Inductive System Monitors Tasks
Originating Technology/NASA Contribution
The Inductive Monitoring System (IMS) software developed at Ames Research Center uses artificial intelligence and data mining techniques to build system-monitoring knowledge bases from archived or simulated sensor data. This information is then used to detect unusual or anomalous behavior that may indicate an impending system failure.
Currently helping analyze data from systems that help fly and maintain the space shuttle and the International Space Station (ISS), the IMS has also been employed by NASA’s hybrid combustion facility; an advanced rocket fuel test facility; the UH-60A RASCAL Black Hawk helicopter; and to monitor engine systems on an F/A-18 Hornet aircraft.
IMS uses techniques from the fields of model-based reasoning, machine learning, and data mining, though unlike some other machine learning techniques, IMS does not require examples of anomalous behavior, or failures, to learn. IMS automatically analyzes nominal system data to form general classes of expected system sensor values. This process enables the software to inductively learn and model nominal system behavior. The generated data classes are then used to build a monitoring knowledge base.
In real time, IMS performs monitoring functions: determining and displaying the degree of deviation from nominal performance. IMS trend analyses can detect conditions that may indicate a failure or required system maintenance.
The development of IMS was motivated by the difficulty of producing detailed diagnostic models of some system components due to complexity or unavailability of design information.
Successful applications have ranged from real-time monitoring of aircraft engine and control systems to anomaly detection in space shuttle and ISS data. IMS was used on shuttle missions STS-121, STS-115, and STS-116 to search the Wing Leading Edge Impact Detection System (WLEIDS) data for signs of possible damaging impacts during launch. It independently verified findings of the WLEIDS Mission Evaluation Room (MER) analysts and indicated additional points of interest that were subsequently investigated by the MER team.
In support of the Exploration Systems Mission Directorate, IMS is being deployed as an anomaly detection tool on ISS mission control consoles in the Johnson Space Center Mission Operations Directorate. IMS has been trained to detect faults in the ISS Control Moment Gyroscope (CMG) systems. In laboratory tests, it has already detected several minor anomalies in real-time CMG data. When tested on archived data, IMS was able to detect precursors of the CMG1 failure nearly 15 hours in advance of the actual failure event.
In the Aeronautics Research Mission Directorate, IMS successfully performed real-time engine health analysis. IMS was able to detect simulated failures and actual engine anomalies in an F/A-18 aircraft during the course of 25 test flights. IMS is also being used in collaboration with the Federal Aviation Administration’s Aviation Safety Information Analysis and Sharing (ASIAS) system to analyze commercial airline data for anomalies that may indicate potential safety hazards.
Partnership
IMS can be used to monitor nearly any system with recurring behavior and appropriate data collection. This allows application to any number of system monitoring tasks.
iSagacity Inc., based out of Portland, Maine, executed a non-exclusive license with Ames for use of the IMS software. iSagacity was founded in 2001 as a provider of engineering software and consulting services to the process industries has a Web-based platform called Remote Manager, used for collecting data in real time, monitoring, and analyzing data for industrial process systems. Customer applications for the Remote Manager include water treatment plants, water heating and cooling in the process industry, oil refineries, public water distribution, and power generation plants.
In June 2006, iSagacity licensed IMS to complement the capabilities of its Remote Manager tool for monitoring industrial process systems.
The license is helping iSagacity to build early warning and diagnostics software systems for a variety of applications and industries. iSagacity CEO, Peter Millett, reports that the partnership with NASA has allowed the company to secure early stage development funding to develop and test its product.
Product Outcome
iSagacity has developed a new product, Process Data Miner, that uses IMS for a powerful new way of detecting trends in data that are early warning signs of process or equipment problems. Process Data Miner automatically scans data in real time and organizes it into a knowledge base consisting of “data signatures” or patterns that characterize operating behavior of the system. Process Data Miner automatically learns the patterns in data and organizes them for easy knowledge discovery.
iSagacity is pleased to count the NASA-developed software amongst its core technologies, and the IMS-based products will provide an elegant solution to the important problem of early warning and diagnostics for both industrial and commercial applications. Millett indicates that the use of the underlying IMS algorithms in its new product provides a very powerful way to rapidly build intelligence into equipment monitoring applications.
Other IMS applications under development include use in spacecraft and aircraft, and potential applications under consideration include telescope subsystems and uninhabited aerial vehicles.
Remote Manager™ and Process Data Miner™ are trademarks of iSagacity Inc.
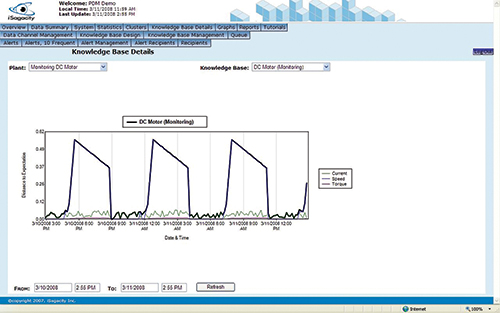
NASA partnered with industry to develop a new systems health monitoring software to increase safety and efficiency in complex industrial plants, such as power generation and water treatment facilities.
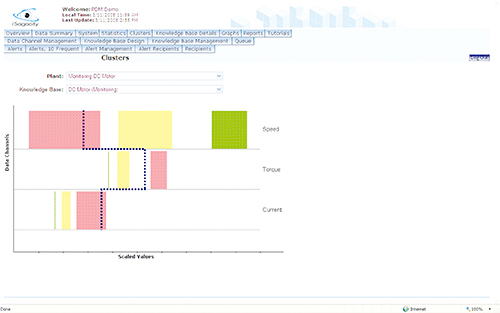
Industries that monitor the health of their equipment and processes with either online or batch sampling can benefit from the use of Process Data Miner.