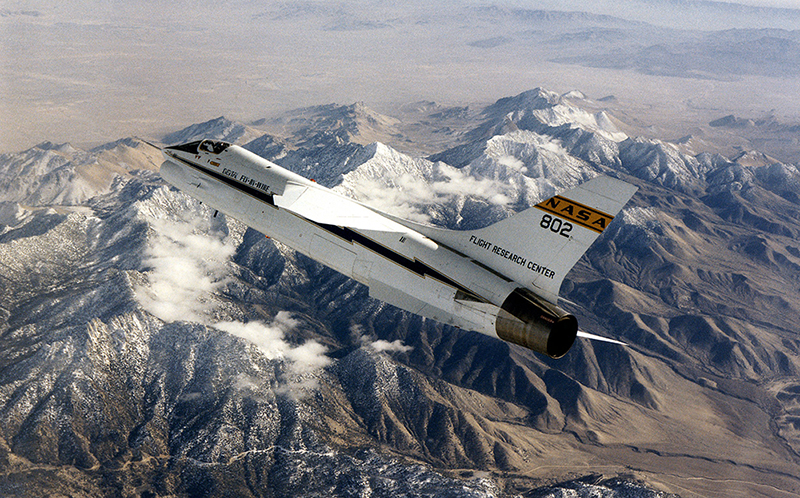
Fly-by-Wire Systems Enable Safer, More Efficient Flight
Fly-by-Wire Systems Enable Safer, More Efficient Flight
NASA Technology
In 1961, not long after NASA received the imperative from President John F. Kennedy to land a man on the Moon within the decade, then-NASA administrator James Webb posed a question to Charles Stark “Doc” Draper, head of the Massachusetts Institute of Technology (MIT) Instrumentation Lab. Webb wanted to know if it was possible to create a guidance system that could lead a man to the Moon and return him safely to Earth.
Doc Draper had pioneered the field of inertial navigation—the use of instruments such as gyroscopes and accelerometers to provide guidance for a vehicle—and the Lab had developed the guidance systems for the Nation’s first ballistic missiles and even conducted work in the 1950s on an autonomous probe that could find its way to Mars and back.
Doc Draper’s answer was a definitive “Yes.”
Known today as Draper Laboratory, an independent, nonprofit institution based in Cambridge, Massachusetts, the MIT Instrumentation Laboratory became the first major contractor for the Apollo program. Working with other contractors, the lab developed the Apollo Primary Guidance, Navigation, and Control System (PGNCS, pronounced “pings”). Consisting of an inertial measurement unit, optical and other components, the system had at its heart the Apollo Guidance Computer. Designed and programmed by the Lab and largely built by Raytheon, the computer would be the brain for both the Apollo Command Module and the Lunar Module that would deliver the first astronauts to the Moon’s surface. To do this, it had to be faultless.
“It had to work and it had to work flawlessly. There was no possibility for repair,” says Darryl Sargent, vice president of programs for Draper.
And it did. Throughout the course of the Apollo program, the computer never experienced a failure. In addition to enabling the PGNCS system that in turn enabled the Moon landings, the computer also contributed to the rescue of Apollo 13 through the use of a program that helped push the damaged Command Module into a safe course back to Earth.
Meanwhile, at NASA’s Flight Research Center in California (now known as Dryden Flight Research Center), aeronautics engineers were asking questions about how computers could contribute to flight on Earth—questions that the Apollo Guidance Computer would help answer.
Partnership
At that point, mechanically controlled aircraft—in which the vehicle’s control surfaces are operated through cables and pushrods connecting the aerodynamic surfaces to the pilot’s control sticks and rudder pedals—were the norm in aviation. In 1970, a Dryden team visited NASA Headquarters proposing an advanced aircraft controlled by an analog fly-by-wire system with no mechanical backup.
The idea of flying an aircraft electronically was not a new one. In a fly-by-wire system, a computer collects sensor data from the pilot’s controls and sends those signals via wires to actuators that decode the signals and move the aircraft’s control surfaces accordingly. Dryden researchers had developed significant experience in electronic flight controls through the development of experimental aircraft; in fact, the Lunar Landing Training Vehicle NASA used to train the Apollo spacecraft commanders employed an analog fly-by-wire system with no mechanical backup—making it the first genuine fly-by-wire vehicle. But these systems all used analog computers, as opposed to digital ones. Electronic analog computers use variations in the physical properties of electricity to represent numbers; digital computers use binary code. Though slower for certain functions than their analog counterparts, digital computers can store large quantities of data and can be programmed with complex software.
While the actual aircraft the Dryden team proposed proved too futuristic to pursue, the question was raised, “What about a digital fly-by-wire system?”
“The answer was that there were no flight qualified digital computers for airplanes,” says Ken Szalai, then a young engineer at Dryden. An objection was raised by a well-known figure (and former Dryden test pilot) in what was then NASA’s Office of Advanced Research and Technology: Neil Armstrong. He had recently flown to the Moon and back with his life entrusted to the guidance of a digital computer. Szalai approached Draper Laboratory, the architect of the Apollo PGNCS, to see whether it could be adapted to test the feasibility of digital fly-by-wire for aircraft. The answer, again, was “Yes.”
Through Armstrong’s support, and that of U.S. Navy Vice Admiral Donald Engen, Dryden acquired a trio of F-8C Crusaders from the Navy and, working with Draper, the Center installed an adapted extra Apollo PGNCS on one of the planes, which became the Digital Fly-by-Wire (DFBW) research aircraft. Another of the F-8s was converted into an “Iron Bird” ground-based simulator for testing the flight software and training pilots, and the third F-8 was used to familiarize test pilots with the aircraft.
“The Apollo system wasn’t an ideal configuration for airplane control,” says Philip Felleman, who was the DFBW program manager for Draper. “But it did have one big thing going for it: It was highly reliable.”
The DFBW program (also commonly known as the F-8 program) was divided into two phases. In Phase I, the objective was to demonstrate the viability of flying an aircraft by digital computer alone. The first use of an analog fly-by-wire system in an aircraft was in early May of 1972 by the U.S. Air Force YF-4E Control Configured Vehicle. About three weeks later, on May 25, 1972, Gary Krier piloted the DFBW research aircraft on the first flight of an aircraft controlled by digital computer. The plane had no mechanical backup, only a three-computer analog emergency system. The backup system was not needed for that flight, nor any other for the length of the program.
More than 30 successful flights later, Phase I finished having proven a digital computer could be used to fly an aircraft. The next question was how to make it practical. Commercial digital computers did not have the reliability of the Apollo Guidance Computer. A DFBW system would require more than just one or even two computers to operate with any acceptable assurance of safety. In Phase II of the DFBW program, Dryden collaborated with Draper, Langley Research Center, and others to create the hardware and software necessary for a highly reliable, fault-tolerant, three-computer DFBW system.
“The big job was to be able to manage the redundancy, to be able to tolerate a failure and still be able to fly,” says Felleman. To do that, Szalai says, “We worked untold hours to develop the logic schemes, and then we had to test it and verify that it worked in all the various combinations.”
Draper, meanwhile, was also working with NASA on the guidance, navigation, and control system for an entirely new kind of aircraft: the Space Shuttle. Employing a quad-redundant digital fly-by-wire system, the shuttle benefited from the work done during the DFBW program, which in one case identified a hardware issue with the flight computers (both programs used IBM AP-101s), and in another helped solve a potentially hazardous problem with pilot-induced oscillation that occurred during the final test flight of the Space Shuttle Enterprise.
“There was feedback between the programs, mostly from us to the shuttle program because we were doing everything first,” says Felleman.
The DFBW program’s final flight occurred on April 2, 1985—the last of more than 200 successful flights that collectively provided the impetus for changing the way aircraft are designed and flown around the world.
Benefits
“Some of the techniques we developed at that time are still being used, and that spawned the digital fly-by-wire revolution,” says Szalai, who went on to become Dryden’s center director before retiring in 1998. “We communicated with all of the major airframe manufacturers and were able to transfer a lot of the technology.”
The first commercial airliner to fly with DFBW was the Airbus 320 in 1987, followed by Boeing’s 777 in 1994. Today, the technology features in a number of aircraft from both manufacturers. For commercial aircraft, the technology replaces heavy mechanical systems, allowing airlines to benefit from greater fuel efficiency or carry more passengers and cargo. The heightened responsiveness of DFBW-enabled aircraft allows pilots to provide a smoother flight, and the system’s redundancies help ensure safe operation of the vehicle. Mechanical maintenance needs are also reduced, saving costs and time spent on upkeep and repairs of the mechanical systems and reducing the chance of failures.
“Now, when you fly any major, large airplane, you’re flying a digital fly-by-wire system based on the technology from the F-8 program,” says Sargent. Even smaller aircraft are now incorporating the technology; in 2005, the Dassault Falcon 7X became the first business jet with a DFBW system.
One of the biggest contributions to aviation to emerge from the DFBW program is the ability to support entirely new forms of aircraft, says Szalai. The enhanced control capabilities of a DFBW system allow pilots to fly aerodynamically unstable aircraft that could not be controlled otherwise. While current aircraft are still designed as aerodynamically stable to at least some degree, unstable aircraft promise higher performance—such as increased maneuverability in fighter jets and minimized drag and increased range in civil transport—and future aircraft may capitalize on this benefit.
“Digital fly-by-wire has unshackled designers from the rules of the 1950s and 1960s, so you end up with vehicles like the Space Shuttle, the B-2 bomber, and the F-117. You couldn’t have these kinds of aircraft without a fly-by-wire system,” says Szalai. In addition to those, Szalai notes, many other military aircraft benefit from DFBW systems, including the F/A-18 and F-22. The F-16 began with an analog fly-by-wire system—the first production aircraft with fly-by-wire—and later switched to DFBW controls.
The benefits of digital computer vehicle control systems as demonstrated by the DFBW program are not limited to the skies, however. The electronic cruise control features found in many automobiles are enabled by drive-by-wire technology, as are antilock braking and electronic stability control systems, both of which significantly enhance safety. Auto and motorcycle manufacturers have also incorporated electronic throttles into their vehicles—the first being the BMW 7 series in 1988—eliminating moving mechanical systems between the accelerator and the engine.
For Draper, the outcomes of the DFBW program have served to enhance the Lab’s expertise and reputation in the field of guidance, navigation, and control systems.
“What NASA has meant to us is a steady stream of hard problems to work on. The skills we learned and technologies we developed from our work with NASA we then turn around and apply as broadly as possible,” says Sargent. Beyond aircraft, Draper has applied the DFBW technology to a range of unmanned underwater vehicles and the U.S. Navy’s Seawolf class submarines. “A redundant, fault tolerant, ‘swim-by-wire’ system,” Sargent says. And Draper recently delivered a DFBW system to Orbital Sciences for the company’s launch vehicle and Cygnus capsule, being developed in support of NASA’s Commercial Orbital Transportation Services (COTS) program.
“You can draw direct heritage from the F-8 system to the systems that fly the Space Shuttle and the International Space Station, and now we’ve taken that technology into the COTS program. That says a lot for the power of what was done back then,” Sargent says.
Szalai recalls countless hours in the desert where Dryden is located, standing up in a lean-to hangar with the F-8 Iron Bird simulator and a computer test set, working out software anomalies, trudging up and down the steps to the cockpit to work with the pilots in training. The hangar was drafty, dusty. Sand slid in under the roll-down door.
“One of the values of flight research is that reality meets with dreams and visions,” Szalai says. “They meet and they clash. You have to solve the real world issues. You can’t always take a picture of the spinoff. Sometimes it’s showing that you can do something.”
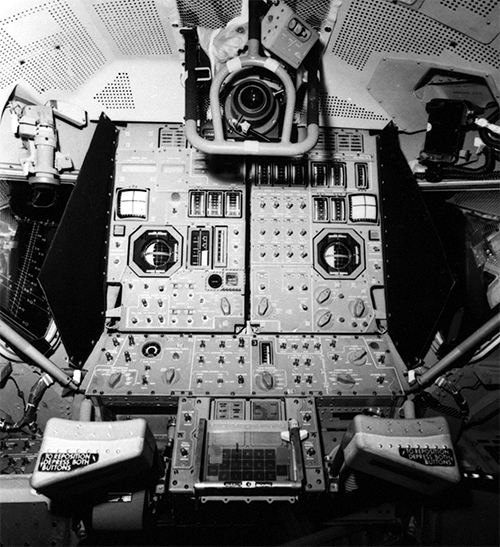
The Primary Guidance, Navigation, and Control System of the Apollo Lunar Module. The display and keyboard (DSKY, pronounced “diskey”) interface used by the astronauts to input commands can be seen in the bottom center of the image.
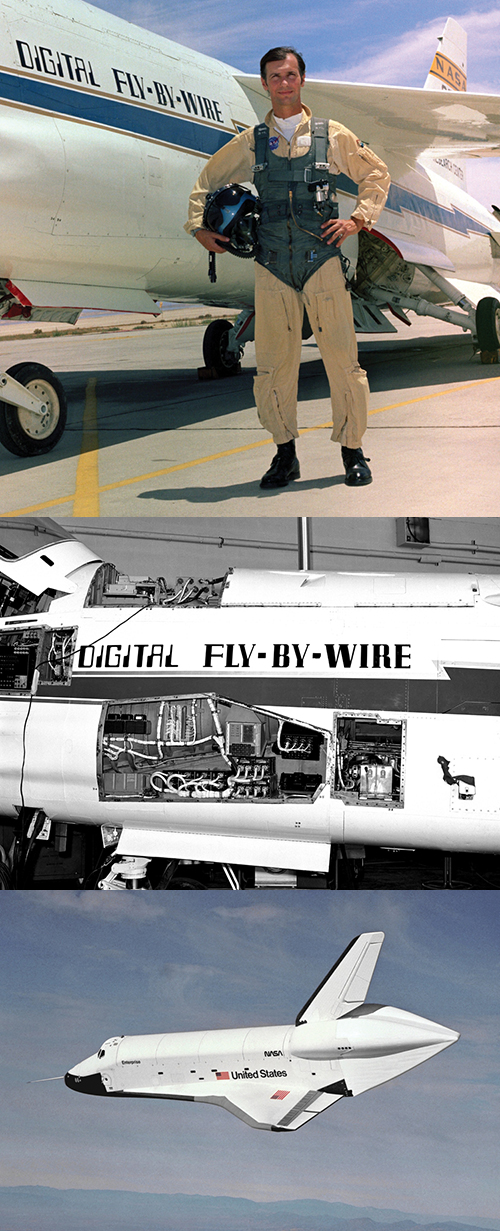
From top to bottom: Gary Krier, pilot of the first flight of an aircraft controlled by digital computer; cutouts in the F-8 aircraft show the incorporation of the Apollo computer, with the DSKY visible in the cutout beneath the word “Fly”; Enterprise, the Space Shuttle Program’s prototype, used to test the shuttle’s DFBW system.
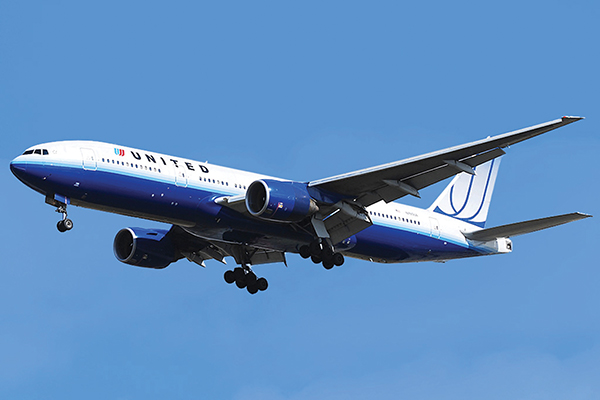
In 1994, the Boeing 777 became the second commercial airliner to fly using DFBW. For commercial aircraft, the replacement of heavy mechanical systems with DFBW controls provides greater fuel efficiency or the ability to carry more passengers or cargo. Image courtesy of Kevin Koske
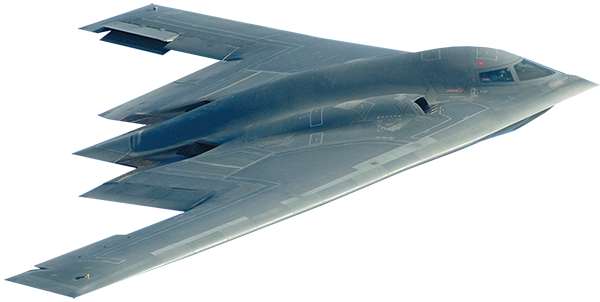
The Northrop Grumman B-2 Spirit is one of the aircraft designs enabled by DFBW technology.
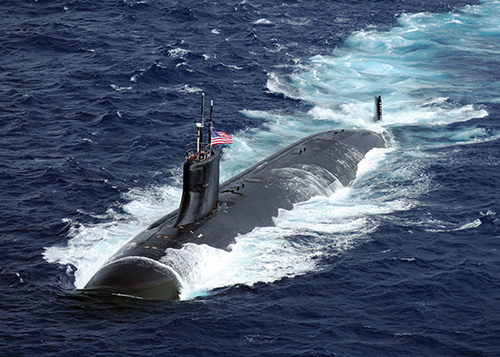
The U.S. Navy’s Seawolf class submarines feature a “swim-by-wire” system adapted by NASA partner Draper Laboratory from the Lab’s work during the DFBW program.
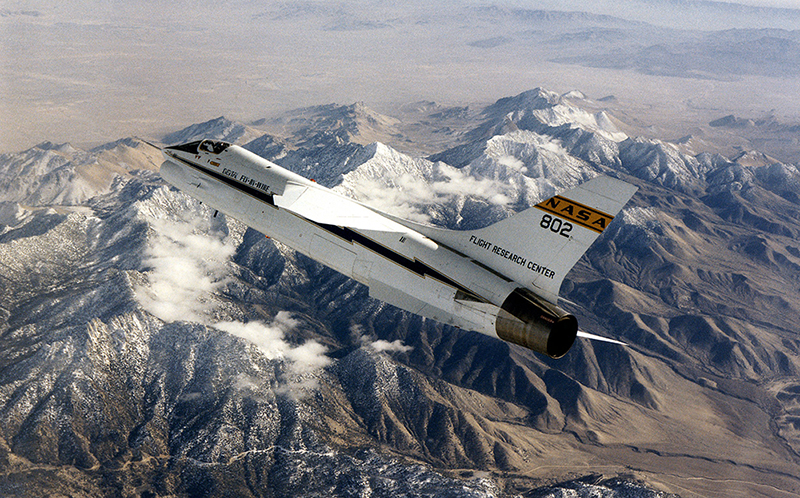
The F-8 Digital Fly-by-Wire (DFBW) research aircraft.