Intelligent Fasteners
If you are facing that oft-quoted engineering truism, that a system is only as good as its weakest link, consider the world's first, high-temperature-resistant, "intelligent" fastener.
A product of Ultrafast, Inc. of Malvern, Pennsylvania, this fastening technology was originally developed under a Small Business Innovation Research (SBIR) contract managed by Marshall Space Flight Center. The NASA partnership was born by a need for critical-fastening appraisal and validation of spacecraft segments that are coupled together in space. In-orbit assembly requires both lightweight wrenches for enhanced robot-arm mobility as well as remote fastener-load inspection capability.
The space solution yielded an innovation that is likely to revolutionize manufacturing assembly, particularly in the automobile building industry.
Ultrafast's "intelligent bolt" utilizes a piezoelectric thin-film deposited directly on one end of the fastener. When electrically excited by an Ultrafast tool, tensile loads can be accurately controlled during the bolt tightening process. Insufficient bolt preload is usually the root cause of joint failure resulting from joint separation, bolt loosening or fatigue.
In effect, a bolt topped by the thin-film technology—at a cost of just pennies per fastener—functions as a transducer for measurement and recording of bolt tensile load. The coating itself is less than 0.001 inch thick and is durable, deposited on the fastener by sputtering. This is a vacuum process that has long found practical application in everything from integrated circuits to reflective coatings on glass or decorative coatings on plastic. Moreover, the coating can be applied to all forms of existing fasteners without changing the basic design or metallurgy of the item undergoing the process.
Ultrasonic measurements of a fastener are possible by using piezoelectric thin films, in both longitudinal and transverse directions, heretofore impractical in typical fasteners. Ultrafast technology uses the relationship between the speed of ultrasonic waves in a material and the stress applied to the material as its basis for computing load measurements. The idea is that the "time-of-flight" of an ultrasonic signal traveling in a fastener will increase as the load on the fastener is increased.
Ultrafast's intelligent-bolt technology deletes the self-defeating procedure of having to untighten the fastener, and thus upset the joint, during inspection and maintenance. Even the smallest fastener can be turned into latent sources of information in numerous applications.
For the automotive industry, the advantages of applying the Ultrafast system are distinct. Safety-critical components like powertrains, steering systems and brakes can achieve higher reliability while minimizing service costs and other impacts from joint failure. Use of high speed impact or impulse wrenches to improve joint integrity and inspection can lower costs in automotive body manufacturing by reducing joint assembly times.
Practical use of ultrasonic thin-film fasteners go beyond the realm of automobile, aircraft, and space applications. For instance, from computer disk drive assemblies to forklifts. In the nuclear field, from small flanges to large pressure vessels. For chemical processing, critical-fastening applications include offshore platforms to pipes. In construction, the appeal of Ultrafast's innovation can be applied to buildings and bridges.
Ultrafast expects sales to exceed $100 million in a few years. Ultrafast has licensed two major European tool companies to supply power tools for automotive assembly and is establishing worldwide fastener coating services through its Ultracoat subsidiaries.
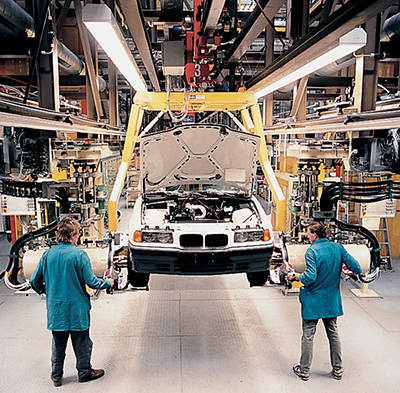
Ultrafast's "intelligent" fasteners are expected to be a boon to automobile manufacturers, assuring that more precise loads are applied during bolt tightening.