Measuring Pressure Has a New Standards
DH Instruments (DHI), Inc., of Phoenix, Arizona, is enjoying commercial success with its Force-Balanced Piston Gauge (FPG) after developing the innovation for NASA's Kennedy Space Center. Formally known as the FPG8601 Calibration System for Very Low Pressure, the FPG tests and calibrates instrumentation operating in the low pressure range.
Piston gauges derive pressure directly from the base units of mass, length, and time. Because of their fundamental operating principles and long term stability, they are an essential tool in pressure metrology, which assures the integrity of pressure measurement throughout science and industry. According to Martin Girard, DHI's chief executive officer, the concept for the FPG grew from the need for a primary pressure standard for both gauge and absolute pressures to cover the range below what is covered by conventional piston gauges or deadweight testers. Original product concepts were based on the combination of a high-precision piston-cylinder and a digital mass comparator.
DHI, a supplier to the Kennedy Metrology Laboratory since the mid-1980s, worked with the Japanese National Research Laboratory for Metrology (NRLM) in the 1990s to produce conceptual drawings of the FPG. In 1994, Kennedy expressed the need for an easy-to-use, low-pressure, primary standard to support the calibration of instrumentation for the International Space Station. DHI provided an unsolicited proposal based upon its work, resulting in a NASA contract to provide Kennedy with the FPG.
The Kennedy system was inspected and accepted for installation in August 2000. The FPG saves the Center time and money, since NASA can avoid sending certain components to the National Institute of Standards and Technology for calibration. The system provides a traceable, primary calibration standard for measuring pressures in the range of near 0 to 15 kPa (2.2 psi) in both gauge and absolute measurement modes. The hardware combines a large area piston-cylinder with a load cell measuring the force resulting from pressures across the piston. The mass of the piston is tared out, allowing measurement to start from zero. A pressure higher than the measured pressure, which keeps the piston centered, lubricates an innovative conical gap located between the piston and the cylinder, eliminating the need for piston rotation. A pressure controller based on the control of low gas flow automates the pressure control.
After achieving success with Kennedy, DHI is now marketing the FPG as an automated primary standard for very low-gauge and absolute pressures. Several metrology laboratories have already installed the system, including the NRLM in Tsukuba, Japan, and the National Measurement Institute in Helsinki, Finland. DHI is currently selling the FPG to high-end metrology laboratories on a case-by-case basis and expects a full commercial release to the general public in the summer of 2002. Due to the critical nature of accurate measurements of very low-gauge and absolute pressures, Girard believes that the FPG has applications in many industries, including aerospace, semiconductor manufacturing, nuclear fuel processing, and pharmaceuticals.
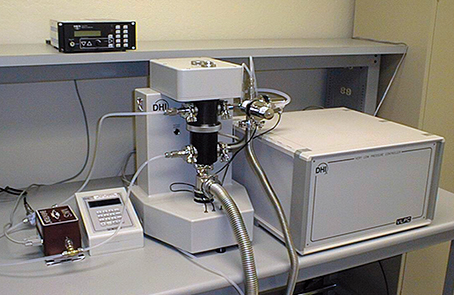
The Force-Balanced Piston Gauge tests and calibrates instruments that operate in the low pressure range.