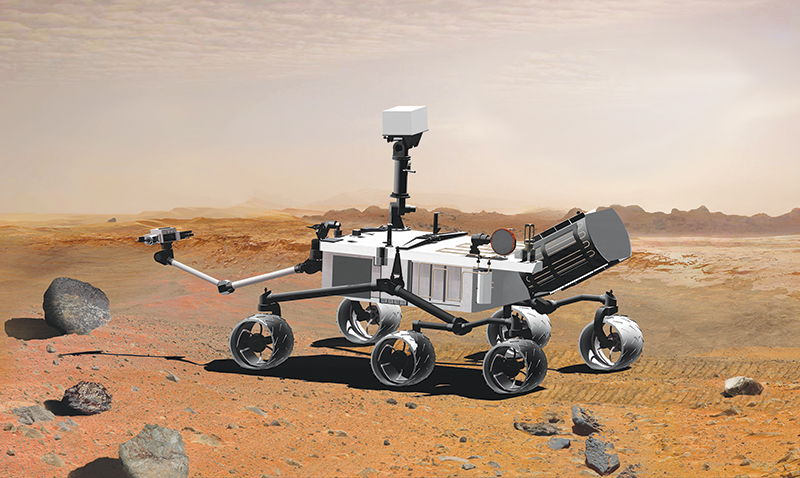
Intelligent Memory Module Overcomes Harsh Environments
Originating Technology/NASA Contribution
Solar cells, integrated circuits, and sensors are essential to manned and unmanned space flight and exploration, but such systems are highly susceptible to damage from radiation. Especially problematic, the Van Allen radiation belts encircle Earth in concentric radioactive tori at distances from about 6,300 to 38,000 km, though the inner radiation belt can dip as low as 700 km, posing a severe hazard to craft and humans leaving Earth’s atmosphere. To avoid this radiation, the International Space Station and space shuttles orbit at altitudes between 275 and 460 km, below the belts’ range, and Apollo astronauts skirted the edge of the belts to minimize exposure, passing swiftly through thinner sections of the belts and thereby avoiding significant side effects. This radiation can, however, prove detrimental to improperly protected electronics on satellites that spend the majority of their service life in the harsh environment of the belts. Compact, high-performance electronics that can withstand extreme environmental and radiation stress are thus critical to future space missions.
Increasing miniaturization of electronics addresses the need for lighter weight in launch payloads, as launch costs put weight at a premium. Likewise, improved memory technologies have reduced size, cost, mass, power demand, and system complexity, and improved high-bandwidth communication to meet the data volume needs of the next-generation high-resolution sensors. This very miniaturization, however, has exacerbated system susceptibility to radiation, as the charge of ions may meet or exceed that of circuitry, overwhelming the circuit and disrupting operation of a satellite. The Hubble Space Telescope, for example, must turn off its sensors when passing through intense radiation to maintain reliable operation.
To address the need for improved data quality, additional capacity for raw and processed data, ever-increasing resolution, and radiation tolerance, NASA spurred the development of the Radiation Tolerant Intelligent Memory Stack (RTIMS). Suitable for both geostationary orbit (GEO) and low-Earth orbit (LEO) missions, RTIMS was developed with technology investments by Langley Research Center, Goddard Space Flight Center, ASRC Aerospace Corporation, Irvine Sensors Corporation, and 3D Plus USA Inc. Advances made by the RTIMS technology include:
- Significant reductions in the size and mass of memory arrays
- Simplified interface to a large synchronous dynamic random access memory (SDRAM) array with built-in logic for timing read, write, and refresh cycles
- Novel self-scrubbing and single event functional interrupt (SEFI) detection to improve radiation tolerance
- Radiation shielding and mitigation structure at the component level instead of system level to increase system reliability
- Added mission flexibility by operating in a triple modular redundancy (TMR) or in error detection and correction (EDAC) architecture, allowing RTIMS to be configured for the harshness of the expected environment
- In-flight reconfigurability using static random access memory (SRAM)-based field programmable gate array (FPGA) technology allows RTIMS to overcome both hardware and software errors that may be detected after launch, and adapt to changing mission conditions
Partnership
3D Plus USA Inc., of McKinney, Texas, licensed RTIMS from Langley for systems and methods to detect a failure event in FPGAs. One of the contributors to RTIMS—incorporating its circuit stacking technology—3D Plus has designed and manufactured many modules (memory-based, CPU, converters) for space applications, and has had its assembly process certified by NASA and the European Space Agency (ESA). 3D Plus is a leading company in 3-D electronics packaging in Europe and is recognized as a high-performance innovator in the design and manufacturing of miniaturized 3-D modules for active, passive, opto-electronics, and micro electro-mechanical systems (MEMS) and micro opto-electro-mechanical systems (MOEMS) components.
In partnership with Langley, 3D Plus developed the first high-density and fast access time memory module tolerant of space radiation effects. The project sought to develop and demonstrate an in-flight reconfigurable radiation tolerant stacked memory array based on state-of-the-art chip stacking, radiation shielding, and radiation mitigation technologies. The module can be directly connected to a processor or equivalent and operate like a radiation tolerant static random-access memory (SRAM) with a maximum capacity of 3Gb.
The first prototype intelligent and reconfigurable radiation tolerant memory modules were manufactured and tested by 3D Plus in April 2005. To manage total ionizing dose (TID) and single event effects (SEE) on electronics, specific hardware and patented software protections were developed. The resulting unit significantly reduces board design time as it requires no single event upset (SEU) management and no TID management. The result is a complete computing module—computing cores can be compiled into the onboard FPGA that can then support a distributed, reconfigurable computing architecture. This module decreases design complexity for space-based electronics requiring memory with its simple interface and internal radiation tolerance management (shielding, EDAC, overcurrent protections, and patented software protections).
Product Outcome
3D Plus introduced the commercial Intelligent Memory Module (IMM), intended for space applications such as commercial or scientific geostationary missions and deep space scientific exploration, and high-reliability computing in other radiation-intensive environments. Nuclear facilities, for instance, utilize automated or remote-controlled nuclear waste handlers that have significant computing and data collection tasks. Nuclear-powered craft, such as aircraft carriers, submarines, and proposed future spacecraft, would also be natural applications for this technology.
By using SRAM-based FPGAs, the IMM takes advantage of the inherent ability to change function and substantial data processing performance. The IMM provides a 3Gb memory capacity, including a TMR memory controller for multiple error correction. This controller has been applied to the XQ2V1000 SRAM-based FPGA from the Xilinx Virtex-II family. The modular architecture, SRAM-based FPGA re-programmability, and the large amount of SDRAM allow the implementation of custom applications, such as image data processing, high-speed network switching/monitoring, and other embedded applications.
3D Plus is collaborating with several partners on additional developments, including two applications that will see RTIMS return to space. EADS Astrium, Europe’s leading satellite system specialist, is designing RTIMS into a satellite and evaluating it for other applications. Of particular interest, CNES (the French space agency) incorporated RTIMS into the ChemCam instrument for NASA’s Mars Science Laboratory Rover mission, to be launched in 2009 and expected to reach Mars in 2010.
Virtex® is a registered trademark of Xilinx Inc.
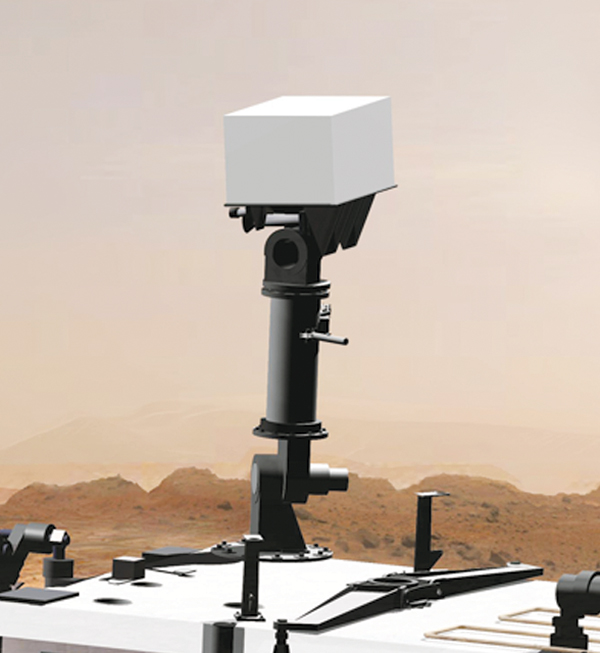
The mast of the Mars Science Laboratory robot, rising to about 2.1 meters (6.9 feet) above ground level, supports two remote-sensing instruments: the Mast Camera for stereo color viewing of surrounding terrain and material collected by the arm, and the ChemCam for analyzing the types of atoms in material that laser pulses have vaporized from rocks or soil targets up to about 9 meters (30 feet) away. The ChemCam incorporates the 3D Plus RTIMS.
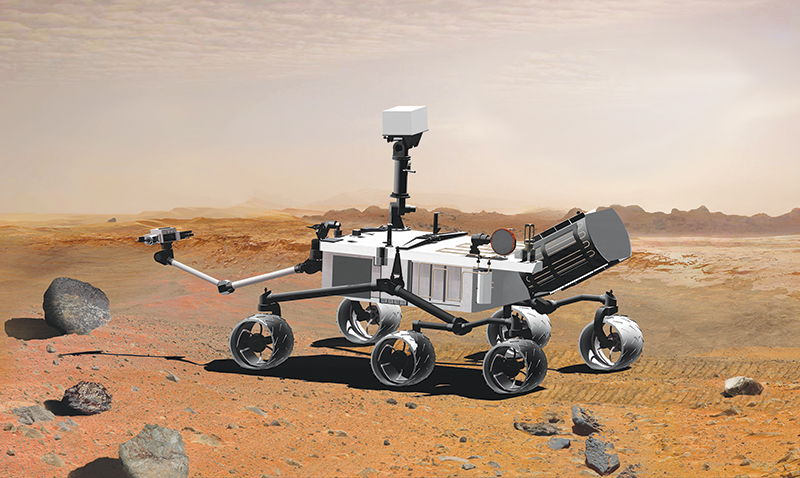
An artist’s concept portraying NASA’s Mars Science Laboratory, a mobile robot for investigating Mars’ past or present ability to sustain microbial life. This picture is what the advanced rover, scheduled for launch in 2009, would look like in Martian terrain from a side aft angle.