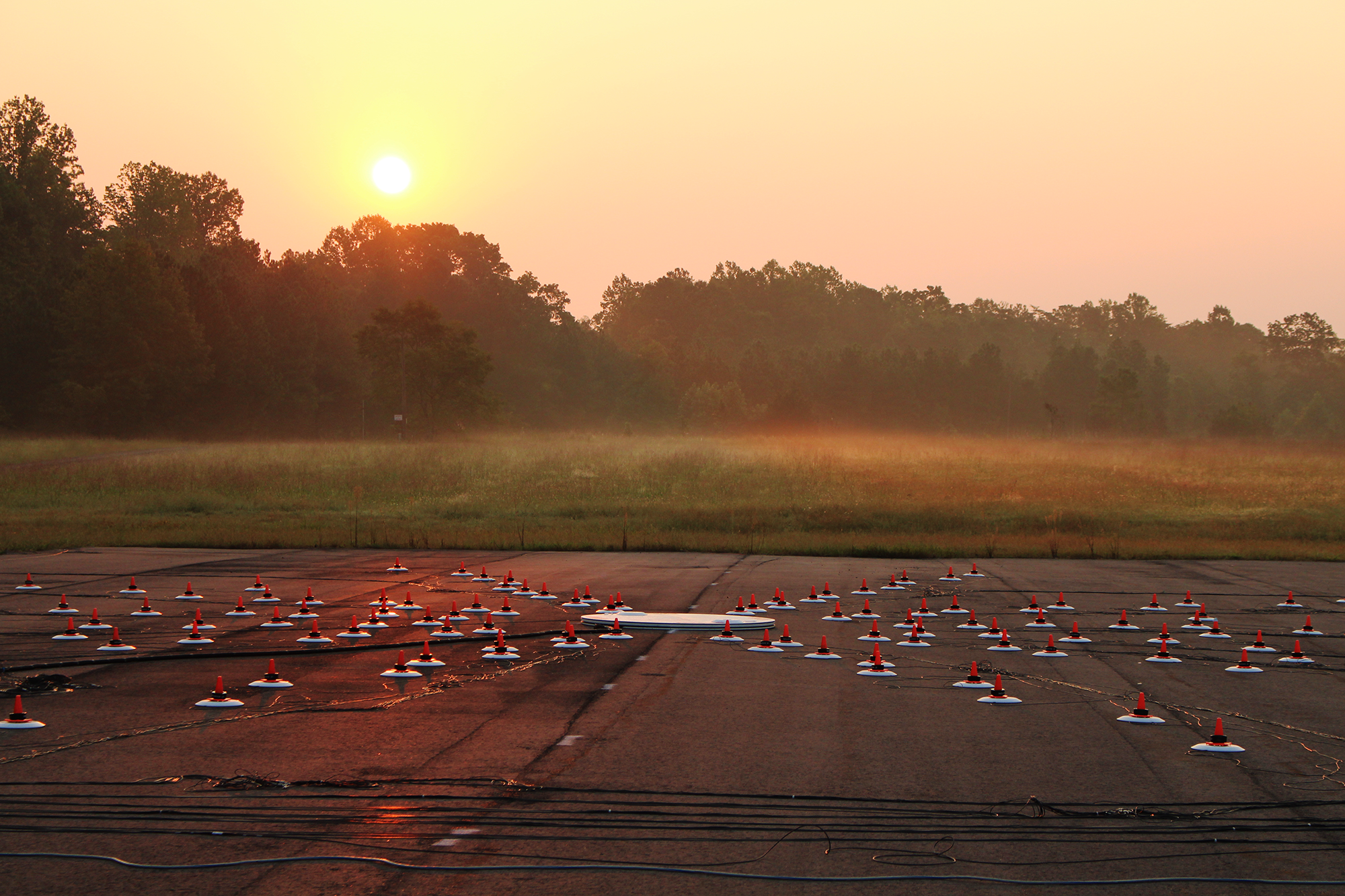
Measuring Buzz, Hum, and Rattle
Subheadline
Wireless microphone array quickly, cheaply, accurately maps noise from aircraft and much more
Airplane manufacturers running noise tests on new aircraft now have a much cheaper option than traditional wired microphone arrays. And it’s sensitive enough to help farmers with pest problems. The wireless microphone array that one company recently created with help from NASA can locate crop-threatening insects by listening for the sounds they make in fields. And now, it’s making fast, affordable testing possible almost anywhere.
Since releasing its first commercial product in 2017, a sensor for wind tunnel testing developed with extensive help from NASA (Spinoff 2020), Interdisciplinary Consulting Corp. (IC2) has doubled its staff size and moved to larger lab and office space to produce its new WirelessArray product. Interested in making its own flight tests more affordable, NASA’s Langley Research Center in Hampton, Virginia, supported this new project as well, with multiple Small Business Innovation Research (SBIR) contracts and expert consulting.
The result is a series of small, saucer-shaped bases equipped with multiple sensors that measure the air pressure changes created by overhead sounds. Airplanes go through noise testing and require certification so that they don’t exceed the noise level set for their body type by the Federal Aviation Administration. When an airplane flies directly overhead, the array collects noise data to build a two-dimensional map of the sound pressure and its source. A custom software package translates that information for the end user.
Thanks to support from NASA, the more affordable testing tool is seeing applications beyond aircraft, from animal monitoring to clean energy generation.
Neither Rain nor Snow
NASA Aeronautics has always used wired systems to collect the same data but saw the potential for a less cumbersome approach, said Tony Humphreys, chief engineer with Langley’s Measurement Sciences. Humphreys oversaw the WirelessArray SBIR contracts and also provided consulting and even a prototype device the company used as a starting point.
“Previously, when we went out to Edwards Air Force Base for a series of flight tests, we used a large array with hundreds of sensors. We had about 15 miles of cabling to hook up all of them, and it took a crew of six people three days to set up and tear down,” he said. The cables had to be positioned in a specific pattern to avoid overlapping, and if it rained, each sensor had to be covered to protect it from precipitation. Multiple semi-trucks hauled all of that equipment, along with power generators, racks of servers, and other equipment.
By contrast, two IC2 staff arrived at Langley’s flight-test range driving a minivan with all the hardware needed to test the WirelessArray system. Yet Humphreys said the data generated by the smaller wireless system was comparable to a conventional system.
The flight testing NASA and commercial airlines perform with a wired system is so expensive that it’s usually out of reach for smaller companies, said Chip Patterson, vice president of IC2, which is based in Gainesville, Florida. This technology, designed to meet NASA specifications, is changing that. Whether using one or 100 of the sensor nodes, anyone can afford to do flight testing.
“Each node contains a small computer system,” said Patterson. “It’s able to acquire and store data in memory on an SD card. It also has a small web server that allows the end user to poke it, asking it to start acquisition, stop recording, download files, check on the battery health, and more.”
A traditional wired system requires the simultaneous and instant download of all data, meaning the array is limited to the capacity of the hard drives it feeds into. IC2’s smaller system acquires significantly larger datasets, allowing that data to sit in each node until it’s collected. If, for example, a single node is placed in the field to collect community noise measurements over several months, it won’t be necessary to go to the site daily to download measurements.
The WirelessArray supports a variety of sensors, so a microphone can easily be swapped for an optical sensor or a variety of other types. Each unit has its own self-charging battery and solar panel, supporting long-term deployment. Built-in GPS maintains synchronized sampling across multiple nodes, and wireless communication allows users to download data remotely and monitor the health of each device. The nodes’ environmentally hardened enclosures make it possible to take measurements in any weather without additional protection from dust, snow, or extreme temperatures.
A startup developing a new remotely piloted vehicle can now get sophisticated flight test data to quickly identify noise issues during takeoff, flight, or landing. Multiple test flights for every modification can speed the time to market because the cost to set up, operate, and take down the system is so low.
Bugging Bugs
All it takes to operate an individual node or an extensive array is an off-the-shelf wireless access point and a standard laptop loaded with IC2’s software application. The nodes are also easily integrated into existing systems.
This small, portable technology is finding its way into a variety of projects and applications beyond aircraft testing. IC2 is working with an entomologist to use acoustic data to listen for high-frequency insect sounds in agricultural settings. Discovering where insects feed on crops will make it possible for farmers to intervene before they do too much damage while limiting pesticide use to those areas.
Researchers are exploring ways to monitor mice and rats in a laboratory setting by swapping the standard acoustic sensor that matches human hearing for an ultrasonic sensor. This will make it possible to monitor squeaks and other sounds that indicate an animal’s health and well-being. A similar ultrasonic sensor could monitor the flight path of supersonic aircraft, identifying when a sonic boom is approaching an area.
The technology can be applied to anything that generates sound, collecting data according to a preset schedule or on demand. Rocket engine test stands, and environmental observations such as the noise level at airports are just a few possibilities. NASA could also use this system to collect data for entirely new airplane designs.
“We’ve been pushing the acoustic side as aeronautics move into more advanced concepts like the truss-braced wing, maybe distributed electric propulsion, or others. That raises the need for noise testing and noise certification for new configurations,” said Humphreys. So NASA engineers could soon trade the semitrucks and servers for a couple of minivans and laptops.
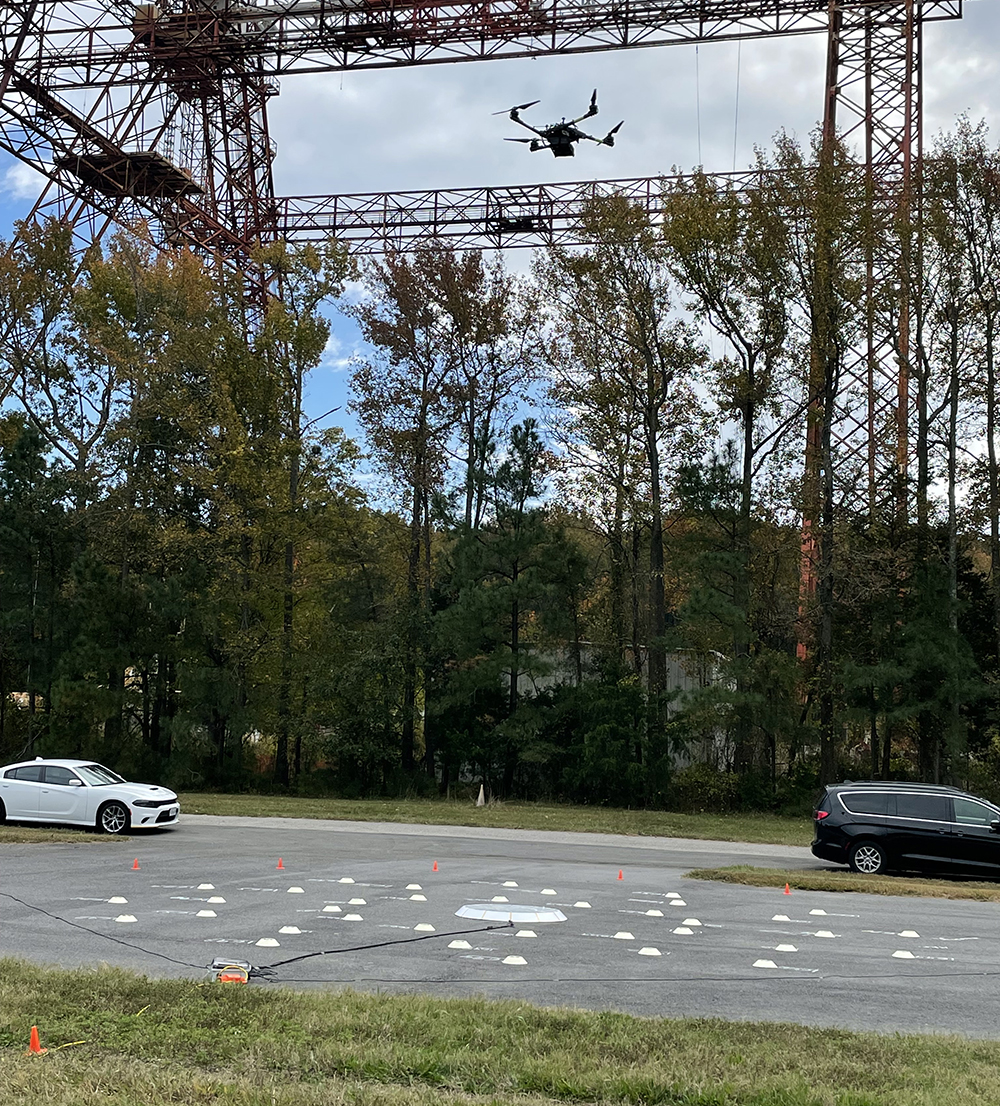
The WirelessArray developed by IC2, laid out here for a test flight at Langley Research Center, makes flight testing for drones quick and cost-effective. Credit: NASA
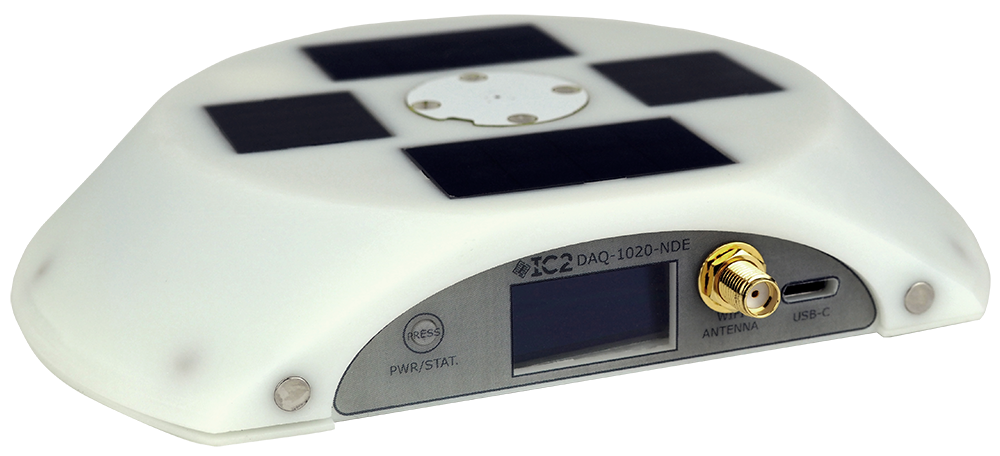
The WirelessArray developed by Interdisciplinary Consulting Corp. (IC2) uses self-powered, weatherproof nodes, like this one, to detect noise. The microphone can be replaced by other sensors to collect data for a day, a week, or even year-round. Solar panels on the top power the internal battery, and data is stored internally on a memory card. Credit: Interdisciplinary Consulting Corp.
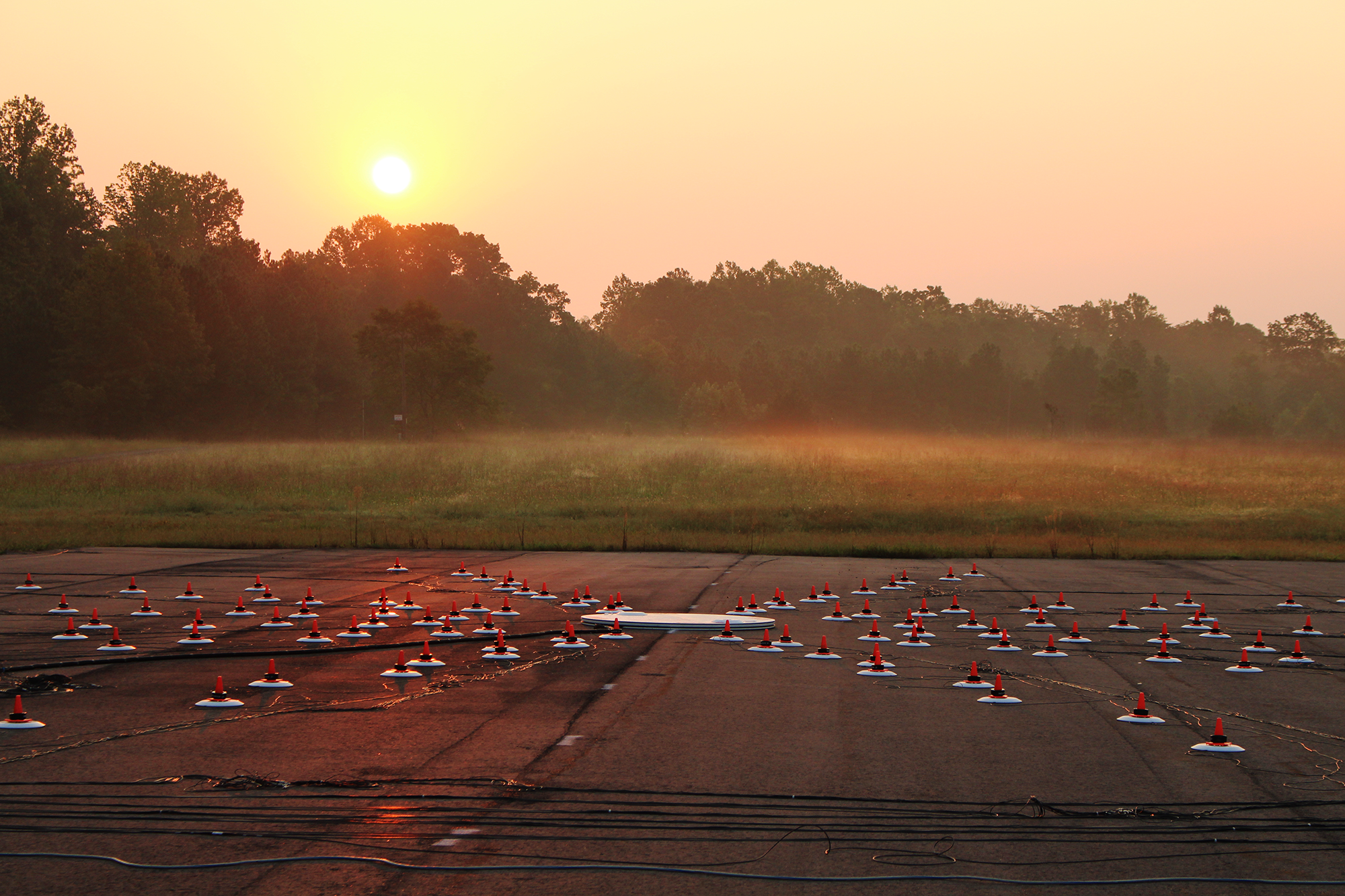
Test flights help airplane and drone manufacturers identify which parts of the aircraft are creating the most noise. Using hundreds of wired microphones makes it an expensive and time-consuming process to improve the design to meet noise requirements. Credit: NASA