Rhenium Redefined
Through a Small Business Innovation Research (SBIR) contract with NASA's Glenn Research Center, another business is delivering an innovative new product. Rhenium Alloys, Inc., of Elyria, Ohio, developed a new method for producing rhenium combustion chambers. While the method provides major benefits to NASA, the benefits and conveniences also extend to the private sector.
Rhenium is one of Earth's rarest naturally occurring metals and is required by NASA for various space applications. It has an extremely high melting point of 5756 °F, and can maintain its durability through thousands of repeated temperature changes. This makes it attractive because a rocket made of rhenium could be cooled by simply radiating its heat into space, instead of being cooled by alternative means, which are presently a major source of fuel inefficiency in spacecraft. Unfortunately, this metal had a reputation for being difficult to work and form.
Glenn researchers found several less costly methods for forming the metal, but decided the manufacturing industry would be the ideal source for perfecting and refining these developments--enter Rhenium Alloys, Inc. Using room temperature isostatic pressing, the company compacted rhenium powder to a high density and into the approximated end shape and dimension of the rocket thruster. The item was then subjected to sintering and containerless hot isostatic pressing, increasing the density of the powder metallurgy part. With the new manufacturing process, both production time and costs are reduced while quality is significantly increased. The method enabled the company to deliver two chemical rocket thrusters to Glenn Research Center. Not only was the new method good for creating rocket thrusters, but also for other commercial purposes. For instance, Rhenium Alloys, Inc., used its innovative process to manufacture a rhenium hemisphere for a commercial customer, and can also create other custom parts as needed.
Rhenium Alloys, Inc., makes rhenium a practical choice in manufacturing fields, including the aerospace, nuclear, and electronic industries, with upcoming opportunities projected in medical instrumentation.
Todd Leonhardt, director of technology at Rhenium Alloys, Inc., attributes part of the company's success to NASA and the SBIR program: We would never have been able to develop these processes without the financial and technical support of the SBIR contracts. The advice and encouragement we received from Glenn researchers was [sic]also invaluable.
With their innovative new processing capabilities, Rhenium Alloys, Inc., will continue to remain a premier global supplier of rhenium and rhenium alloy products.
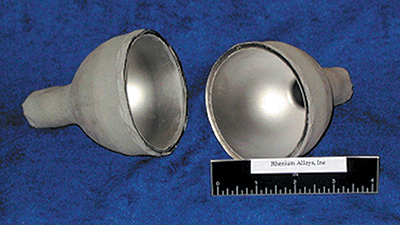
Rhenium Alloys, Inc., uses NASA-developed methods to manufacture custom parts from rhenium, such as the two domes displayed here.
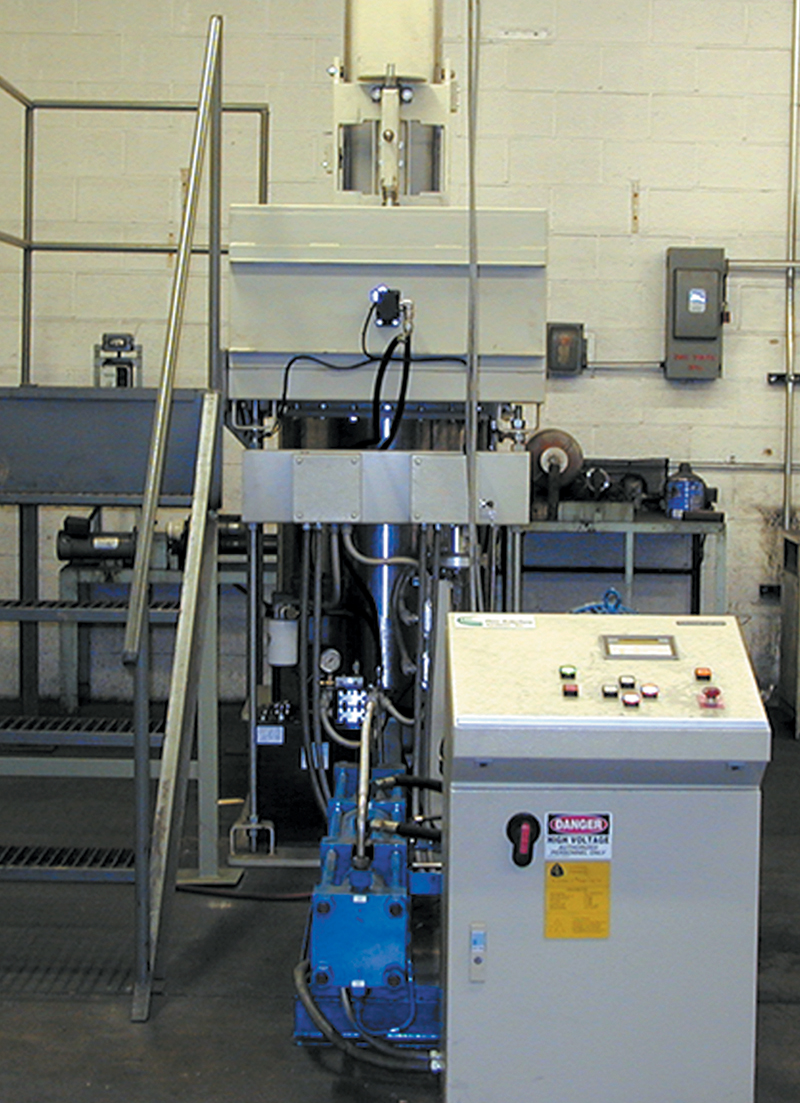
Rhenium Alloys, Inc., uses their cold isostatic press to compact rhenium powder to a high density. The pressed compact is the approximate shape of the component.