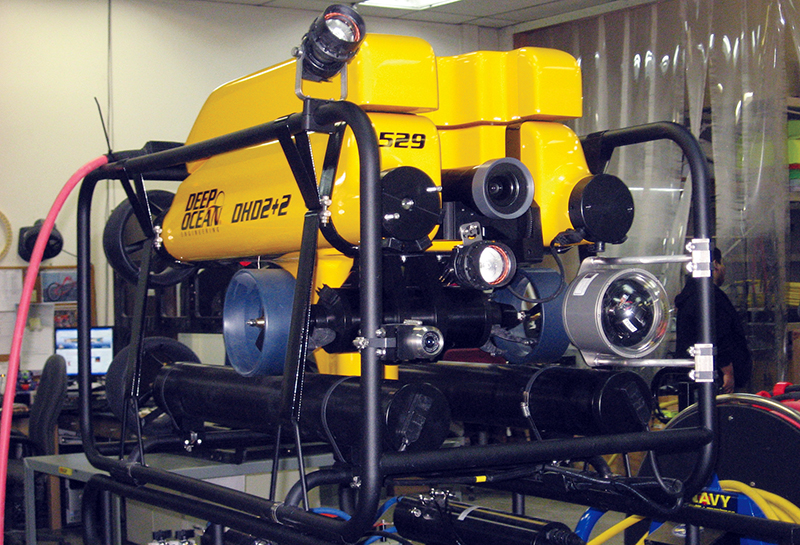
Robots Explore the Farthest Reaches of Earth and Space
Originating Technology/NASA Contribution
“We were the first that ever burst/Into that silent sea,” the title character recounts in Samuel Taylor Coleridge’s opus Rime of the Ancient Mariner. This famous couplet is equally applicable to undersea exploration today as surface voyages then, and has recently been applied to space travel in the title of a chronicle of the early years of human space flight (“Into That Silent Sea: Trailblazers of the Space Era, 1961-1965”), companion to the “In the Shadow of the Moon” book and movie. The parallel is certainly fitting, considering both fields explore unknown, harsh, and tantalizingly inhospitable environments.
For starters, exploring the Briny Deep and the Final Frontier requires special vehicles, and the most economical and safest means for each employ remotely operated vehicles (ROVs). ROVs have proven the tool of choice for exploring remote locations, allowing scientists to explore the deepest part of the sea and the furthest reaches of the solar system with the least weight penalty, the most flexibility and specialization of design, and without the need to provide for sustaining human life, or the risk of jeopardizing that life.
Most NASA probes, including the historic Voyager I and II spacecraft and especially the Mars rovers, Spirit and Opportunity, feature remote operation, but new missions and new planetary environments will demand new capabilities from the robotic explorers of the future. NASA has an acute interest in the development of specialized ROVs, as new lessons learned on Earth can be applied to new environments and increasingly complex missions in the future of space exploration.
Partnership
Deep Ocean Engineering (DOE) Inc., of San Leandro, California, designs and manufactures a complete range of underwater ROV systems. Founded in 1982, DOE has over 25 years of continuous operating experience in providing a wide range of innovative and cost-effective robotic solutions. Over 500 ROV systems have been designed, built, and delivered to hundreds of customers in over 30 countries.
During the 1990s, DOE received the first of several Small Business Innovation Research (SBIR) contracts from NASA to develop ROV technologies. Since many of those technologies are similar to what astronauts might use in space, the firm first worked on an ROV that could test enhanced human interfaces through an SBIR contract with Ames Research Center.
NASA recently followed this work with a Phase II SBIR contract, exploring the research and development of a versatile apparatus and method for remote robot mobility. Robotics intended for exploration of extremely remote and harsh environments must be extraordinarily versatile as well as robust. They must be able to perform in and adapt to unknown and highly variable physical surroundings—robots with tracks, wheels, or articulating legs can provide effective mobility on certain kinds of terrain. However, these same robots would likely fail if their mission requirements included roving over roughly contoured surfaces or in water, sand, slush, or ice.
DOE engineers developed a concept for a versatile and robust locomotion methodology based on snake and worm morphologies. This “super snake” has the ability to transition seamlessly from one environment to another, such as land to water, to burrowing into soft sediment.
Field experiments with this robot include sites such as San Francisco Bay, California’s Mono Lake, and desert environments such as Death Valley. The prototype equipment will be used by NASA on future projects, such as scientific research in the Dry Valley lakes of Antarctica, and experiments to evaluate concepts for exploration of Mars and Jupiter’s moon, Europa.
Product Outcome
The Monterey Bay Aquarium Research Institute (MBARI) has teamed with the National Oceanic and Atmospheric Administration on an Antarctic research project to study chemical and biological characteristics of icebergs. Because of the danger involved in getting too close to the icebergs, the team has been using a Deep Ocean DS2 ROV. The DS2 (two motor) ROV started life as a delivery to NASA in 1998, and has been on loan to MBARI. The ROV is in the process of being modified to become a DS4 (four motor), including additional thruster/motors and additional flotation.
Michael Gilson, vice president of Customer Solutions for DOE, explained the members of the Phantom family of ROVs: “The DS2 is a deeper-diving version of the S2 and the DS4 is a deeper version of the S4,” he said. “Unlike [with] a diver, depth is not a limiting factor, nor is water temperature or clarity of the water.”
The DS2 has an array of sensors that includes two suction samplers, a water sampler, plankton net, dissolved oxygen sensor, water speed sensor, two cameras (SIT and HD), three-function manipulator, and a tracking system. The Phantom family includes more than 70 deliveries in many countries for applications including military, archeology, science, oil and gas, and ship hull inspection.
Once the ROV is deployed in the water, the operator controls it and the attached instruments from the surface. From helping to recover drowning victims to inspecting off-shore oil platforms and gathering intelligence, DOE’s ROVs have many underwater uses. The U.S. armed forces use the ROVs in security measures and intelligence gathering, and Hydro Quebec—Canada’s largest electric utility and second largest corporation, which generates more than 95 percent of its production from hydroelectric facilities—uses a DOE ROV to inspect dams and hydroelectric apparatus for damage, saving an estimated $10 million in two seasons. More than 40 universities and scientific organizations conduct marine studies with the ROVs.
After more than 3 years of engineering design and development, including extensive discussions with customers worldwide, DOE launched the VectorROV product family. The state-of-the-art Vector family has three models to meet unique customer requirements. For example, the Vector L4 has been designed to meet the requirements of military, maritime, power generation, offshore petroleum, and scientific applications, and combines superior power, telemetry, and payload with ease of use, ruggedness, and reliability.
The power and control system for the Vector L4 is designed for simplicity and ease of use, with multiple microprocessors providing redundancy and expanded capabilities. The design incorporates intuitive, computer-aided, always active diagnostics facilitating maintenance of the system in the harshest environments by technicians with a minimum of training. Specifically designed high-performance brushless thrusters provide the highest power-to-weight ratio and reliability compared to other vehicles in its class. The Vector L4 graphical user interface with multiple menu screens provides intuitive feedback and active user control for ease of vehicle handling, navigation, collection and display of sensor data, as well as setting and storing custom system configurations.
Fabricated using modern marine-grade aluminum and composite materials, the chassis is modular with quick access to all the parts for ease of servicing and replacement as required. Constructed from polypropylene, the chassis is resilient, non-corroding, and maintenance free. Ancillary equipment is easy to mount and integrate.
Vector™ is a trademark of Deep Ocean Engineering Inc.
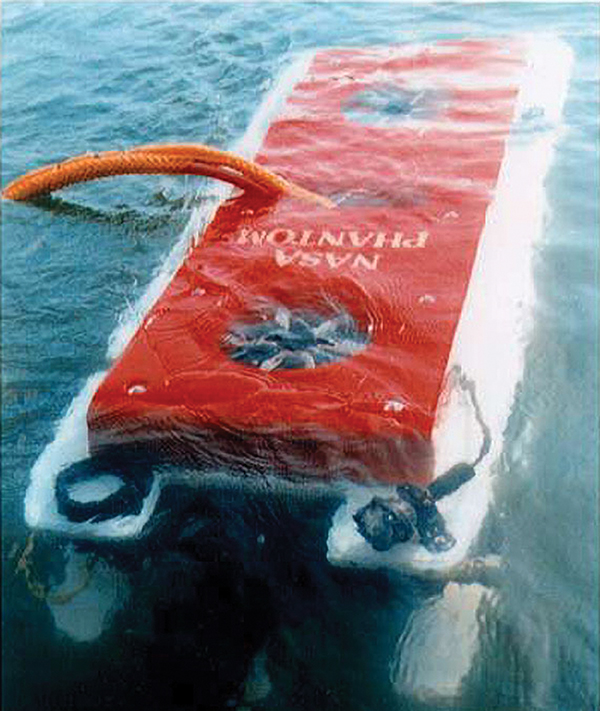
DOE’s ROV systems have been utilized in a broad range of industry applications, including military, security, salvage, long tunnel and pipeline inspection, customs, and nuclear and hydroelectric power plants.
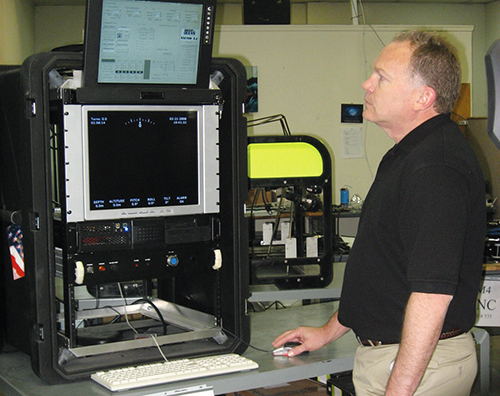
Configured submersible delivery systems also integrate a wide variety of sensors, tools, electronic navigational controls and tracking systems, instrumentation packages, and accessories.
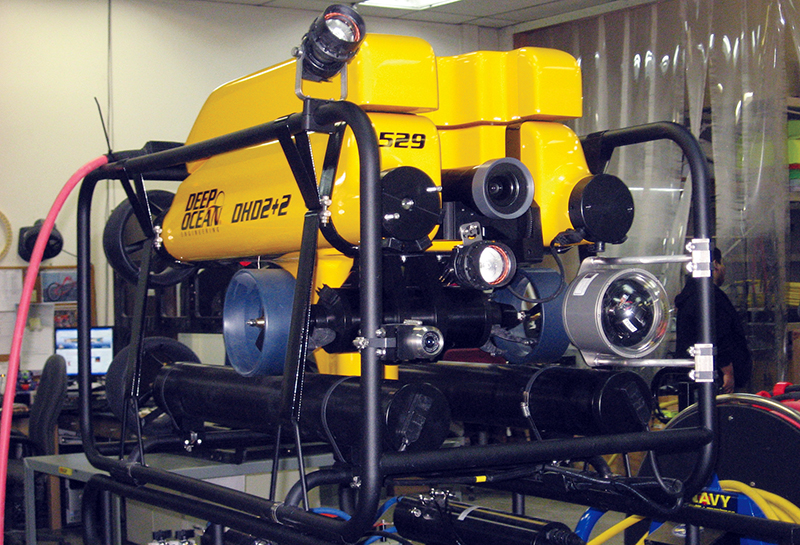
Deep Ocean Engineering Inc. provides robotic solutions for various underwater applications in harsh and diverse operating environments. DOE has been in continuous operation for 25 years and has sold more than 500 ROV systems in over 30 countries worldwide.