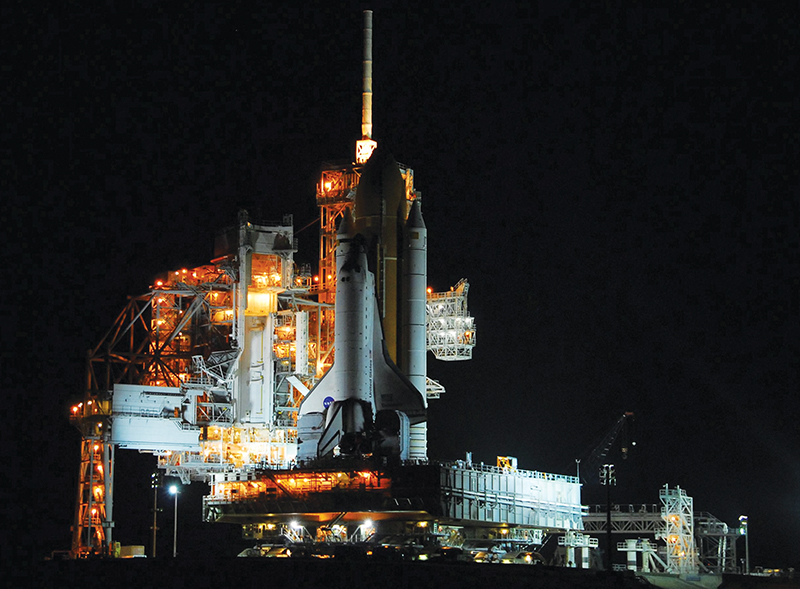
Fuel Cell Stations Automate Processes, Catalyst Testing
Originating Technology/NASA Contribution
Since the early days of space flight, fuel cells have provided an important source of power for extended missions to space. Aboard the space shuttle, three fuel cell power plants generate all of the electrical power from launch through landing.
After the Space Program refined them, fuel cells achieved widespread recognition by academia, industry, and the government as a means of producing clean energy. Compared to conventional combustion-based technologies, fuel cells produce much smaller quantities of greenhouse gasses and none of the air pollutants that create smog or cause health problems. When pure hydrogen is used as a fuel, fuel cells emit only heat and water as byproducts. In fact, the fuel cells on the space shuttle produce potable water that is pumped into storage tanks for the crew to use in orbit.
At the center of NASA’s fuel cell research and development, Glenn Research Center performs work that could lead to new flight capabilities, electric power for long-term human exploration beyond Earth orbit, more efficient cars and trucks, and a cleaner environment. Glenn continues to look for ways to improve fuel cells—including the equipment used to test fuel cell technology.
Partnership
In 1991, Glenn awarded a Phase II Small Business Innovation Research (SBIR) award to Lynntech Inc., of College Station, Texas. Working with Glenn, Lynntech addressed one of the major limitations of fuel cell testing equipment by developing equipment and techniques to fully automate the fuel cell testing process. Five years later, the company was issued a patent on the breakthrough technology and began to offer the test equipment to the commercial world.
By 1999, the equipment was being sold internationally, and as demand grew, Lynntech Industries was formed in 2001 to concentrate on the manufacturing, sales, marketing, and servicing of the equipment, which was separate from the technology development efforts of the company. Not only did Lynntech’s customer base grow, but the company’s product line grew in the fuel cell and catalyst support industry—and extended to all fuel cell types, all power levels, and all stages in the development and testing cycle, from concept through production testing.
By 2004, Lynntech made the decision to transfer its successful fuel cell technology, patents, and personnel to a spinoff company called Fideris. Shortly after Fideris introduced highly modular, plug-and-play, rack-mounted components into its product line, ownership of the Fideris technology and brand was transferred to TesSol Inc., of Battle Ground, Washington. TesSol, which stands for Testing Solutions, is a provider of the Fideris brand testing equipment to fuel cell researchers and developers, catalyst companies, and research centers around the world.
Product Outcome
Building on the invention made under NASA’s SBIR program, the Fideris product line continues to offer computer-controlled, fully automated fuel cell test equipment with ultra-low impedance electronic loads, real-time evaporation humidifiers, a graphical user interface, and all-digital communication with remote monitoring and control. Whether for a fuel cell, catalyst, battery, or process control; in a laboratory, or in a manufacturing environment; the technology provides automated operation and control of the process, device, or material being tested. Applied to fuel cell testing, for example, the test equipment provides automated fuel, oxidant, and temperature control while measuring and monitoring various parameters such as pressure, temperature, and power output.
Because of its versatility, the technology has also expanded into a variety of other applications, and a large percentage of the equipment is used for non-fuel cell work such as catalyst testing, environmental chamber atmosphere control, sensor testing, chemical reactors, stack and exhaust emission control technologies, gas blending and humidification, temperature control, and the automation of other physical processes.
Companies are using the Fideris equipment with NASA-derived technology in laboratories to evaluate the performance of products, as part of testing services, for quality control in production environments, and for general process control and automation. The Fideris equipment is found at universities, national laboratories, government entities, and small and large businesses around the world.
For the testing of catalysts, sensors, and stack emissions treatment technologies, the system evaluates the performance of the catalyst under various conditions as well as for its lifetime. In one application, a supplier to the auto industry uses the equipment to evaluate the underbody catalyst used for exhaust treatment in automobiles. In another, a commercial test facility uses the technology to perform catalyst evaluation as an independent testing service. The technology is also being used by suppliers to test NOx and O2 sensors, as well as to test ambient gas detectors and personal monitoring detectors.
Now a full 15 years after the original concepts were patented, the technology continues to be one of the most critical aspects of fuel cell testing. The widest application is in gas blending and humidification in laboratories, including the feeding of a humidified gas stream across the product or device to evaluate corrosion, to regulate how a sample is dried, to modify the composition of the sample, or to grow surface layers. Fideris’ equipment can also maintain the temperature of environmental chambers, evaporation processes, reactors, and dryers. In addition, it can be used for thermal management for performing automated temperature profiles of baths, and for blending liquids or gasses to perform automatic concentration sweeps for a reaction or process.
Thanks in part to the developments made possible through the NASA SBIR program, Dr. Craig Andrews, chief technology officer of TesSol, says the technology has saved money for the fuel cell industry.
“The technology opened the door to automated testing of fuel cells. As the fuel cell industry matured, it became more important to perform endurance testing as well as maintain a testing program where a specific test is repeated in the exact manner for direct comparison,” says Andrews. “Our equipment has reduced the manpower required for testing and turned away from the old ‘one-person, one test stand’ to suites of test stands that can perform tests for months or years without intervention.”
Fideris™ is a trademark of TesSol Inc.
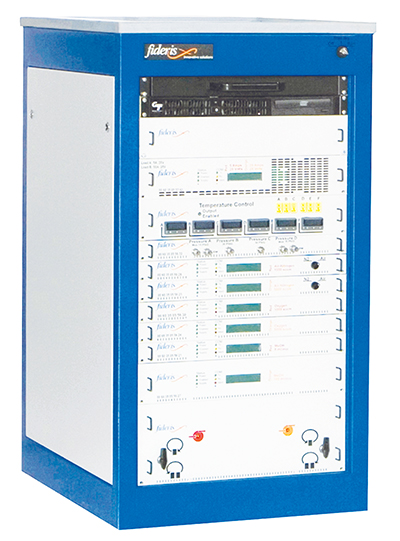
Fideris testing modules satisfy the testing needs of researchers and manufacturers in the fields of energy, fuel cells, catalysts, and sensors. The flexibility of the equipment lends itself to field reconfiguration, hardware, redundancy, and endurance testing.
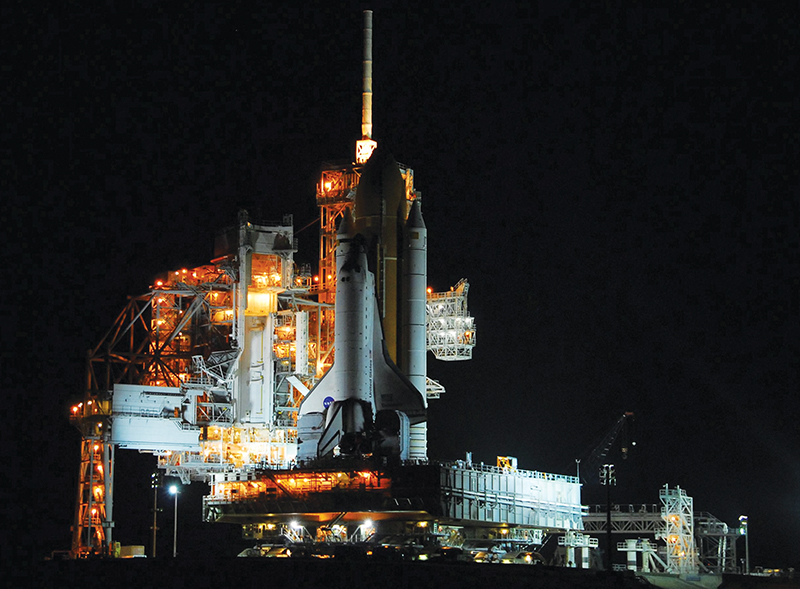
Space Shuttle Endeavour rests on a launch pad at Kennedy Space Center before the STS-118 mission. Fuels cells onboard Endeavor produce all of the electrical power needed for its mission.