Nondestructive Test Probe
Under NASA's Aircraft Structural Integrity program, which addresses ways to enhance the safety of aging commercial jetliners by improving structural inspection and lifetime prediction techniques, Langley Research Center is developing a variety of devices and procedures for detecting cracks, disbonds and corrosion during routine aircraft service inspections. One such device is the CrackFinder, now commercially available; it is manufactured by Krautkramer Branson (KB Instruments), Lewistown, Pennsylvania under an exclusive NASA license.
The CrackFinder is an electromagnetic probe for nondestructive evaluation (NDE), developed to meet a need for a highly reliable, low cost method of rapidly scanning aircraft skins for surface breaks. It is based on eddy current technology that enables extreme sensitivity to fatigue cracks in aluminum alloy plates. An eddy current is an electrical current induced by an alternating magnetic field; eddy current techniques are generally used for detecting surface cracks, where ultrasonic systems are used for detecting internal flaws.
The device employs an innovative self-nulling feature that makes the CrackFinder simple yet highly accurate, reliable and economical. Self-nulling means that the device automatically recalibrates to zero so that each flaw detected produces a reading. When the probe is placed on a flaw-free metallic object, its output is automatically nulled. The presence of a flaw alters the delicate self-nulling condition, causing a distinctive probe output amplitude. A bargraph display indicates crack severity.
A subsidiary of Emerson Electric Company, Krautkramer Branson says the innovative probe removes some major limitations of conventional eddy current testing: the CrackFinder is more affordable, costing about one-third the price of a conventional eddy current instrument package; it is small and lightweight, weighing only nine ounces where conventional eddy current instruments weigh six to 20 pounds; its small size and simplicity allow installation of multiple probes in inaccessible locations for periodic monitoring of crack growth in critical infrastructures; and it requires minimal operator training. It also needs no calibration or balance circuitry.
The versatile CrackFinder has applications beyond the aging aircraft market, for example, steel structures, ski lifts and other structures where detection of fatigue is critical. NASA's Technology Application Team at Research Triangle Institute played a part in bringing the CrackFinder to market by identifying Krautkramer Branson as a prospective NASA commercialization partner.
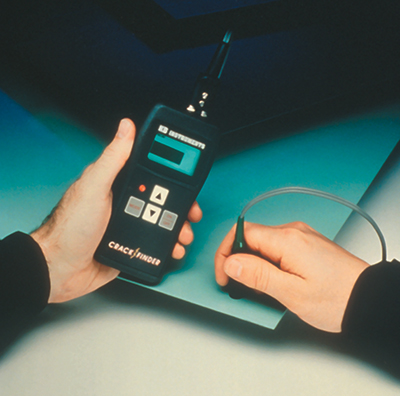
Developed to scan aircraft skins for surface breaks, the CrackFinder is available for industrial use in fatigue detection.