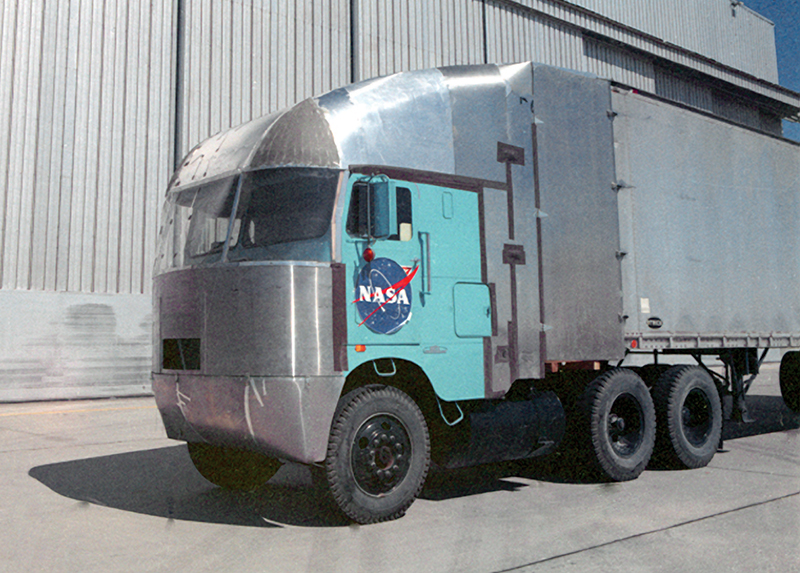
Aerodynamics Research Revolutionizes Truck Design
Originating Technology/NASA Contribution
The last 35 years have seen a sea change in the design of trucks on America’s highways, reflecting extensive research into vehicle aerodynamics and fluid dynamics conducted by NASA engineers. Thanks to the ingenuity of a Dryden Flight Research Center researcher bicycling through the California desert and a team of engineers in Virginia, the shape of rigs and recreational vehicles (RVs) today owes as much to the skies as it does the open road.
Bicyclists, motorcyclists, and even pedestrians feel a push and pull of air as large trucks pass. The larger a vehicle is and the faster it moves, the more air it pushes ahead. For a large truck, this can mean a particularly large surface moving a large quantity of air at a high velocity—its blunt face acting like a fast-moving bulldozer, creating a zone of high pressure. The displaced air must go somewhere, spilling around the cab into swirling vortices. The air traveling along the side moves unevenly, adhering and breaking away, and sometimes dissipating into the surrounding air. At the end of the cab or trailer, the opposite effect of the high-pressure zone at the front develops; the airflow is confronted with an abrupt turn that it cannot negotiate, and a low-pressure zone develops.
The high pressure up front, the turbid air alongside and under the vehicle, and the low pressure at the back all combine to generate considerable aerodynamic drag. A study published in Automotive Engineering in August 1975 found that a tractor trailer unit moving at 55 miles per hour displaced as much as 18 tons of air for every mile traveled. In such cases, roughly half of the truck’s horsepower is needed just to overcome aerodynamic drag.
In 1973, Edwin J. Saltzman, Dryden aerospace engineer and bicyclist, noticed the push and pull of large trucks at highway speeds while riding to work. As a tractor trailer overtook him, he first felt the bow wave of air pushing him slightly away from the road and toward the sagebrush; as the truck swept past, its wake had the opposite effect, drawing him toward the road and even causing both rider and bicycle to lean toward the lane. Saltzman mused about ways to mitigate the bow wave and trailing partial vacuum, and resolved to help trucks glide through air instead of push through it, and, in the process, decrease drag and increase fuel efficiency. NASA colleagues at Dryden were working on the effects of drag and wind resistance on different kinds of aircraft and the early space shuttle designs, so they transferred their considerable knowledge to the design of large trucks.
The first formal experiment involved a Ford van retired from delivery duties at Dryden. Mechanics attached an external frame which was then covered with sheet aluminum to give the van flat sides all around and 90-degree angles at all corners. The vehicle looked like an aluminum shoebox on wheels, simulating the cruder motor homes of the period. The Dryden engineers measured the vehicle’s baseline drag and then set about modifying the shape of the van: First rounding the front vertical corners, then the bottom and top edges of the front, then the edges of the aft end, and finally sealing the entire underbody of the van including the wheel wells, with tests run after each modification. Rounding all four front edges yielded a 52-percent drag reduction, while sealing the bottom of the vehicle gained another 7 percent. The engineers estimated the potential gain in fuel economy to be between 15 and 25 percent at highway speeds.
During the following decade, Dryden researchers conducted numerous tests to determine which adjustments in the shape of trucks reduced aerodynamic drag and improved efficiency. The team leased and modified a cab over engine (COE) tractor trailer, the dominant cab design of the time, from a Southern California firm. Modifications included rounding the corners and edges of the box-shaped cab with sheet metal, placing a smooth fairing on the cab’s roof, and extending the sides back to the trailer.
Rounding the vertical corners on the front and rear of the cab reduced drag by 40 percent while decreasing internal volume by only 1.3 percent. Likewise, rounding the vertical and horizontal corners cut drag by 54 percent, with a 3-percent loss of internal volume. Closing the gap between the cab and the trailer realized a significant reduction in drag and 20 to 25 percent less fuel consumption. A second group of tests added a faired underbody and a boat tail, the latter feature resulting in drag reduction of about 15 percent. Assuming annual mileage of 100,000 driven by an independent trucker, these drag reductions would translate to fuel savings of as much as 6,829 gallons per year.
On the other coast from Saltzman and his Dryden team, Dr. John C. Lin and Floyd G. Howard of Langley Research Center with Dr. Gregory V. Selby of Old Dominion University, Norfolk, Virginia, conducted a series of research projects in the late 1980s and early 1990s focusing on controlling drag and the flow of air around a body. One study conducted in 1989, “Turbulent Flow Separation Control,” explored controlling airflow—flow separation—to decrease energy expenditure and weight in airfoils, inlets, and diffusers and improve aircraft control and decrease drag. The study employed vortex generators, aerodynamic surfaces protruding from a body that draw faster moving air to the surface of the vehicle and disrupt the slower moving boundary layer air around a vehicle, the use of which can be traced back to research conducted by the National Advisory Committee for Aeronautics (NASA’s forebear) in the 1950s. The generated vortices “energize” the slower-moving boundary layer and thereby reduce drag and, in aircraft applications, increase lift.
Subsequent studies in 1990 and 1991 continued vortex-generator research with an exploration of various active and passive methods for controlling two-dimensional separated flow. These studies quantified and characterized the behavior and performance of a variety of large-eddy breakup devices for turbulent flow separation control.
Partnership
Answering the charge given by the U.S. Congress in the National Aeronautics and Space Act of 1958 to disseminate newfound technologies and discoveries to the public, NASA makes the results of its research and expertise of its scientists and engineers available through a variety of means. Sponsored by the Innovative Partnerships Program, these include published studies, NASA outreach, the Small Business Innovation Research and Small Business Technology Transfer programs, technology transfer offices at each NASA field center, and the Space Alliance Technology Outreach Program (SATOP).
The aerodynamics studies at Dryden have been made publicly available, and Aeroserve Technologies Ltd., of Ottawa, Canada, with its marketing arm, Airtab LLC, in Loveland, Colorado, applied these studies, the aerodynamic work at Langley, and the patented Wheeler vortex generator to the development of the Airtab vortex generator; designed to reduce drag and improve vehicle stability and fuel economy. Of the devices tested, the Wheeler showed the least parasitic drag, and Aeroserve optimized the Wheeler design for ease of installation and application to any vehicle.
Product Outcome
The Surface Transportation Assistance Act of 1982 required states to permit trucks with trailers as long as 48 feet on both interstate and intrastate highways; the previous length limit of 55 feet had applied to the tractor and trailer together. As the previous regulation made the COE tractor a dominant choice, owing to its decreased length regardless of aerodynamic or fuel efficiency shortcomings, the new regulations opened the door for a renaissance of the “conventional” cab. While COE designs place the cab directly above the engine, minimizing length and producing a cube-like tractor, conventional truck designs place the engine ahead of the cab. Though longer as a result, a protruding nose offers truck designers an inherently more aerodynamic shape from which to work. In 1982, COE trucks constituted over 65 percent of the market for the Peterbilt Motors Company, with similar numbers for other manufacturers; the cab-over design represented only 1 percent of sales for Peterbilt by 2004.
Streamlined cabs and fairings are now a common sight on our highways, and the once-prominent cab-over design has been abandoned in virtually all applications except small-capacity urban-oriented trucks where length remains a premium. The modifications tried by the engineers at Dryden were adopted by the truck manufacturers, as the same principles the NASA engineers demonstrated with COE trucks applied to conventionals. In addition, the cargo boxes of most delivery trucks today have rounded corners and edges, a direct application of the research conducted at Dryden on the “shoebox.”
Today’s trailers, on the other hand, are little changed from the last few decades. For livestock haulers, a key factor is that individual farmers have been the predominant owners of trailers, and these owners are difficult to convince about the costs of redesign versus the savings of superior aerodynamics. However, more and more livestock trailers are sporting boat-tail designs that ease the flow of air past the end of the trailer and minimize the low-pressure wake. Conventional trailer manufacturers have resisted change more so than others, in part because the aft end of such a trailer needs to be easy to manipulate at loading docks, where the optimal shape for superior aerodynamics—the boat tail—is impractical.
Likewise, the gap between the cab and the trailer can create a significant amount of drag as air swirls in the space between. Two conventional means to address this issue are problematic: Adding side extenders (to decrease the exposed gap) is expensive and might impede maneuverability; moving the fifth wheel forward (to shorten the gap) places more weight on the steering axle—which is legally regulated and limited—and reduces maneuverability while increasing driver effort and wear on steering tires and steering gear.
Addressing both of these dilemmas, Aeroserve’s Airtabs garner the benefits of the airflow found in a boat-tail design with the practicality of a squared-off end for loading and unloading, and see additional applicability smoothing the airflow between cab and trailer. Airtab vortex generators create a controlled vortex to reduce truck and trailer wind resistance and aerodynamic drag. Each Airtab produces two counter-rotating vortices of air, each approximately four to five times the height of the Airtab and several feet in length, that smoothly bridge the gap between tractor and trailer or control airflow past the rear of the vehicle. Airtabs thus allow an operator to set the fifth wheel to the optimum position without incurring extra drag or steering gear wear penalties and gain some of the aerodynamic benefit of side extenders.
At the back of a trailer, box van, or RV, Airtabs radically alter the airflow to reduce drag in two ways: Shifting the airflow pattern from vertical to horizontal to eliminate large eddies, and smoothing the airflow to artificially simulate a tapered rear of the vehicle. In fact, Airtabs have been shown effective on any vehicle with more than a 30-degree slope to the rear; the potential benefits stretch across vehicular applications and could thus benefit a considerable number of vehicles.
Smoothing the airflow results in markedly improved fuel economy without compromise to design utility, and additional benefits have been realized as well. The vortex generation reduces spray; users have reported improved rear and side view in wet or snowy weather, increasing safety and offering a clearer view of surrounding vehicles. Also, because Airtabs alter the airflow around the rear of a vehicle, the accumulation of road grime is reduced, keeping tail lights and reflectors clean and allowing less snow to build up, a significant safety benefit in foul weather. Less accumulation of road grime also means advertising and safety information on the back of a vehicle remains visible.
Perhaps most importantly, drivers of vehicles fitted with Airtabs have reported improved stability and handling and dramatically reduced fishtailing of trailers—an effect where the trailer sways or slides from side to side independent of the tractor, potentially causing catastrophic loss of control—effects that are especially important with the double trailers found in North America and the famous quad-trailer “road trains” in Australia. Increased stability also means that the trailer does not scrub on the sides of the road as much, increasing the life of tires. Drivers also report better handling when being passed in the same direction by other large vehicles.
Cummins Rocky Mountain LLC, a diesel engine and generator wholesale and distribution company in Broomfield, Colorado, recognized these benefits and agreed to promote and sell Airtabs after internal testing and customer feedback indicated that Airtabs brought immediate safety and fuel economy benefits when running equipment at highway speeds. The company noted additional benefits included ease of installation, minimal maintenance, and low price.
As more NASA research and development is adapted and introduced to the market by companies like Aeroserve, the vehicles populating our highways and interstates will likewise continue to evolve. Practical solutions to aerodynamic challenges, exemplified by the Airtab, offer increased stability, safety, and economy to airborne and surface vehicles alike, and NASA is proud to contribute tangible and current benefits to both fields of transport and travel.
Airtab® is a registered trademark of Aeroserve Technologies Ltd.
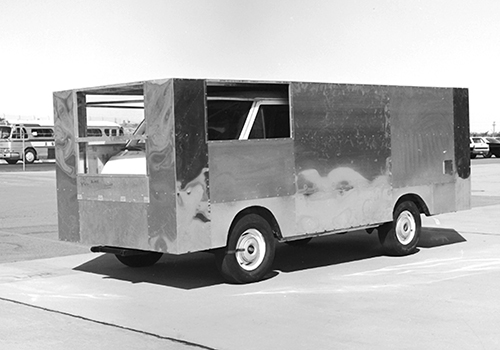
Dryden engineers modified a retired delivery van to test aerodynamic drag, first boxing the van with aluminum sheets at 90-degree angles, and then rounding the sides and fashioning a boat-tail rear.
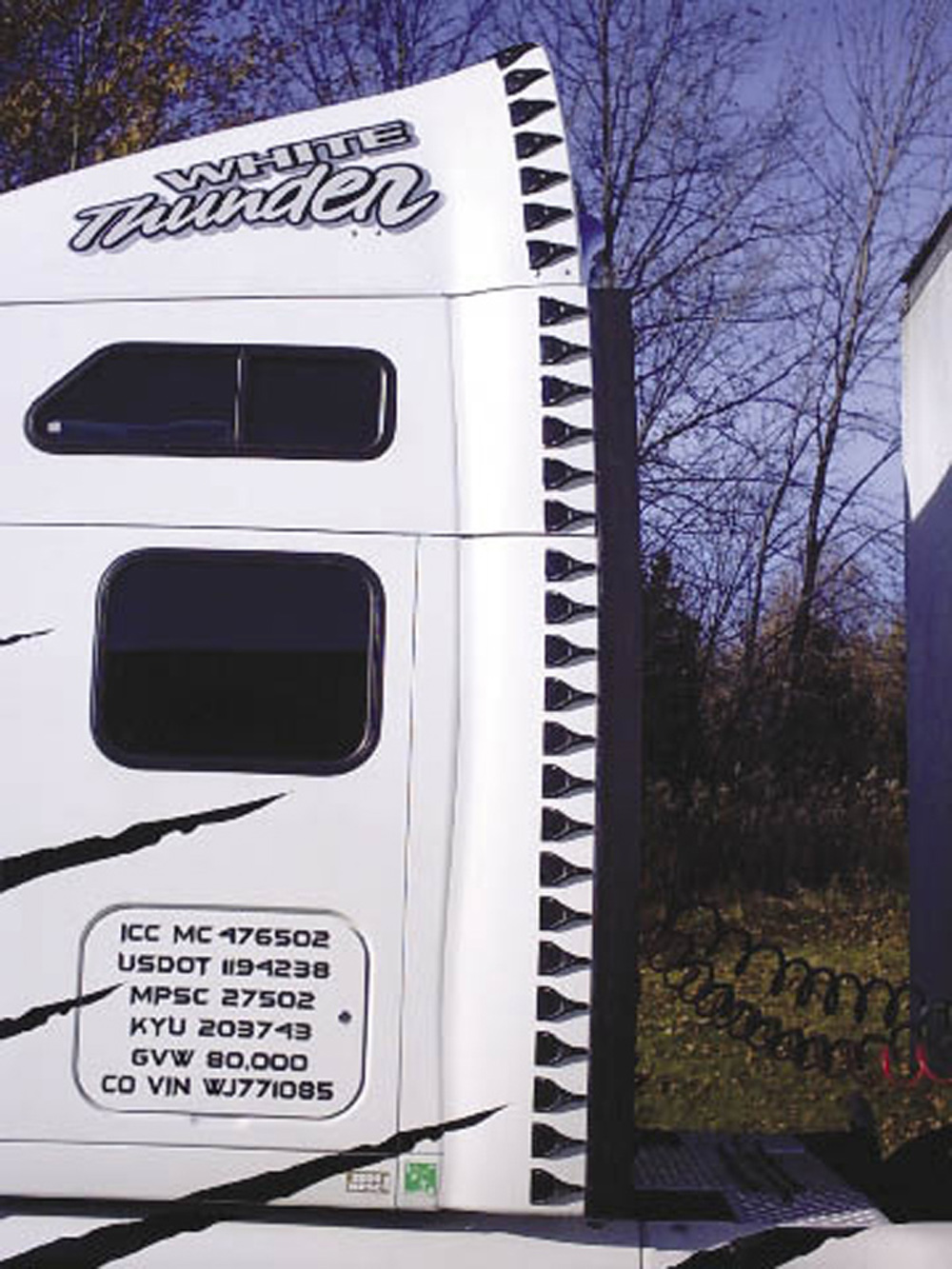
Airtabs create controlled, counter-rotating vortices to bridge the gap between tractor and trailer or control airflow past the rear of the vehicle.
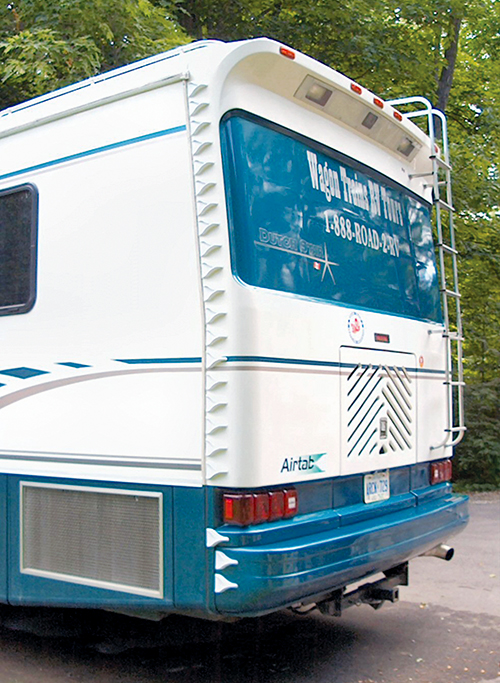
Effective on any vehicle with more than a 30-degree slope to the rear, Airtabs see many applications in addition to trucks.
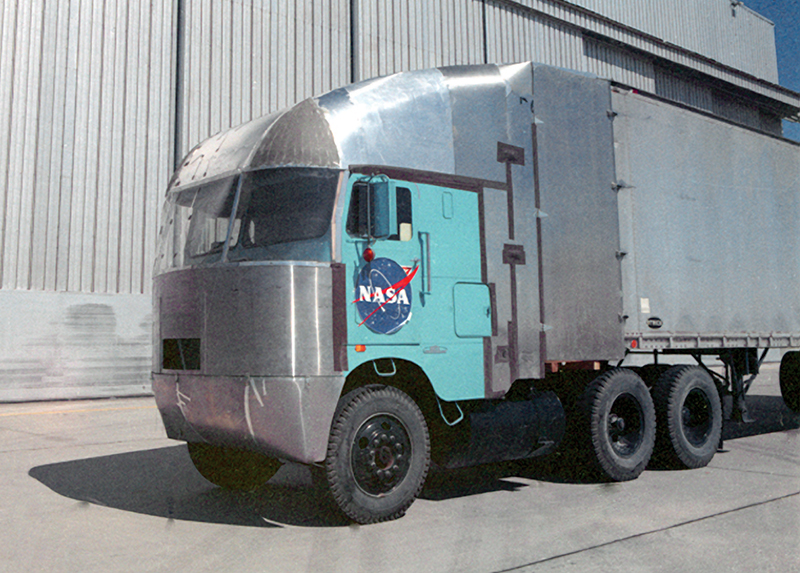
A cab over engine tractor trailer was leased by Dryden, tested, and modified to reduce aerodynamic drag.