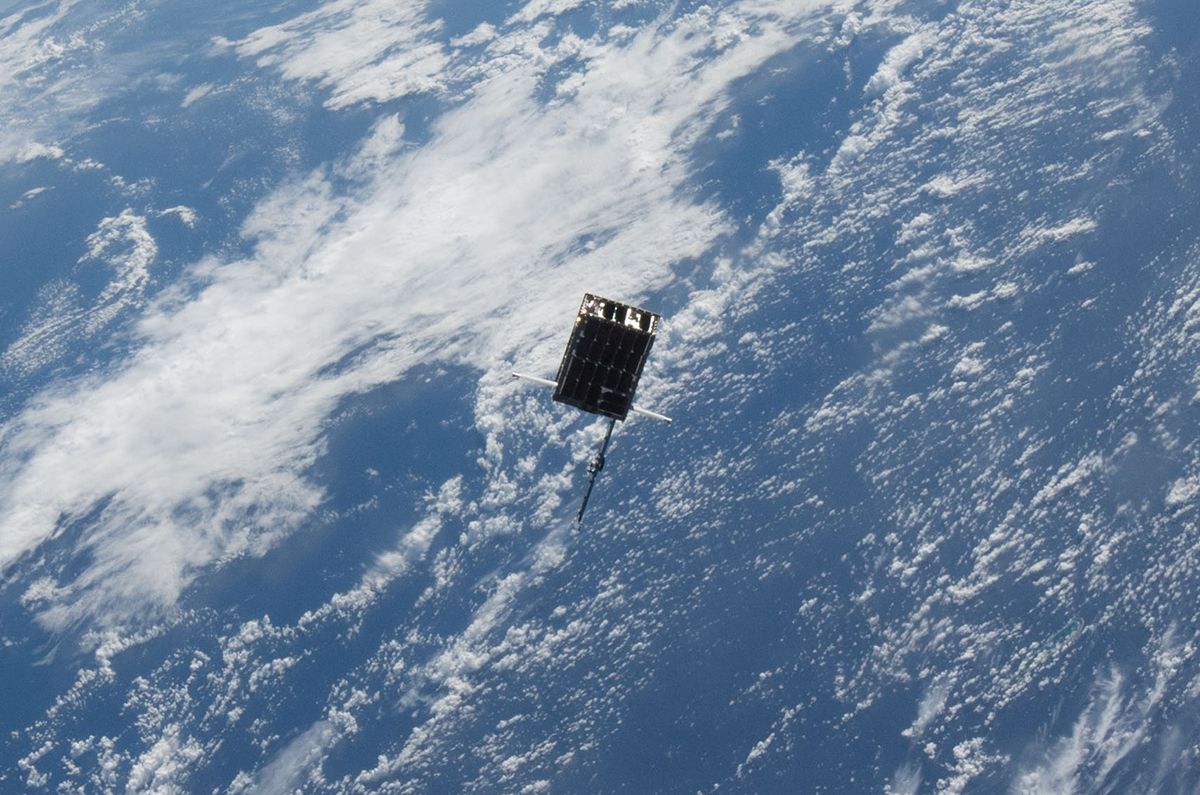
A Huge Development for Tiny Satellites
Subheadline
NASA-developed mechanism improves reliability of small satellites
For satellites to fit into their enclosures on top of a rocket, they often launch folded up into a much smaller size, then unfurl any external equipment once they reach orbit. These parts, such as solar panels and antennas, are known as deployables. While these systems have been refined for large satellites, engineers working on smaller orbiters like CubeSats have had difficulties miniaturizing the mechanisms that release deployables.
One of the most popular solutions has been a thin monofilament rope, similar to fishing line, that secures deployables to the body of the satellite. This line is then burned by a small heating element to release the equipment. However, this process is unreliable, and the exposed nature of the wire causes a high failure rate on these components. Luis Santos, currently the chief engineer of the small satellite office at NASA’s Goddard Space Flight Center in Greenbelt, Maryland, saw the issues facing deployables on CubeSats and thought there could be a better solution.
“I just thought, what would be the best way to hold the deployables in place that is repeatable?” Santos said.
Santos separated the problem into two areas: holding the deployables securely and a movement initiation device. The resulting system combines a nichrome wire and a type of easily molded plastic to initiate the release movement while another mechanism holds and releases the deployable instead of wire alone. The release mechanism became much sturdier and could still be released using the same kind of heating approach, which saves volume and mass in comparison to other mechanisms. Santos named this new method the Diminutive Assembly for Nanosatellite Deployables (DANY).
“Around that time, I had my first son, and his name was Daniel, so I called it a ‘Danny’ mechanism,” Santos joked.
Some prototypes were first tested aboard sounding rockets launched from NASA’s Wallops Flight Facility on Wallops Island, Virginia, and later demonstrated on the Dellingr CubeSat mission launched from the space station. The technology proved its worth in space, able to deploy antennas and sensors flawlessly. Soon after, it started to receive interest from the private sector.
“It’s a thermal-based actuator, so it kind of fits into our thermal products that we design and develop,” said Scott Schick, president of Thermal Management Technologies LLC (TMT) of Logan, Utah, the first company to license DANY for commercial use.
As the company’s name implies, its primary business is in providing thermal controls such as radiators for spacecraft and industrial applications. The company was looking for a release mechanism for their deployable radiators, and DANY seemed to be a good fit. While they officially licensed the patent in 2018, the engineers at TMT found the component was not easily reproduced on an industrial scale and needed more development time to be commercially ready. During the work to build out the technology’s capabilities, Schick said, they had extensive communications with Santos and his office at Goddard.
TMT’s commercial version of DANY is called the Gecko Actuator, owing to the namesake lizard’s ability to maintain its grip until release is necessary. In addition to governmental and nongovernmental institutions looking to build CubeSats, several commercial companies have purchased them as well. These use them in applications ranging from Earth-observing satellites to small communications orbiters.
“Anyone who has an antenna could use this, and every spacecraft has an antenna,” Schick said.
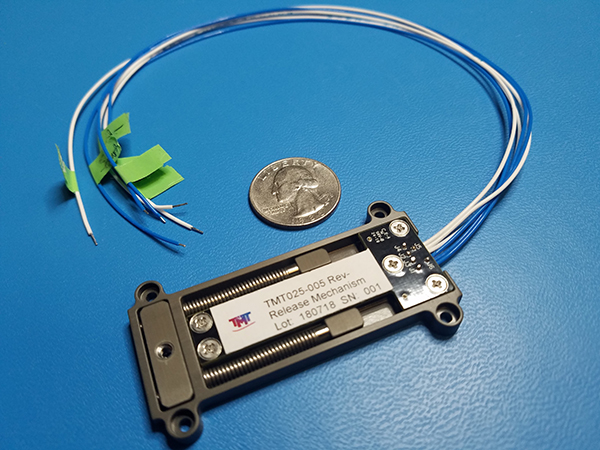
The Gecko Actuator built by Thermal Management Technologies (TMT) is extremely compact. This allows CubeSats to fit large attachments like antennas, radiators, or solar panels into the limited payload space aboard rockets. Credit: Thermal Management Technologies LLC
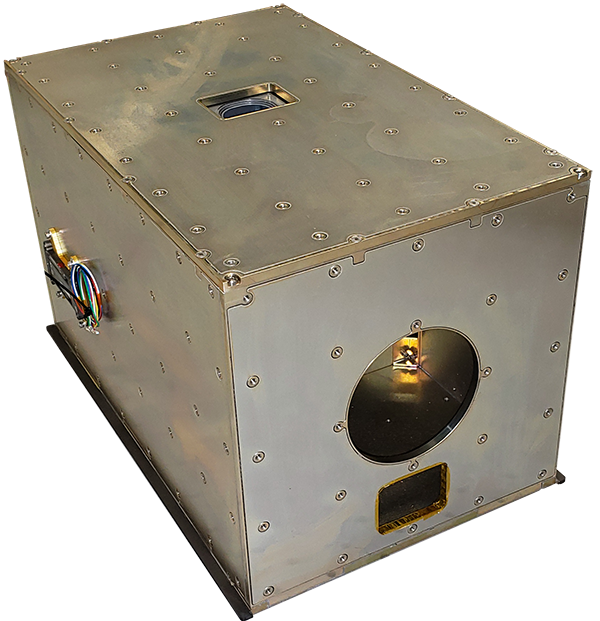
This small satellite features a Gecko Actuator release mechanism on the side. Originally developed by NASA, this system was licensed by TMT so it could be used aboard commercial satellites. Credit: Thermal Management Technologies LLC
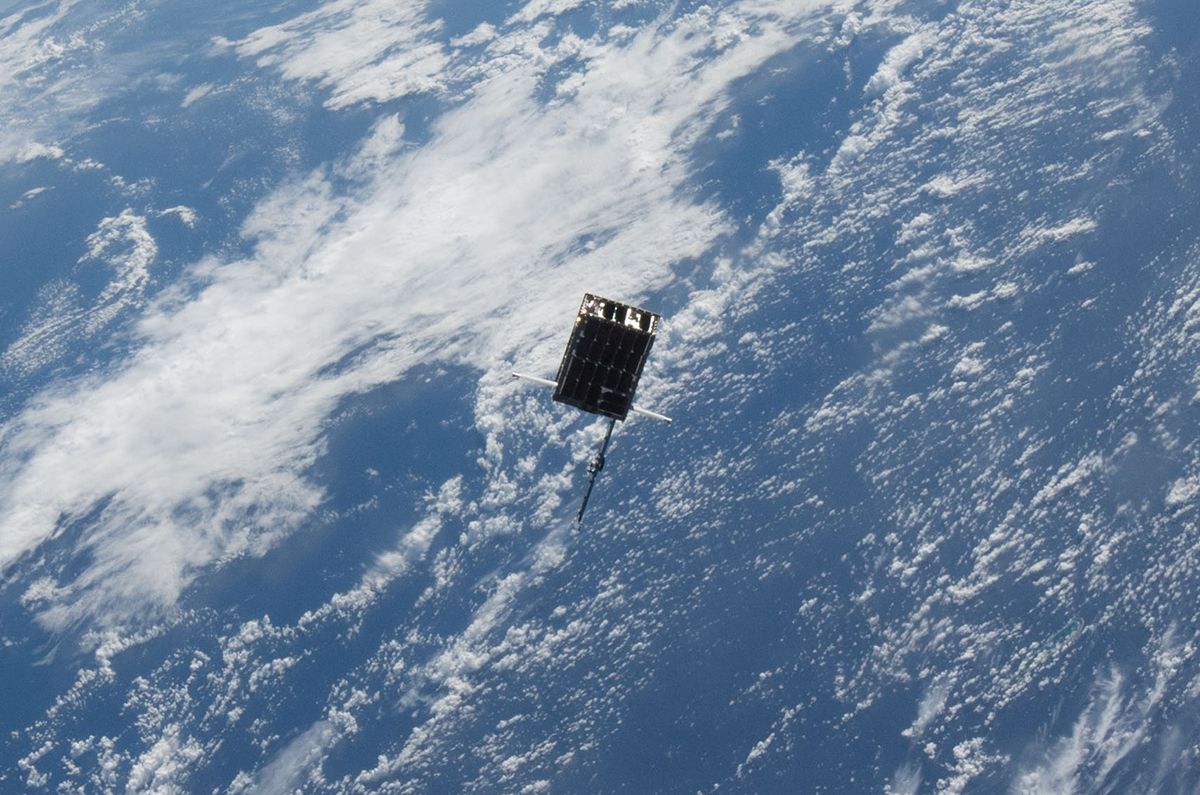
The Dellingr CubeSat falls into orbit shortly after its release from the International Space Station in 2017. The antennas on the small satellite were deployed as a test of the Diminutive Assembly for Nanosatellite Deployables (DANY) mechanism, which was later developed into the Gecko Actuator. Credit: NASA