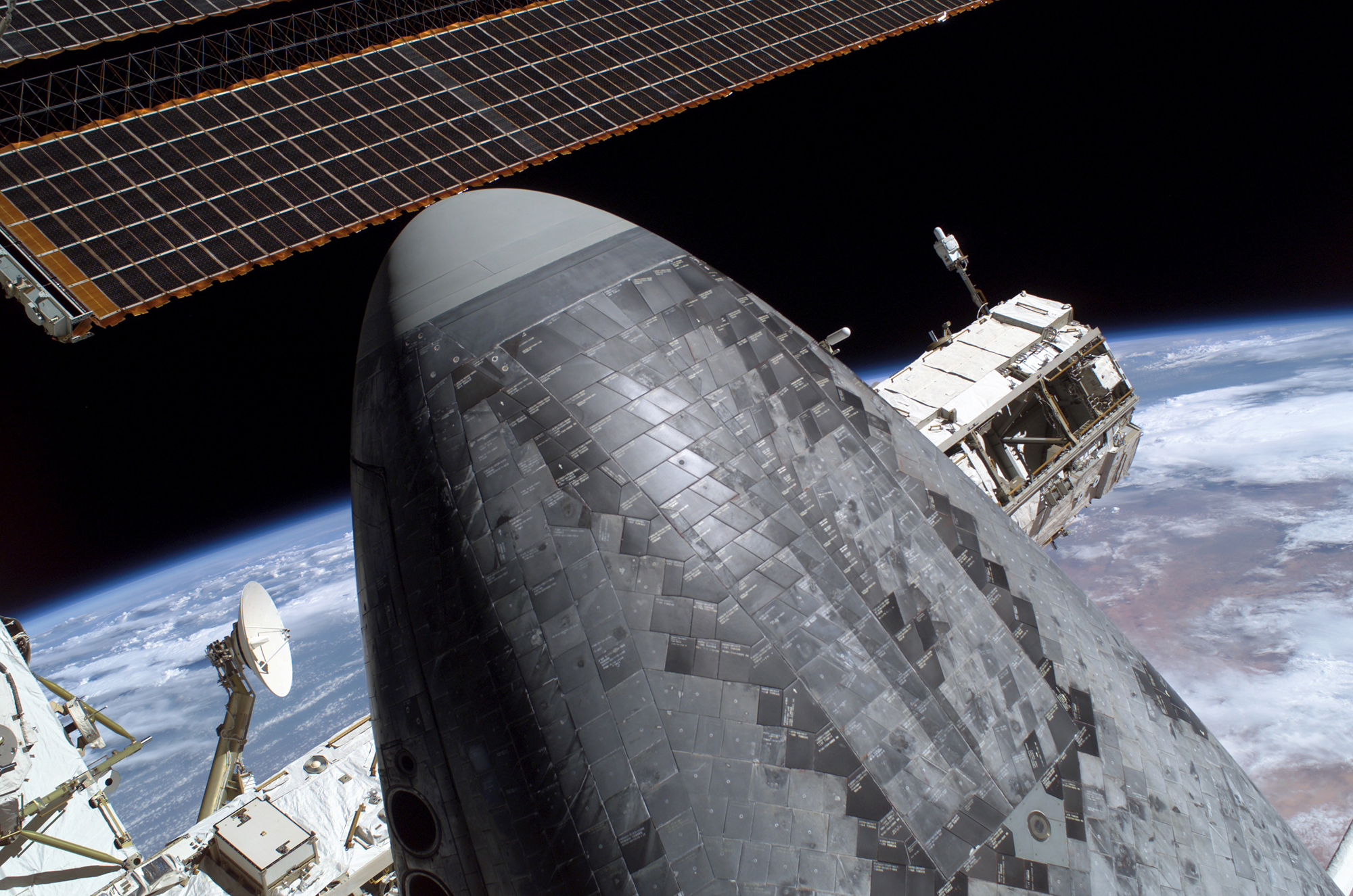
Launch, Return, Repeat
Subheadline
A NASA thermal protection system enables reuse of commercial spacecraft
The dream of reusable spacecraft became reality when NASA developed the space shuttles to carry the International Space Station into orbit one module at a time. Many of the technologies created for that purpose are considered flight-ready and now could aid the safe return of commercial space vehicles. Canopy Aerospace Inc. is offering one of those technologies — the thermal protection system (TPS).
By participating in NASA’s Startup Studio, the Littleton, Colorado-based Canopy learned about a specific TPS called alumina-enhanced thermal barrier (AETB) with a reaction-cured glass coating, usually referred to simply as space shuttle tile.
FedTech, a venture firm that specializes in connecting entrepreneurs with technologies from federal labs, teamed up with NASA’s Technology Transfer Expansion (T2X) initiative to introduce entrepreneurs to the agency’s technologies ready for commercialization through the Startup Studio. During one-on-one meetings with High Temperature Reusable TPS Program Manager Jay Feldman, senior materials researcher at NASA’s Ames Research Center in Silicon Valley, California, Matt Shieh recognized an unmet need.
“The material itself is a flight-proven technology that NASA has already qualified, tested, and flown but has not been commercialized for industry use,” said Shieh, who is now CEO of Canopy. Under a Space Act Agreement, Feldman’s team is teaching the company how to reproduce the same material NASA used on the underside of the shuttle vehicles.
The shuttle tiles dispersed the heat generated when the spacecraft entered Earth’s upper atmosphere at speeds greater than Mach 25. The porous ceramic material was formed into a specific shape and then coated with a black glaze of borosilicate.
“It’s essentially a very highly engineered form of sand combined with other ingredients that has this incredible performance, where it can repeatedly withstand thousands of degrees, almost 3,000°F,” said Feldman. And the tiles’ light weight helps reduce flight costs for a launch vehicle and frees up weight for customer payloads.
With commercial space companies developing flight schedules ranging from daily to weekly, Feldman believes reusable vehicles are the only way to deliver cost-effective launch service. The heritage TPS technology eliminates the time and expense of developing an entirely new system, flight testing it, and then building out the infrastructure for manufacturing.
Another category of TPS is ablative, meaning they disperse heat by shedding layers of material. That single-use approach changes the aerodynamics of the vehicle structure, making it a lot more complicated to use, and requires costly refurbishment, according to Shieh.
The Canopy tiles are scheduled for testing at the Ames Arc Jet Complex, which replicates the condition of atmospheric reentry.
Working at full capacity, the company can manufacture up to 200 custom pieces per month. This pace likely won’t be enough to satisfy the already unmet and growing demand, but the current process is a first step on the way to a new type of manufacturing. While Canopy fills orders, it’s also working with NASA to create a 3D printed material that’s comparable to space shuttle tiles but eliminates multiple steps in the current manufacturing process.
“There’s a lot of technology that needs to be transitioned out of NASA for the commercial space industry to flourish and get to market. The Technology Transfer program makes that really easy,” said Shieh. “Working with NASA has been a really great experience.”
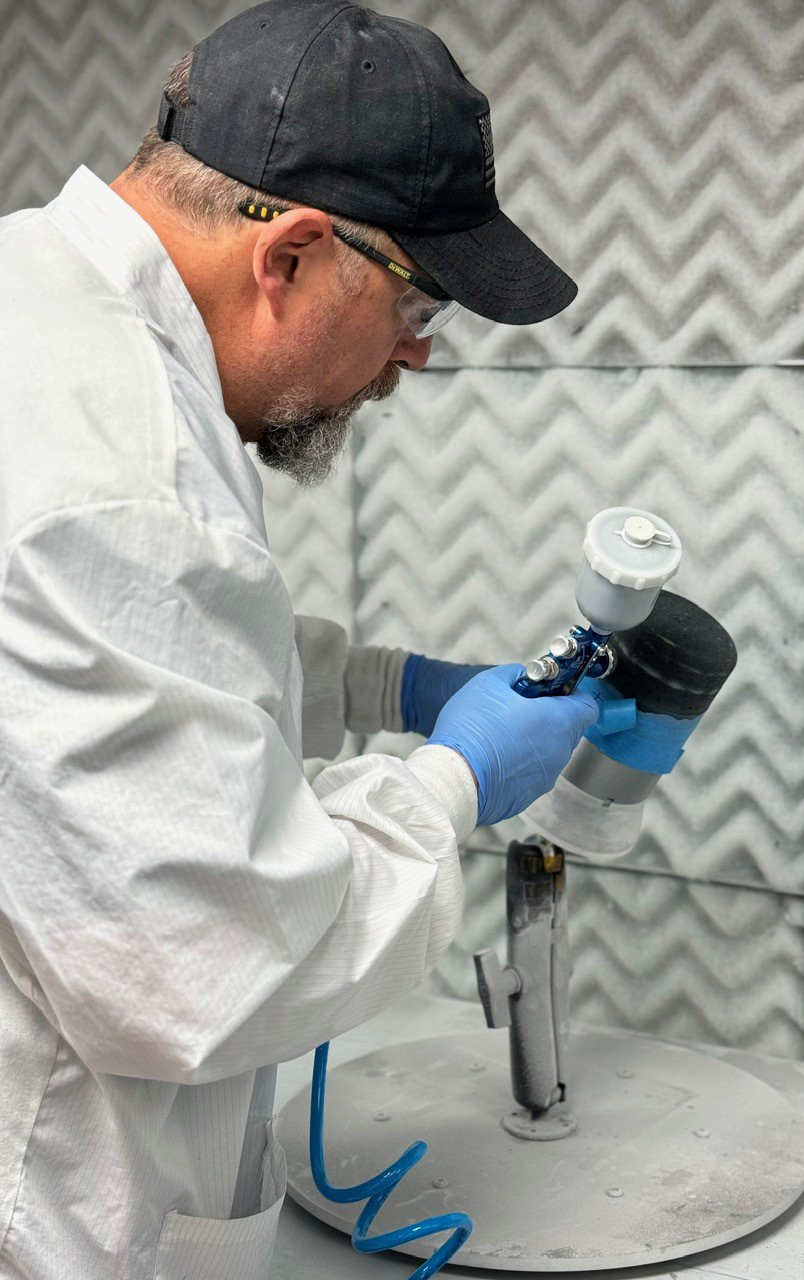
Reusable rockets will allow commercial space companies to lower the cost and increase the frequency of launch services. But they need shielding to survive the heat of reentry, so Canopy Aerospace is manufacturing the proven TPS developed by NASA. Credit: Canopy Aerospace Inc.
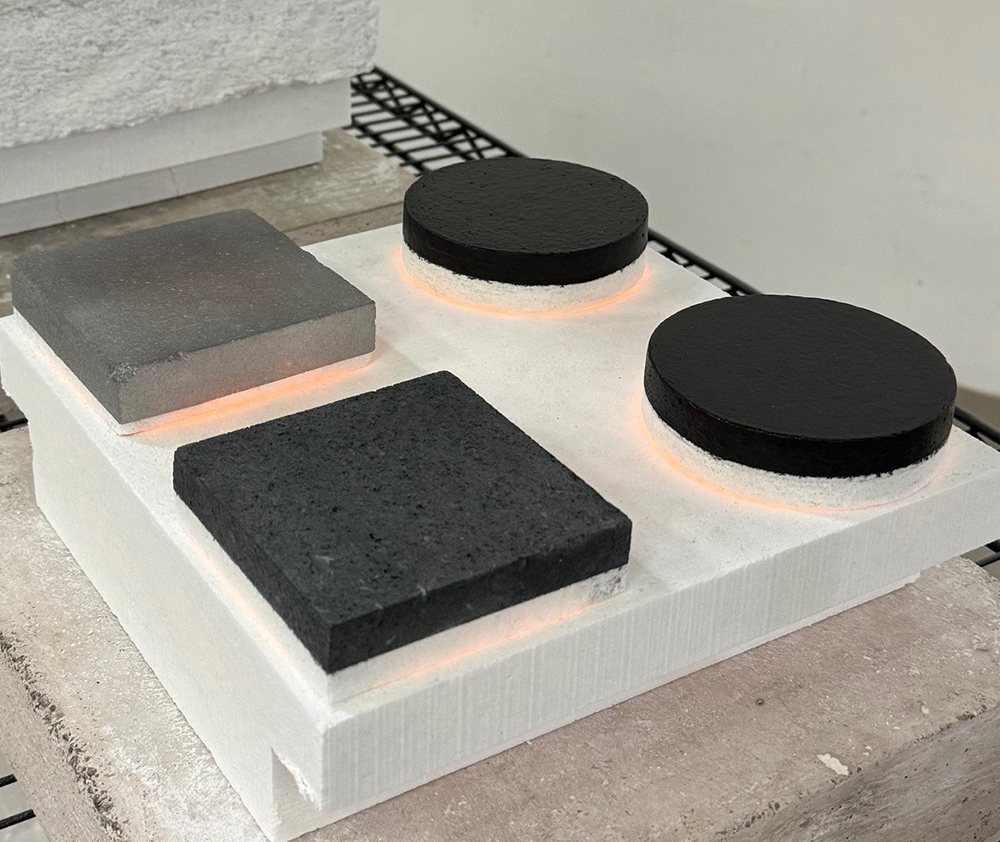
Canopy Aerospace learned how to manufacture space shuttle tiles like the ones shown here to meet the growing demand for a lightweight TPS for rockets and other vehicles that will be reused by commercial space companies. Credit: Canopy Aerospace Inc.
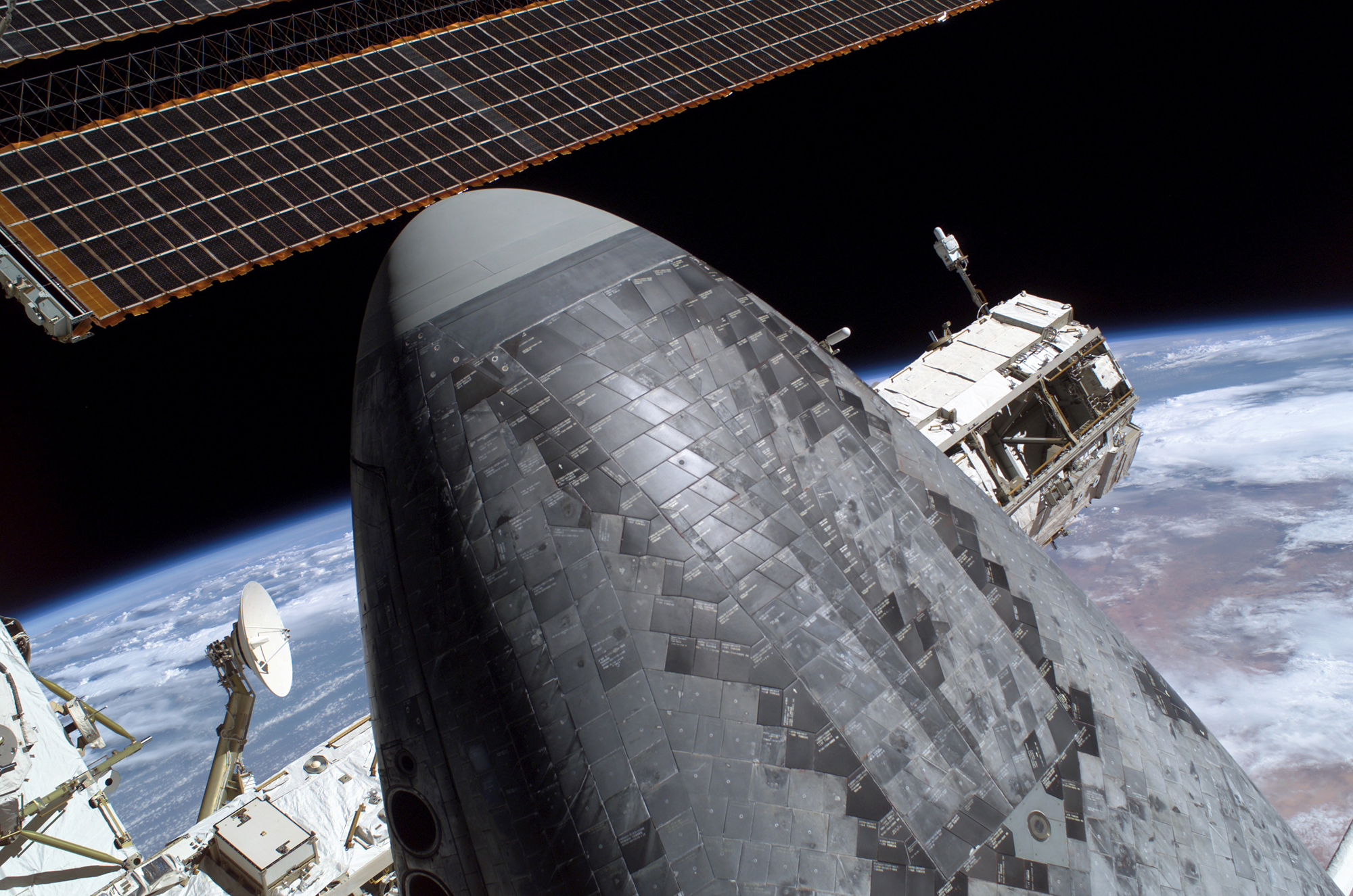
This picture of the underside of the space shuttle Discovery’s nosecone shows the thermal protection system (TPS) tiles that Canopy Aerospace now manufactures. Credit: NASA