Tough Like Metal
A new coating material can greatly extend the lifetime of ceramic composites, making them more than 1,000 times more durable.
Lewis Research Center has awarded Small Business Innovation Research (SBIR) contracts to Advanced Ceramics Corporation (ACC) of Cleveland, Ohio, as part of a NASA campaign to study propulsion materials within its high-speed aircraft program.
ACC has developed a family of high temperature and specially treated boron nitride coatings. These interface coatings circumvent moisture that complicates composite manufacture and ultimately degrades composite performance at high temperatures. The moisture-resistant coatings extend the shelf life of composite materials and resist thermal oxidation in moist air. Ceramic fibers woven into fabrics can now be coated with this advancement. The coating work is seen as a boon to the ceramic composites industry.
What are ceramic composites? They are a new type of material made by reinforcing refractories with high-strength ceramic fibers. They are as strong as metal, yet can withstand higher temperatures. One immediate use for composite materials is use in turbine engines, an application that can make the engines far more efficient.
Industrial gas-fired power turbines that have composite combustor liners and shrouds can compress fuel and air at higher temperatures than all-metal turbines, which increases efficiency. The turbine can produce more kilowatt-hours from the same fuel than it could if metal combustor liners and shrouds were used. This is a big advantage in the competitive and very cost-conscious power turbine industry.
Aircraft turbine engines which have composite liners and shrouds also weigh less than all-metal turbines. This allows the aircraft to carry a larger payload or fly a longer distance using the same fuel. "More payload and more distance from the same engine and the same fuel" is the mantra of civil aviation.
Why did ceramic composites require better interface coatings in the first place? A sliding interface between fiber and ceramic allows mechanical loads to be distributed to the reinforcing fibers, making ceramics "tough" like metals. A lot of energy is needed to produce a fracture in a ceramic composite. But conventional interface coatings are removed by air, especially by moisture in the air.
Through NASA SBIR-supported research at Advanced Ceramics Corporation, a high-performance barrier coating was made, capable of being applied to composites by chemical vapor deposition. This new coating enables continuous ceramic fiber composites to be used at higher temperatures, permitting development of ceramic combustors and hot parts for advanced turbine engines. Non-aerospace applications of the barrier coating include stationary power turbine components, radiant tube burners, gas-flow heat exchangers and filters, and waste incineration systems. ACC received a patent for its work on interface coatings for ceramic fibers in January 1997.
Advanced ceramic materials are experiencing rapid growth because they perform extreme engineering and structural functions that are outside the performance range of metals and metallics. Advanced ceramics operate effectively from super-cold to super-hot temperatures. Paradoxically, these materials are excellent electrical insulators and also perform as superconductors.
ACC's investigations into special coatings for ceramic composites are expected to provide an entire new range of high-performance material options. These materials are making important contributions in such leading technologies as heat engines, integrated circuit manufacture, and superconductivity. They also are important in manufacturing and processing applications such as molten metal handling and glass making.
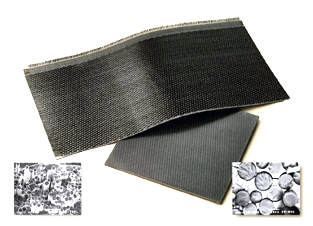
Advanced Ceramics Corporation research makes composite materials more durable by application of patented coatings. Work was stimulated by NASA interest in future high-speed civil air transportation.