Paint and Shoot
Up Polariscope! That's the call if you need to monitor such items as fatigue in composite materials or visualize residual strains in glass and plastic.
A few years ago, through a Small Business Innovation Research (SBIR) award from NASA's Langley Research Center, Stress Photonics, Inc., of Madison, Wisconsin, developed the Delta Therm 1000. This infrared-based stress measurement system was commercialized, permitting its user to compare designs and detect cracks in structures, especially aging aircraft and bridges. Combining digital signal processing technology with a special infrared camera, the system provided instantaneous thermal images and live differential images.
Stress Photonics has furthered its research on structural integrity analysis. Under a Langley Small Business Technology Transfer (STTR) contract, the firm has perfected the portable Grey-field Polariscope. This device, called the GFP 1000, involves a single rotating optical element and a digital camera for acquiring full-field images quickly and efficiently.
The company has also introduced specially tinted brush-on coatings. While paint-on coatings have been possible for many years, they were rarely used because the thickness of the coating directly affected the stress measurement.
For the GFP 1000 to efficiently measure the coating thickness, a coating tint attenuates red, green, and blue light to different degrees. Once a target object is illuminated with the GFP 1000's circularly polarized light, oscillations of that light can be reviewed for strain amplitude and direction. When measured by the Polariscope, for instance, a paint-on coating applied to a wrench would reveal the tool undergoing shear strains as a bolt was being tightened.
Moreover, by using the GFP 1000, the thickness of a brush-on coating can be ascertained. Therefore, the Polariscope that measures strain amplitude can also appraise the thickness of the coating, eliminating it as a variable. The result is a full-field strain map by using a truly simple "paint and shoot" technique. Data are displayed on a laptop computer for analysis. Data collected are presented in an intuitive format so that they are easy to interpret. One image depicts the shear strain magnitude with gradients represented in grayscale levels, and the other indicates the directions of the principal strains. Commercially available, the GFP 1000 also works with all currently available photostress coatings, such as paste-on sheet or liquid contoured.
Reflective photoelastic strain analysis has a longstanding history. Although proven to be very effective over decades, the technique has been largely overlooked by scientists as a fruitful area for innovation due to its maturity. Supported by NASA STTR funds and enabled by Stress Photonics researchers, this tried and true technique now finds greater usefulness by incorporating modern video and computer technologies.
More than $2 million in research and product development projects have been completed by Stress Photonics. The company is one of Wisconsin's top SBIR recipients, receiving research and development funds from several U.S. government agencies, as well as major industries. It actively markets a growing line of stress and strain analysis and flaw detection products worldwide. In 1994, the organization was selected by more than 75 leading scientists to receive the prestigious R&D 100 Award.
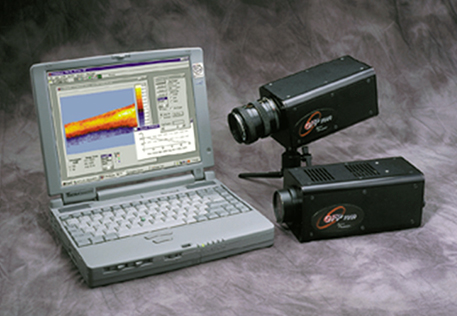
Stress Photonics, Inc.’s GFP 1000 acquires full-field images quickly and efficiently, detecting cracks in structures.
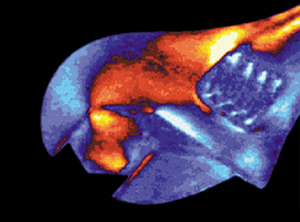