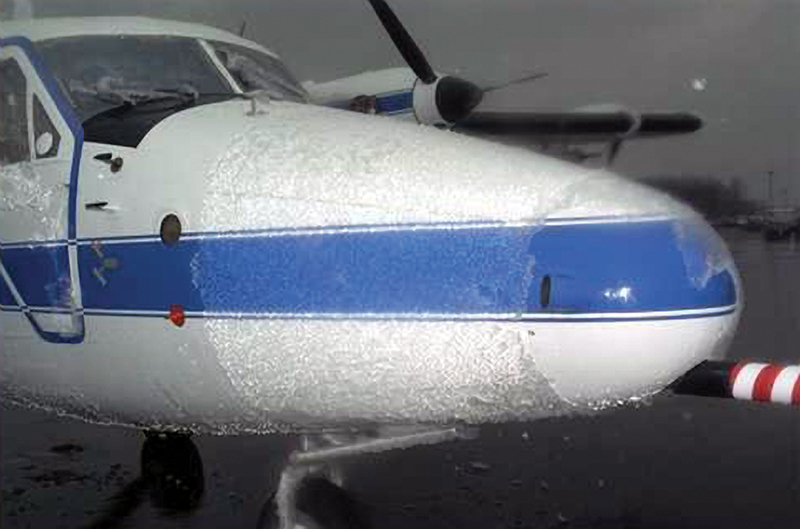
Simulation Tools Model Icing for Aircraft Design
NASA Technology
Here’s a simple science experiment to try: Place an unopened bottle of distilled water in your freezer. After 2–3 hours, if the water is pure enough, you will notice that it has not frozen. Carefully pour the water into a bowl with a piece of ice in it. When it strikes the ice, the water will instantly freeze.
One of the most basic and commonly known scientific facts is that water freezes at around 32 °F. But this is not always the case. Water lacking any impurities for ice crystals to form around can be supercooled to even lower temperatures without freezing. High in the atmosphere, water droplets can achieve this delicate, supercooled state. When a plane flies through clouds containing these droplets, the water can strike the airframe and, like the supercooled water hitting the ice in the experiment above, freeze instantly. The ice buildup alters the aerodynamics of the plane—reducing lift and increasing drag—affecting its performance and presenting a safety issue if the plane can no longer fly effectively. In certain circumstances, ice can form inside aircraft engines, another potential hazard.
NASA has long studied ways of detecting and countering atmospheric icing conditions as part of the Agency’s efforts to enhance aviation safety. To do this, the Icing Branch at Glenn Research Center utilizes a number of world-class tools, including the Center’s Icing Research Tunnel and the NASA 607 icing research aircraft, a “flying laboratory” for studying icing conditions. The branch has also developed a suite of software programs to help aircraft and icing protection system designers understand the behavior of ice accumulation on various surfaces and in various conditions.
One of these innovations is the LEWICE ice accretion simulation software. Initially developed in the 1980s (when Glenn was known as Lewis Research Center), LEWICE has become one of the most widely used tools in icing research and aircraft design and certification. LEWICE has been transformed over the years from strictly a research tool to one used routinely by industry and other government agencies. Glenn contractor William Wright has been the architect of this development, supported by a team of researchers investigating icing physics, creating validation data, and ensuring development according to standard software engineering practices. The program provides a virtual simulation environment for determining where water droplets strike an airfoil in flight, what kind of ice would result, and what shape that ice would take. Users can enter geometries for specific, two-dimensional cross sections of an airfoil or other airframe surface and then apply a range of inputs—different droplet sizes, temperatures, airspeeds, and more—to model how ice would build up on the surface in various conditions. The program’s versatility, ease of use, and speed—LEWICE can run through complex icing simulations in only a few minutes—have contributed to it becoming a popular resource in the aviation industry.
“LEWICE is considered the premier code in the world for doing ice-shape generation,” says Mark Potapczuk, an aerospace engineer at Glenn who has coordinated the development of the LEWICE code over the years.
The software is available to U.S. users at no cost from Glenn, and is distributed to everyone from graduate students at universities to multimillion-dollar companies. One such user has capitalized on the capabilities of LEWICE, developing a toolset with the potential to enhance the utility of the NASA-developed software.
Partnership
“I execute literally thousands of runs of LEWICE every year,” says David Parkins, founder and president of American Kestrel Company LLC. Based in Ithaca, New York, American Kestrel provides research and development and consulting services to aircraft manufacturers in the field of aviation safety and icing. Parkins has long used the NASA software to help his company’s customers design safe aircraft that can meet rigorous certification standards for flight in icing conditions. He saw room for improvement with the program’s user interface, however, and began developing tools to facilitate the plotting and running of the code. Parkins shared the results with Glenn, and the Center formed a partnership with American Kestrel through a Space Act Agreement, allowing the company to distribute LEWICE internationally with the company’s new interface.
Benefits
American Kestrel’s LEWICE Interface (LEWINT) combines LEWICE with an enhanced user interface, icing analysis tools, and automated plotting. Since 2007, the company has licensed its LEWINT product to 25 customers for applications including developing certified aircraft and analyzing wind turbines for icing issues.
“Within the United States, every airframer uses LEWICE from Glenn, or LEWINT from American Kestrel,” Parkins says. A key to the technology’s ubiquity, he says, is the years of icing data Glenn has accumulated using its various research tools.
“LEWICE is a unique code in that it has one of the world’s most extensive validation sets,” he says, explaining that Glenn has used its icing flight test bed and icing wind tunnel not only to help refine and develop LEWICE but to validate the code’s results. “Glenn has some of the best icing researchers in the world at one of the best icing facilities in the world working on that software, and they have evolved it into a very robust tool.”
To help design and certify an aircraft or icing protection system for flight, manufacturers need to know how ice accumulates on their particular designs. Through using LEWICE or LEWINT in conjunction with tunnel and flight tests, engineers can determine the kinds of ice shapes that form on their designs in varying conditions. How these shapes impact the aircraft’s aerodynamics helps the engineers determine any design alterations needed to ensure safe flight. Parkins estimates that using the technology in this process saves American Kestrel’s customers hundreds of thousands of dollars in costs by reducing tunnel testing and precluding expensive, late stage design changes.
“It’s a tool that helps reduce risk substantially and provides a lot of confidence that you have a design that is going to succeed,” he says.
Glenn continues to evolve LEWICE to address new areas of icing research, including large supercooled droplets and engine icing. As useful a tool as LEWICE has been, Parkins says, its importance will only continue to grow.
“The modern certification process has resulted in aircraft that are safer in icing conditions than anything we’ve ever developed,” he says. “LEWICE has been a key part of that.”
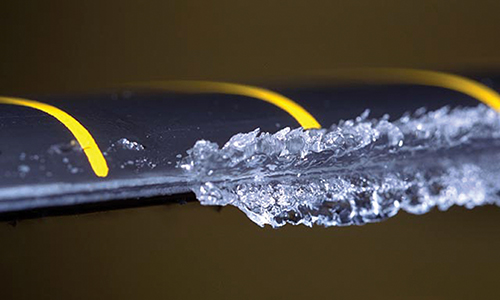
Ice buildup on airfoils can drastically affect the aerodynamics of an aircraft, leading to potentially hazardous flight conditions.
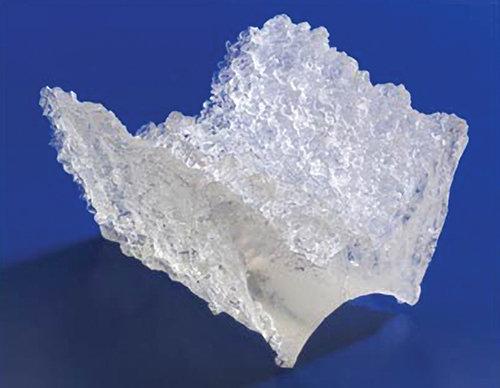
Using the NASA LEWICE software, aircraft manufacturers can model the ice accretion and the various shapes the ice can form on aircraft surfaces.
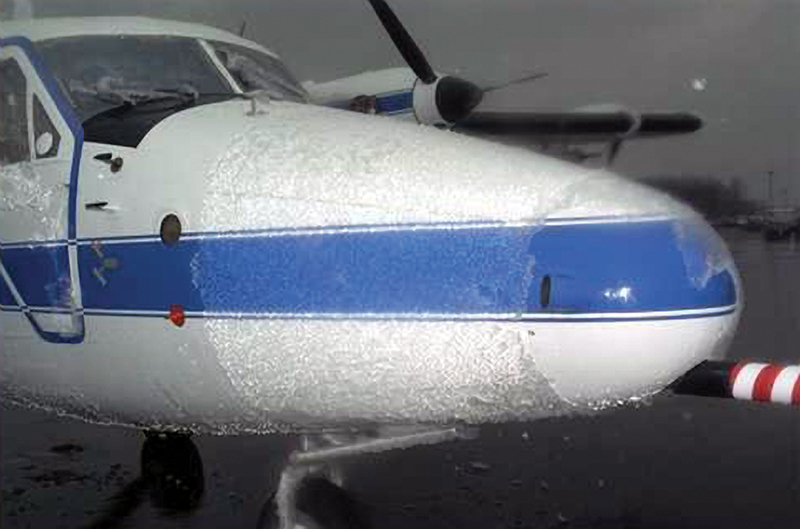
Supercooled large droplet conditions caused the buildup of ice on this aircraft.