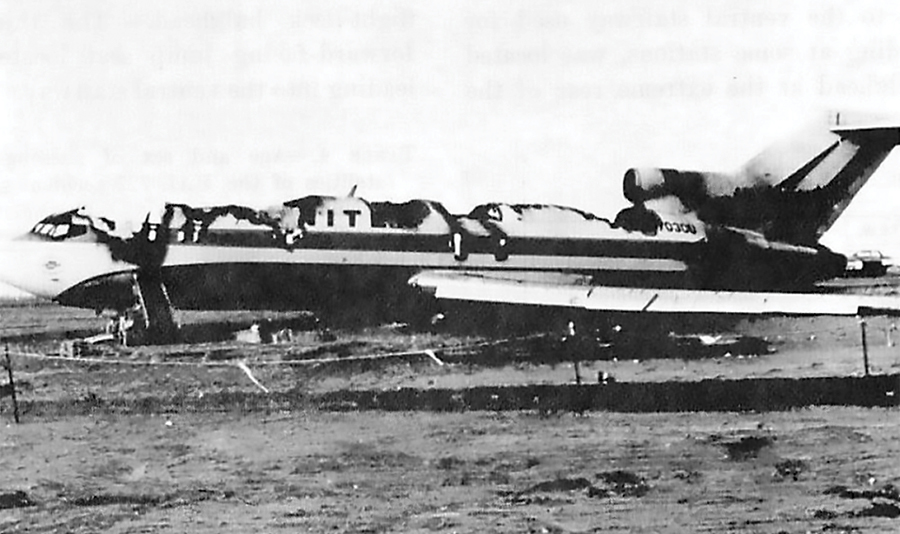
Polyimide Foam Offers Safer, Lighter Insulation
NASA Technology
Oxygen, which comprises just over a fifth of Earth’s atmosphere, is highly reactive and able to form compounds with nearly all other elements. Heat facilitates these reactions. Once a material is sufficiently heated to combine with oxygen, that reaction releases more heat, often setting off a chain reaction that can become difficult to stop or even contain—a conflagration.
To avoid fires, the trick is often to start with materials that resist oxidation, even at high temperatures. But in the 1970s, the airline industry found there was no adequately fire-resistant material fit for use in airplane cabins. NASA came up with a solution that never quite made it into the cabin but can still be found in other parts of most planes flying today and now has many other applications.
Congressional testimony in 1979 suggested that between 1969 and 1978, 419 deaths resulted from post-crash fires. The fatalities almost certainly could have been avoided, given more time to evacuate. And it was often not the fire but the smoke and toxic gases it released that killed passengers.
By then, industry had found ways to incorporate fire-retardant additives into materials such as the foams used in airplane seating, but it was then discovered that, once these additives were hot enough to ignite, they produced large quantities of smoke and incapacitating toxic gases.
NASA had come up with some fire-resistant materials for the Apollo Program and Skylab by the late 1960s and recommended them for public use, but industry deemed them too fragile and much too expensive to manufacture.
So in the mid-1970s, the Federal Aviation Administration and NASA, along with industry players, launched a cooperative effort to improve fire safety in aviation. At NASA, the effort was known as the Fire Resistant Materials Engineering (FIREMEN) project, and it involved a number of the Agency’s field centers between 1976 and 1981.
Materials research under the program culminated with a contract between Johnson Space Center and a company called Solar Turbines International, a division of International Harvester, building on previous work by Solar Turbines, Boeing, and others, mainly at Johnson and Ames Research Center. The goals were ambitious: take a type of polyimide foam identified in earlier work and optimize it for seat cushioning, low-density wall panels, high-strength floor panels, and thermal/acoustic insulation; figure out the best way to manufacture all four products; and make it economically viable—something industry would actually use.
Solar Turbines had been working on foam insulations for solar energy systems since the late 1960s, and its recent work with Johnson had determined this particular type of polyimide foam not only withstood high temperatures but also produced virtually no smoke or flames when it finally began to char. NASA’s ultimate goal was to extend escape time from a burning fuselage from about two and a half minutes to five minutes.
Lasting more than two years and meticulously documented, work under the final contract was exhaustive. Researchers tried various ingredients, ratios, fillers, and additives in the recipe for the starting powder, as well as different processes for turning the powders into foams and for mass-producing the foams into the four end products. Throughout, different timing, temperatures, and countless other variables were tested.
The end products were assessed for resistance to extensive wear and tear, dry heat, humidity, and flames, as well as thermal and acoustical insulation properties.
Technology Transfer
The results were not quite final products, but the material formulations and processing and fabrication techniques were refined enough for industry to take over. Researchers had identified, for example, the molecular ratios in the basic resins that yielded the best mechanical properties, that spray drying worked best for producing the precursor powders, and how to adjust that process to achieve different properties. They learned that conductive fillers coupled with a powerful microwave oven allowed for foaming and curing in a single step, and pulsing the microwave on and off produced a more homogeneous foam. They found that adding ceramic fibers to the powder precursors significantly improved fire-resistance. All these formulas and processes were optimized for each end product.
NASA waived its patents on the materials to allow Harvester International to produce it commercially, and in January of 1982, the company announced full-scale production of fire-resistant SOLIMIDE foams at a 25,000-square-foot facility in Illinois. Within two years, a company called Imi-Tech had acquired the operation, and several aircraft manufacturers were using SOLIMIDE products, mainly as a lightweight, fireproof thermal and acoustic insulator in fuselages (Spinoff 1984). The Navy was funding development of a slightly different version of the foam for use in ships.
In 1988, Imi-Tech moved to Magnolia, Arkansas, doubling the size of its SOLIMIDE production facility—the plant where SOLIMIDE is still produced today.
A decade later, the material had replaced fiberglass insulation in the fuselages of many commercial airliners and was also used in spacecraft, satellites, industrial cryogenic applications, and the Navy’s ships and submarines (Spinoff 1998).
Benefits
SOLIMIDE hasn’t made it into airline seats or cabin panels, but it can now be found somewhere in 90 percent of commercial airliners in the western world. Almost every ship in the U.S. Navy uses it for thermal and acoustic insulation.
In 2014, Boyd Corporation, a global company that specializes in sealing, thermal, and protection solutions, purchased the SOLIMIDE plant in Magnolia. Boyd had been a major consumer of the material for the commercial aerospace industry for years, says Richard Montgomery, field application engineer at Boyd, noting that the plant is the only one in the world that produces large quantities of polyimide foam. “It’s a unique foam, in that it’s lightweight, nonflammable, and a great insulator,” he says.
All these qualities, in addition to its durability, acoustic insulation, and ease of handling, have made it a popular alternative to fiberglass for insulating commercial, private, and military airplane fuselages, where it saves hundreds of pounds on each plane, translating to fuel efficiency and safety improvements. Airframe manufacturers also commonly use SOLIMIDE to insulate ducts and electronics in planes. The Navy has specified the material as a thermal and acoustic insulation in applications where weight is a critical factor.
“The material aligns with industrial and design initiatives of today, and sales have continued to increase as new applications are found,” says Mitch Weirenga, marketing manager at Boyd.
It is non-toxic and environmentally friendly, with some versions receiving a Greenguard Certification from Underwriters Laboratories—signifying low chemical emission—and it supports industry initiatives for minimizing the manufacturing carbon footprint and the treatment of goods at their end of life, Wierenga says. It also does not support microbial growth, making it ideal for medical applications in environments where condensation is a risk.
SOLIMIDE now comes in seven varieties, depending on the temperatures and other environmental needs of end users.
For spacecraft manufacturers, including NASA, two more of SOLIMIDE’s qualities become important: It doesn’t release any chemicals, which, in the absence of convection, can build up in and around spacecraft. And it has an enormous temperature range, staying flexible and resilient at temperatures from -300 °F to 575 °F, and barely expanding or contracting with temperature swings. “Most things, if you dip them in liquid nitrogen and drop them on the floor, they’ll explode,” says Montgomery. “Not SOLIMIDE.”
Other applications include missile guidance systems, railcars, medical devices, solar energy systems, indoor climate control, electronics, and cryogenic pipelines and storage.
The fact that SOLIMIDE has no fibers or toxins has also made it attractive, for example as Europe makes an effort to get fiber insulation out of appliances and heating and ventilation systems, says James Williams, manager of the plant in Magnolia. The tiny fibers can be inhaled or get under the skin. That’s what led a manufacturer of heating appliances for hospitals to become a customer. And those who work directly with it appreciate SOLIMIDE’s ease of handling. “Installers who work with the material absolutely love it for a number of reasons, the biggest being that they don’t have to suit up with safety gear,” says Williams. “That helps from a marketing standpoint.”
Williams estimates that SOLIMIDE supports about 100 jobs at Boyd—40 at the plant he manages and 60 more who work with it at Boyd’s Portland plant.
In 2016, Boyd commercialized a “densified” version of the material, which provides the same insulating qualities at about half the volume, making it work for small spaces. One application for this denser, harder material is in the cryogenic nitrogen generation systems in all large aircraft. As fuel is used up, these systems replace that fuel in the tanks with nonflammable nitrogen gas, preventing fire.
“We’ve found some niche markets for densified SOLIMIDE, and we’re finding new ones every month,” says Montgomery.
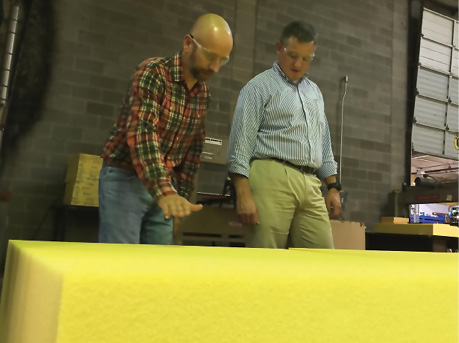
James Williams, left, manager of Boyd Corporation’s SOLIMIDE plant in Magnolia, Arkansas, shows Solimide panels to local Congressman Bruce Westerman during Westerman’s 2016 visit to the plant.

The use of different laminates can alter the thermal and acoustic insulation properties of SOLIMIDE foams.
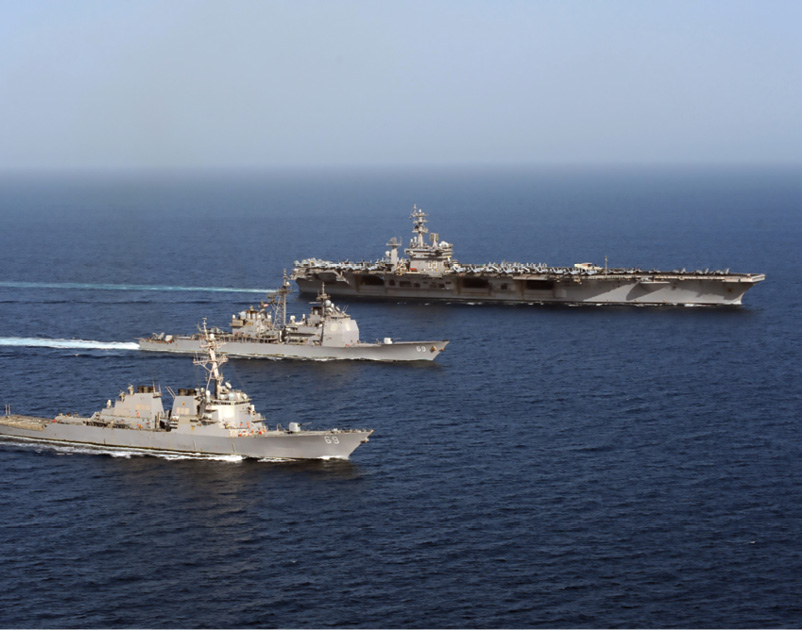
The U.S. Navy was an early adopter of Solimide and helped fund some of its early development. Image courtesy of the U.S. Navy
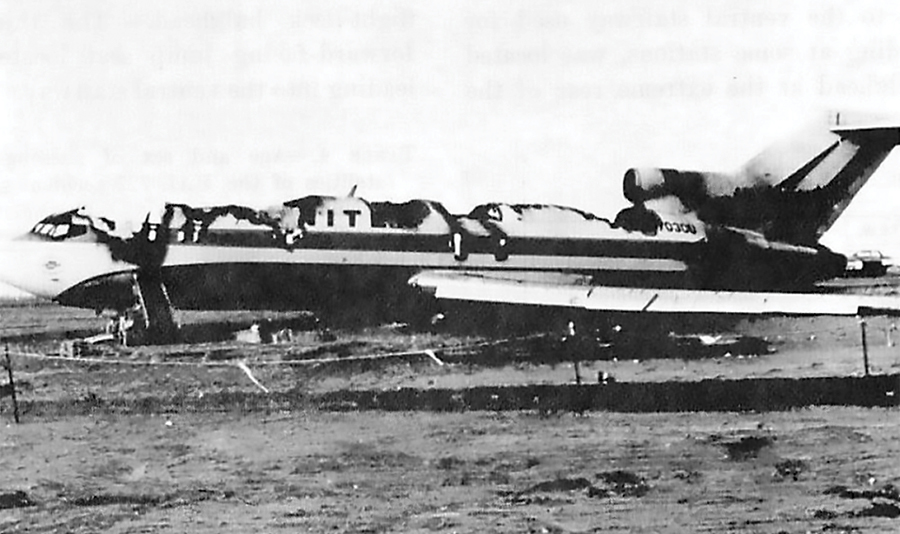
In 1965, United Airlines Flight 227 crashed during landing at Salt Lake City International Airport. According to reports, landing gear broke free and ruptured a fuel line in the fuselage. At the same time, sparks from the fuselage’s friction with the runway and/or severed generator leads immediately ignited the fuel, and the plane burst into flames. Forty-three of the 91 occupants were killed, many, if not most, due to the fire and smoke inhalation. Incidents like this prompted the Federal Aviation Administration and NASA to launch the joint Fire Resistant Materials Engineering Project in 1976, seeking to develop materials for airplane interiors that were fireproof and didn’t give off smoke. Image courtesy of the Federal Aviation Administration