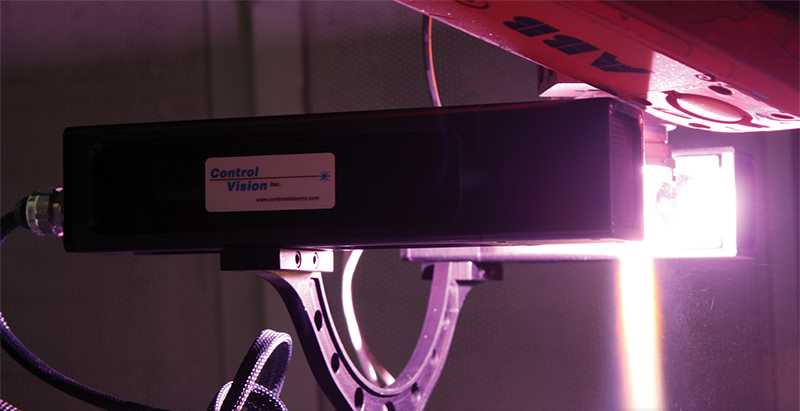
Vision Systems Illuminate Industrial Processes
NASA Technology
When NASA designs a spacecraft to undertake a new mission, innovation does not stop after the design phase. In many cases, these spacecraft are firsts of their kind, requiring not only remarkable imagination and expertise in their conception but new technologies and methods for their manufacture.
In the realm of manufacturing, NASA has from necessity worked on the cutting-edge, seeking new techniques and materials for creating unprecedented structures, as well as capabilities for reducing the cost and increasing the efficiency of existing manufacturing technologies. From friction stir welding enhancements (Spinoff 2009) to thermoset composites (Spinoff 2011), NASA’s innovations in manufacturing have often transferred to the public in ways that enable the expansion of the Nation’s industrial productivity.
NASA has long pursued ways of improving upon and ensuring quality results from manufacturing processes ranging from arc welding to thermal coating applications. But many of these processes generate blinding light (hence the need for special eyewear during welding) that obscures the process while it is happening, making it difficult to monitor and evaluate.
In the 1980s, NASA partnered with a company to develop technology to address this issue. Today, that collaboration has spawned multiple commercial products that not only support effective manufacturing for private industry but also may support NASA in the use of an exciting, rapidly growing field of manufacturing ideal for long-duration space missions.
Technology Transfer
The company was Control Vision Inc., then based in Idaho Falls, Idaho. Through the Small Business Innovation Research (SBIR) program, Control Vision partnered with Marshall Space Flight Center to create video sensor systems capable of imaging industrial processes in which high temperatures and brightness impede in-process visualization. These systems used specialized illumination to overcome process light, explains Dan Crawford, president of Control Vision.
“The basic technology uses intense, pulsed illumination to overwhelm whatever specific process light there is,” he says. The system’s sensors, tuned to a wavelength within the brighter light source, filter out the light generated by the welding arc or furnace, producing clear images of the process as it is happening. At Marshall, Control Vision’s systems were installed and tested on low pressure plasma spray processes to image the particles inside the plasma spray plume.
After a change of ownership, Control Vision is now based in Sahuarita, Arizona, and offers three products that have their origins in the company’s NASA work.
Benefits
One of the products, the LaserStrobe system, uses 10-nanosecond laser pulses and high speed shuttering to create high quality images of conventional and laser welding, plasma spray, and processes such as fiberglass spinning that operate at high speeds. In contrast, the company’s two PyroCam products use a pulsed xenon strobe as their light source. PyroCamLP is ideal for laser processing and PyroCamMV for imaging ceramics, glass, molten metals, and continuous casting processes.
Building off of the LaserStrobe technology, the company created its SprayCam system, created as a low cost means of imaging thermal spray coating processes. SprayCam can image the powder particles in flight within a plasma stream, allowing users to monitor important qualitative characteristics, such as particle distribution, as the coating is being applied.
While quality control has been the traditional application for Control Vision’s spinoff innovations, Crawford says, “Process control is an area where we are really pushing these technologies.” Using machine vision software, the company’s systems can monitor a process and make constant adjustments to ensure consistent, high quality results.
It is in this way that Control Vision’s technologies can contribute significantly to a rapidly developing field of manufacturing: additive manufacturing—also known as 3D printing—a quickly growing $1.7 billion industry. In this case, a three-dimensional object is created by a device that “prints” successive layers of a feedstock material such as a metal or plastic, building up the object one layer at a time. NASA is exploring additive manufacturing methods, such as electron beam freeform fabrication, as a means for creating spare parts or tools in space, allowing astronauts to create what they need instead of having to carry along a supply of extras. NASA’s Innovative Advanced Concepts program has even funded research into using additive manufacturing to create entire buildings on the Moon. Control Vision has been in talks with NASA about using its SBIR-derived technology to provide process control for additive manufacturing.
“In an additive manufacturing process, we measure the melt pool diameter and perform closed loop control on, for instance, the power of the electron beam so we can maintain a constant melt pool shape in spite of a changing, dynamic process,” explains Crawford.
In the meantime, Crawford says Control Vision’s products are finding many applications in the aerospace and defense sectors, and the company has numerous projects underway with the Department of Defense. The company’s successes, Crawford says, go back to the SBIR program.
“The SBIR program continues to be very beneficial for us as we take this technology into new areas and do things we weren’t able to do in the past.”
LaserStrobe™, PyroCam™, and SprayCam™ are trademarks of Control Vision Inc.
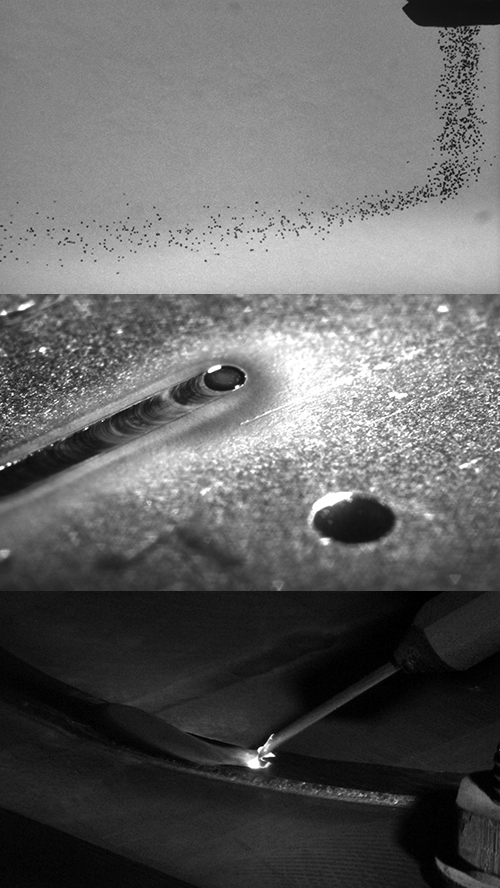
The technology has been used to reveal details of manufacturing techniques, including (top to bottom) thermal spray, laser welding, and additive.
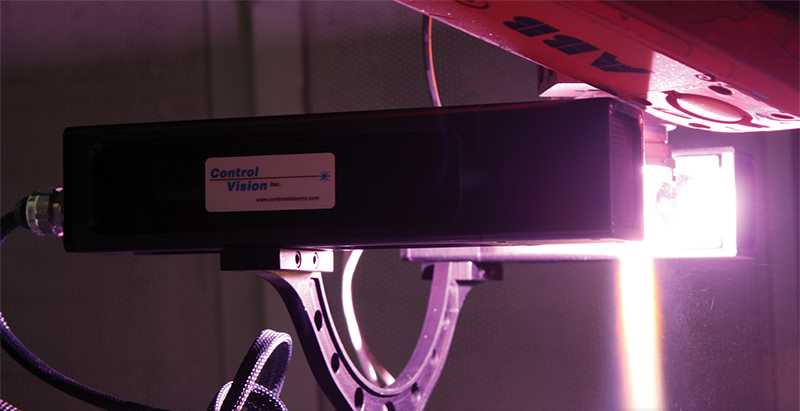
Control Vision’s spinoff technology uses video sensor systems to capture images of high-energy, high-brightness industrial processes.