A Cool Tool for Deicing Planes
When airplanes reach cruising altitude, the high speeds and low temperatures of the air cause thin layers of ice to begin forming on the wings. Ice can present an increased safety risk to the aircraft and its passengers. Thanks to an innovation from NASA's Ames Research Center, this danger could one day be eliminated. Ames patented the Electro Expulsive Separation System (EESS), which is now licensed to Ice Management Systems, Inc. (IMS), of Temecula, California.
EESS is an aircraft ice removal system, appropriately nicknamed the "ice zapper." According to the principle inventor, Leonard Haslim, "It pulverizes ice and removes layers of ice as thin as frost or as thick as an inch of glaze." The EESS consists of layers of conductors encased in materials that are bonded directly to the airframe structure. When ice accumulates on the aircraft, an electric current is sent through the conductors, causing them to pulse. Even though the conductors move less than a twenty-thousandth of an inch in just a millisecond, the movement is sufficient to pulverize the ice. It is this highly accelerated motion that shatters the ice into particles the size of table salt; too small to be harmful to the aircraft.
In 1995, Richard Olson, CEO of IMS, first introduced the ice zapper into the private sector. He has since made improvements that have paid off with recent sales to TRW (Thompson Ramo Woolridge), who purchased the technology for use on a new line of planes. IMS envisions a variety of uses for the EESS technology in the aerospace and automotive industries.
The EESS also offers additional benefits besides the unique ability to deice planes while in flight. According to Haslim, "The ice zapper uses one-thousandth of the power and is one-tenth of the weight of electro-thermal ice removal systems used today." Using less power means that operating costs are lower, while the lighter weight translates into needing less energy to propel the aircraft, resulting in even further cost reductions.
When compared with other systems in use, such as thermal deicers and pneumatic boots, the ice zapper does very well. Thermal deicers are fairly common, although they use an enormous amount of energy and present the possibility of ice refreezing. Pneumatic boots are not always effective because they require an inflation device that is unable to work until a quarter inch of ice has accumulated. With both systems, the ice that is loosened may still be large enough to cause problems for the plane once dislodged. For instance, in just one winter, 26 F/A-18 airplanes were seriously damaged when sizable chunks of ice entered the engines after having been removed by pneumatic boots. Because the EESS will reduce ice to such tiny particles, the chances for this type of occurrence on a plane using the technology would be very unlikely.
Even though EESS has a clear market in the aerospace industry, another potential use for the EESS is in the automotive sector. Specifically, a modified version of the ice zapper could be fitted to the windshields in cars, making the need for ice scrapers and other cumbersome methods obsolete. The automotive applications may be further explored in the future, but for now IMS is aggressively working to demonstrate value to aircraft manufacturers.
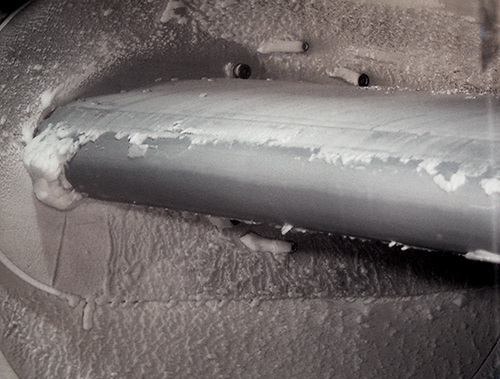
The NASA-developed Electro Expulsive Separation System (EESS) is shown in a testing chamber where it proved it could rid aircraft of ice layers ranging from thin frosts to thick glazes.