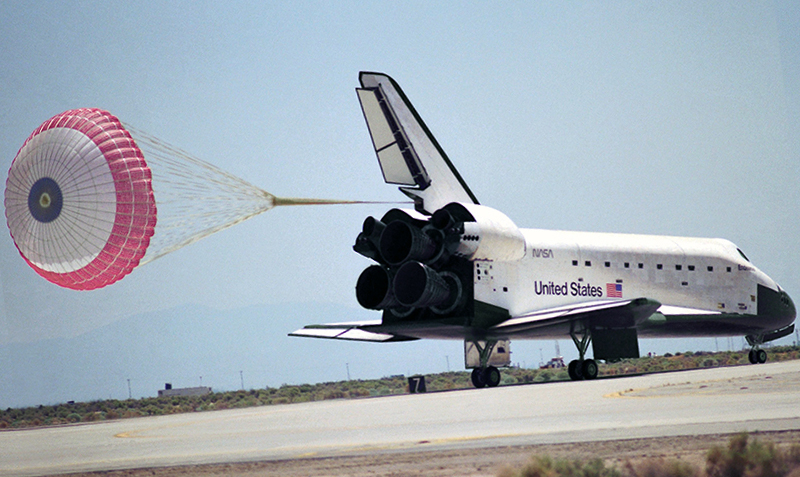
Innovative Techniques Simplify Vibration Analysis
Originating Technology/NASA Contribution
As the launch clock counts down, astronauts in the space shuttle prepare for the fastest ride of their lives. More powerful than any plane, train, or automobile, NASA space shuttles boast the world’s most sophisticated rocket engines: three 14-foot-long main engines that produce more than 375,000 pounds of thrust each. This thrust is approximately four times that of the largest commercial jet engine—and produces an extreme amount of vibration.
In the early years of development, Marshall Space Flight Center engineers encountered challenges related to the development of engine components in the space shuttle main engine (SSME). To assess the nature of these problems, the engineers evaluated the system’s components and operating environment, including the effects of vibration and oscillation. Similar to examining a patient’s heartbeat and blood pressure to inform a medical diagnosis, engineers measure vibrations to diagnose mechanical issues. At the time, vibration signal analysis was a costly, tedious, and time-consuming process. It required an expansive in-house computer system along with several dedicated personnel to keep it functioning.
“A number of significant hardware failures on the SSME necessitated the need for more sophisticated and advanced diagnostic analysis techniques to be developed,” says Jess Jones, a retired NASA engineer and a senior staff engineer at AI Signal Research, Inc. (ASRI) in Huntsville, Alabama.
Partnership
By the 1990s, the power of personal computers advanced significantly, and Marshall awarded ASRI a Small Business Innovation Research (SBIR) contract to enhance the method of vibration signal analysis. Through follow-on SBIRs with Marshall, ASRI developed PC-SIGNAL, a software package with improved tools and techniques for vibration signal analysis to assess engine ground test and flight performance. For the first time, engineers could analyze vibration and oscillation data from the convenience of a laptop or personal computer.
The new techniques allowed for quick and easy identification of potential design issues related not only to vibration, but also related to other signals resulting from sound, strain, and fluid flow. Even though the amount of sophisticated data increased, PC-SIGNAL simplified the analysis of it. According to Dr. Jen Jong, the chairman and director of research and development at ASRI, “Signal analysis had been limited to time, frequency, and phase domains, but PC-SIGNAL offered advanced signal analysis at various other domains. This information provided further insight into the engine’s operating conditions.”
One of PC-SIGNAL’s unique modules, PKP-Module, reconstructs speed signals directly from external vibration measurements, without the installation of intrusive speed sensors. This enables additional vibration analysis techniques for the SSME.
“Partnering with NASA provided a unique opportunity to work on challenging technical problems, which in turn stimulated research and development of innovative solutions to real-world problems. It allowed ASRI to participate in the advancement of state-of-the-art techniques in many critical engineering areas,” says Jong.
Today, NASA employs PC-SIGNAL on a daily basis for development and testing of propulsion systems. It is used for processing dynamic data and other diagnostic analysis, such as analyzing engine health data from shuttle missions, flow testing to identify and resolve fluctuations in pressure in turbopumps, and in designing new rockets. Most recently, the software helped to resolve a cracking issue in a valve in the Space Shuttle Endeavor’s main propulsion system.
Due to the technology’s benefits to space flight missions, the PKP-Module won Marshall Space Flight Center’s “Software of the Year” award in 2009. That same year, the PKP-Module received a Space Act Award in the exceptional category by the Inventions and Contributions Board of NASA.
Product Outcome
With its roots in software development for NASA, ASRI has grown over the last 20 years to provide diverse engineering, programmatic and technical services not only to NASA, but also to the U.S. Department of Defense (DoD) as well as commercial customers. Today, there are more than 80 users of PC-SIGNAL who are enhancing mechanical design and development efforts across the country.
Made to use on a personal computer in a Microsoft Windows-based environment, the graphical user interface of PC-SIGNAL makes it easy to use, and the automated capabilities save time when analyzing large amounts of data. It can view signal properties at various domains through two-, three-, or four-dimensional displays. As Jong explains, “All of the mathematical routines, filtering, and enhancement processes to reduce unwanted noise and other signal contamination are built into the programs. There is no additional programming necessary. Just point and click.”
The software features a number of specialized techniques for engine and machinery diagnostic evaluation including vehicle bearing, gearbox, and drive train signal analysis. Applications include dynamic signal analysis, system health monitoring, flight data analysis, flow data analysis, and fatigue analysis and monitoring. The main markets are the aircraft and helicopter industries, rocket engine manufacturers, the transportation industry, and the nuclear power industry.
DoD employs PC-SIGNAL to calculate data about vehicle and helicopter components and materials including vibration specification development and fatigue analysis and monitoring. The U.S. Army Redstone Test Center uses PC-SIGNAL for vibration data processing and for developing specifications for its weapon system test programs.
The U.S. Air Force Research Laboratory has also applied PC-SIGNAL for vibration analysis in engine testing. Aside from government use, large aerospace firms such as Pratt & Whitney and Aerojet have purchased licenses from ASRI to use PC-SIGNAL for rocket and jet engine development, as well as for testing and analyzing the fluid flow in turbopumps.
While current applications of the software are largely focused on vibration analysis, opportunities exist for wider application of dynamic signal analysis in test facilities and laboratories. In the future, ASRI plans to provide a low-cost, portable, easy-to-use, real-time version of PC-SIGNAL for dynamic signal analysis, also based on the NASA-funded technology.
PC-SIGNAL® is a registered trademark of AI Signal Research Inc.Windows® is a registered trademark of Microsoft Corporation.
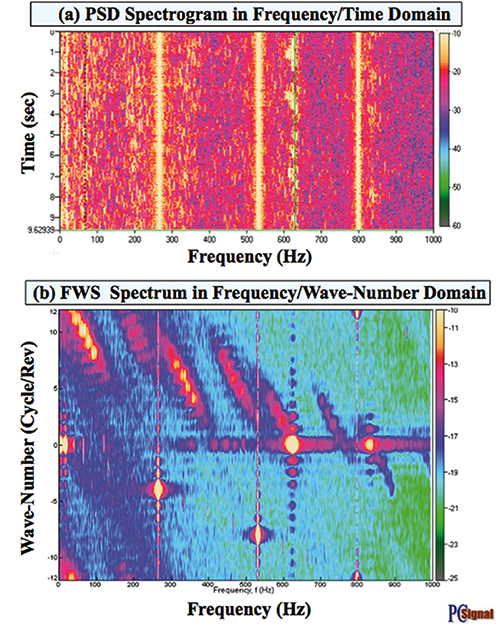
PC-SIGNAL created these dynamic displays of the signal properties in a space shuttle main engine.
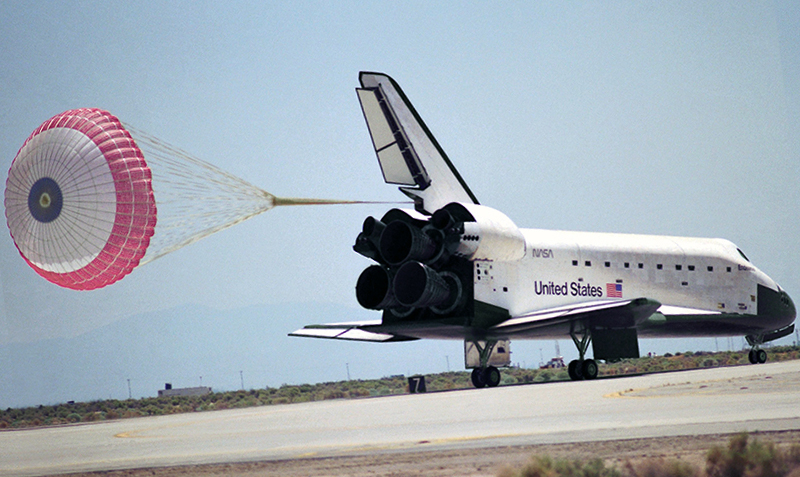
Space Shuttle Endeavour concludes a mission at Dryden Flight Research Center in 1992. The three liquid-propelled main engines, seen at the back of the vehicle, help to power the shuttle into low Earth orbit.