Prototyping the Future
Advanced Ceramics Research (ACR) of Tucson, Arizona, has been labeled "The Idea Factory"— and for good reason.
This young up-start company, just a handful of years old, is already the 11th fastest growing high-tech firm in Arizona. ACR has taken on the mantle of research in advanced materials and process development, transforming scientific concepts into technological achievement. Doubling in size, its equipment-packed, state-of-the-art facilities demand that ACR ready itself for yet another expansion.
Through a Small Business Innovation Research (SBIR) award from Marshall Space Flight Center (MSFC), ACR developed a high pressure and temperature fused deposition system. This ACR-designed rapid prototyping system is known as extrusion freeform fabrication. Using solid feedstock, this system can extrude and form shaped components, using solid powders and/or chopped fibers as fillers to the thermoplastic feedstock. One near-term application for the equipment is in the biomedical prosthesis business.
Three-dimensional rapid prototyping is a process in which physical models are quickly and inexpensively created directly from computer-generated models. Rapid prototyping decreases the product development cycle necessary to compete in the market places of today. Concepts can be transformed into inexpensive prototype parts within days instead of weeks; designs can be verified and engineering costs decreased--no surprises at production time, despite difficult-to-do designs.
Durable, high-strength thermoplastic used for rapid prototyping gives models increased functionality. It provides impact resistance, toughness, heat stability, chemical resistance, and rigidity to permit functional tests on sample parts. Its properties also allow for post-processing techniques such as machining, drilling, tapping, painting, glueing, and sanding.
In another area, Marshall Space Flight Center also contracted ACR to fabricate a set of ceramic engines, to be appraised for a solar thermal rocket engine test program. Along with the MSFC work, ACR received SBIR funding through Ames Research Center. That work centers on continuous fiber reinforced composites for heat shield applications. The technical success of this project, and spinoff work in ceramic plate manufacturing, have attracted several commercial clients and other federal customers, ACR reports.
ACR has developed and implemented three key strategies for maximizing the commercialization of its SBIR programs. These are: Case 1 - the exploitation of the directly-developed technologies from the SBIR program; Case 2 - taking advantage of the credibility associated with both the award and work performed for a Federal SBIR program; and Case 3 - utilizing spinoff technologies from the SBIR work as the program is developing such technologies.
This last point is well taken. Research and development funding from NASA and other SBIR sources equaled, at one point, a total of $750,000. Those dollars have helped refine ACR's true bread-and-butter product, commercial carriers. Sales now total over $10 million. ACR manufactures world-class quality carriers for the grinding, lapping, polishing, and wafer polishing industries. The firm's commercial carrier production represents nearly fifty percent of the worldwide consumption. In other terms, one out of every two new personal computers uses hard drive disks made by ACR carriers. SBIR contracts from Marshall Space Flight Center were instrumental in initiating ACR's commercial business. Since its start, ACR has evolved from its customer base of one hundred percent Federal work to twenty-five percent Federal and seventy-five percent commercial.
Would you expect any less from an idea factory?
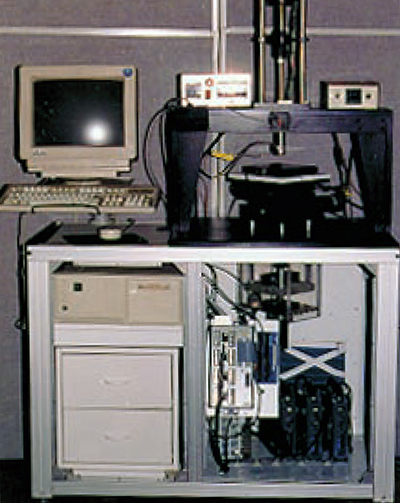
High pressure retrofit modeler transforms computer-based digital images into prototype hardware to ensure customers of a quality final product.
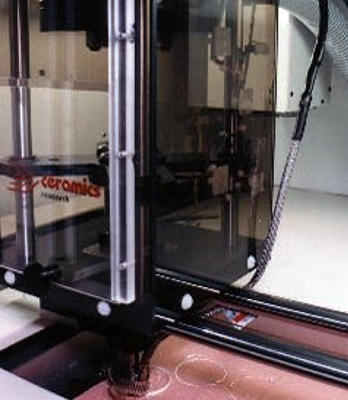
ACR equipment can shorten a customer's product development cycle and save on engineering and production costs—from composite brake pads for bikes to satellites.