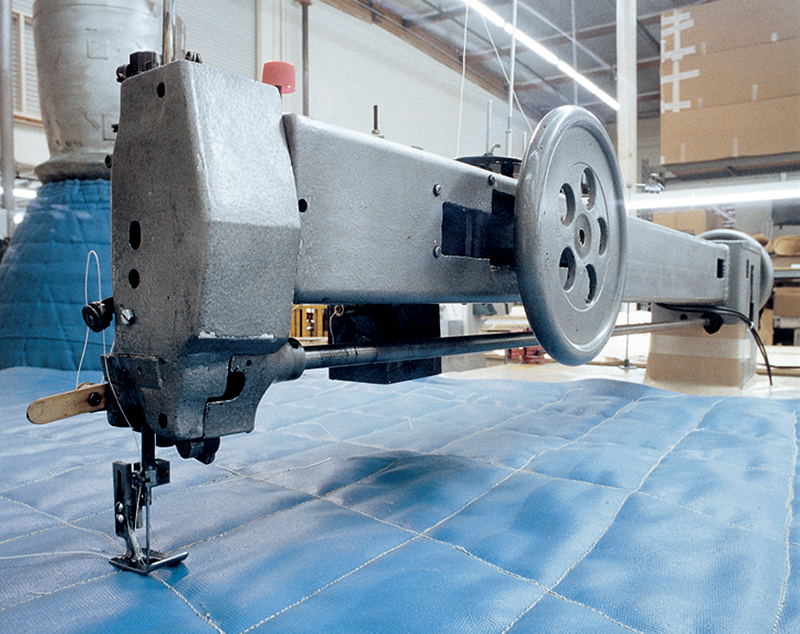
Reusable Surface Insulation
Searing heat engulfs a Space Shuttle orbiter as it plunges through the atmosphere en route to a touchdown on Earth. Protecting select areas of the space plane during its fiery dive is Advanced Flexible Reusable Surface Insulation (AFRSI).
AFRSI was developed by Ames Research Center then integrated into the Space Shuttle by Rockwell International. Production of the AFRSI was transferred in 1974 to Hi-Temp Insulation Inc. of Camarillo, California.
For over 22 years, Hi-Temp has provided insulation blankets for the external leeward surfaces of the Space Shuttle. Hi-Temp created many new technologies to meet the requirements of the Space Shuttle program. A combination of low weight and high thermal efficiency demanded an examination of new materials and fabrication techniques. Material must resist temperatures of some 2,000 degrees Fahrenheit for 15 minutes with no burn through.
On low-temperature areas of a Space Shuttle, the company made molded fiberglass insulation covered with polyester film. Hydraulic lines and system components are wrapped with this insulation.
A Shuttle orbiter's payload bay is protected from heat by using Hi-Temp's two-blanket insulation system. Lastly, the Space Shuttle's main engine nozzles feature ceramic insulation. This insulation is constructed to withstand temperatures to 2,600 degrees Fahrenheit and extreme vibration.
Improvements to the insulation material by Hi-Temp with the assistance of NASA gives it the ability to withstand heating and cooling cycles; rapid and fluctuating temperature changes; continuous vibration and gravitational stress; and contact with aircraft engine contaminants.
The outstanding virtues of Hi-Temp's range of insulation products have enabled the firm to use this innovation in many other ways. These include: insulation blanket to cover aircraft parts, such as engine exhaust ducts; fire barrier material to protect aircraft engine cowlings; molded fiberglass insulation blankets for acoustical protection; and in aircraft rescue fire fighter suits.
Hi-Temp's Space Shuttle work has nurtured a unique proficiency, with many new production techniques now available that can be geared to both aerospace and commercial markets.
Working closely with material manufacturers, Hi-Temp has fabricated blankets using carbon, graphite, ceramic, and nicalon. To protect and seal sewn insulation blankets, Hi-Temp uses a wide variety of facing materials including coated fabrics, mylars, and films. In addition, using stainless steel thread, foils up to .002 thick can be sewn to insulation blankets for liquid proof protection at high operating temperatures. This skill has been applied to such critical programs as the Trident missile, Delta launch vehicle, as well as the Space Shuttle.
Equipment to fulfill tasks at Hi-Temp include many special machines such as rigidizing rollers for strengthening metal foils; a special heated platen press for bonding structural components; heat-sealing machines; and welders for stainless steel and inconel.
A Fire Protection Division of Hi-Temp Insulation has been established, offering the first suit designed exclusively by and for aircraft rescue fire fighters. Offering great mobility, comfort and flexibility, the fire fighting suit uses proprietary insulating materials that enable the suit to weigh far less than other heat-protecting apparel. From the inside out, the Hi-Temp fire fighting suit retards heat, scalding steam, flammable fumes, and molten liquids.
Hi-Temp is a supplier to the Los Angeles City Fire Department as well as other major U.S. civil and military fire departments.
At its start in the mid-1970s, Hi-Temp relied heavily on government projects, becoming 90 percent government dependent. It is now estimated that this growing concern has become 85 percent commercial dependent, with about 15 percent of its work done under government contract.
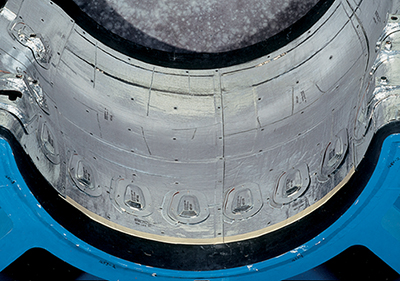
Hi-Temp's insulation is used on the Boeing 777. It is assembled on a check fixture and includes a quilted insulation core.
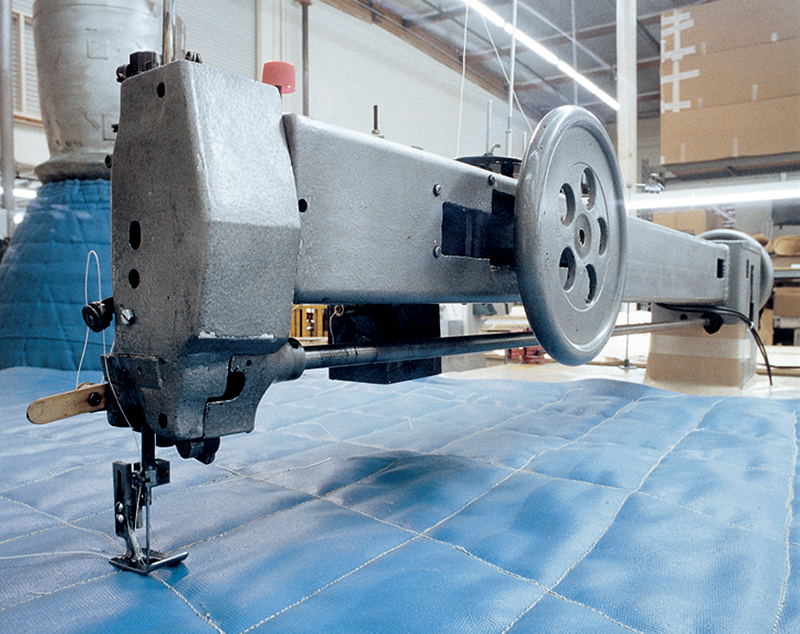
Insulation technology based on protecting the Space Shuttle during reentry has been adopted by the aircraft industry and other commercial interests. A quilting machine is used to fabricate thermal blankets for the Space Shuttle.