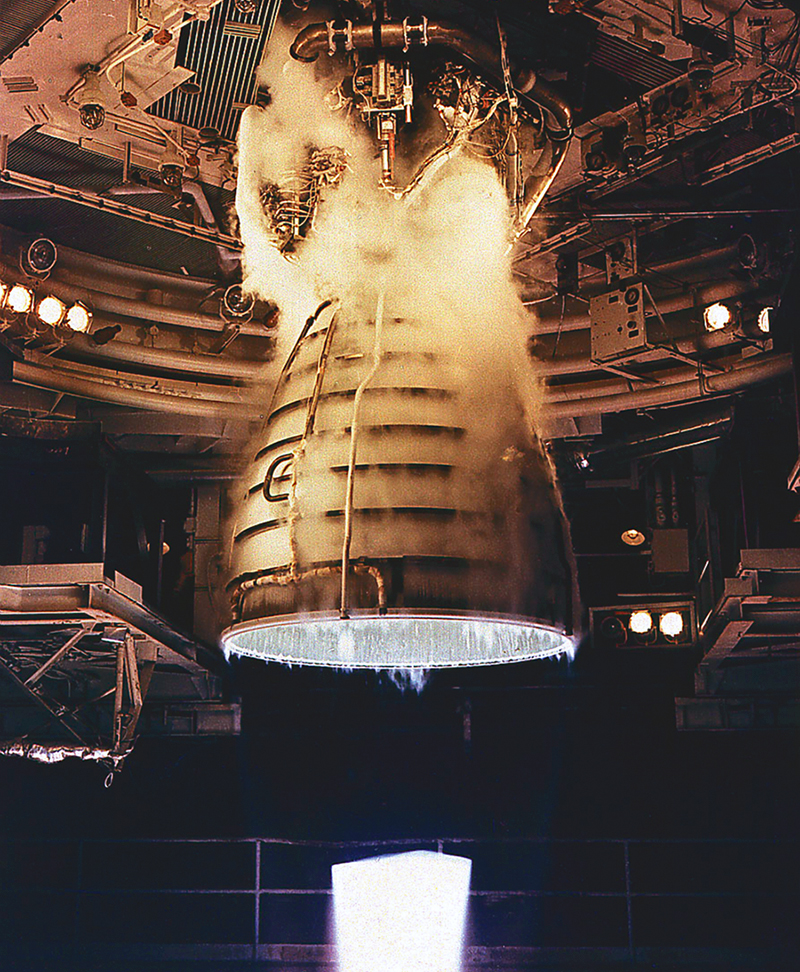
Fault-Detection Tool Has Companies ‘Mining’ Own Business
Originating Technology/NASA Contribution
A successful launching of NASA’s Space Shuttle hinges heavily on the three Space Shuttle Main Engines (SSME) that power the orbiter. These critical components must be monitored in real time, with sensors, and compared against expected behaviors that could scrub a launch or, even worse, cause in- flight hazards.
Since 1981, SSME faults have caused 23 scrubbed launches and 29 percent of total Space Shuttle downtime, according to a compilation of analysis reports. The most serious cases typically occur in the last few seconds before ignition; a launch scrub that late in the countdown usually means a period of investigation of a month or more. For example, during the launch attempt of STS-41D in 1984, an anomaly was detected in the number three engine, causing the mission to be scrubbed at T-4 seconds. This not only affected STS-41D, but forced the cancellation of another mission and caused a 2-month flight delay.
In 2002, NASA’s Kennedy Space Center, the Florida Institute of Technology, and Interface & Control Systems, Inc., worked together to attack this problem by creating a system that could automate the detection of mechanical failures in the SSMEs’ fuel control valves.
Partnership
Indialantic, Florida-based Interface & Control Systems was awarded a Kennedy Small Business Technology Transfer (STTR) contract to develop the failure-detection system. Using data-mining techniques, the company is able to extract behavioral characteristics from past performance data and automate real-time monitoring and controlling with a high degree of accuracy.
What resulted from the STTR was the combination of two cross-cutting technologies: Florida Institute of Technology developed adaptive machine learning algorithms which interact with graphical front-end tools and an artificial intelligence tool developed by Interface & Control Systems’s. This tool, known as Spacecraft Command Language (SCL) software, is a rule-based expert software system used for real-time monitoring and control. Utilizing the adaptive machine learning algorithms, Interface & Control Systems can mine historical data to define relationships and discover operational signatures for groups of related sensors.
With the SCL expert technology, the company can build data-processing control systems that run on embedded systems for autonomous applications in a wide variety of environments. These systems are capable of monitoring thousands of rapidly changing sensors and directing hundreds of actuators based on complex, machine-generated logic.
Prior to the STTR partnership, there was no evidence of cooperation between a rule-based expert system and adaptive machine learning technology within the production, launch, or flight environments of the aerospace industry, according to Interface & Control Systems. This new offering vastly improves NASA’s abilities to autonomously conduct SSME analysis in real time, while still keeping humans “in the loop”—minus the hassle of having to carry out mundane, manual tasks that can easily be handled by the failure-detection technology.
Product Outcome
Built on top of the SCL architecture, Interface & Control Systems’s SensorMiner is a time-series data-mining tool that uses past performance data to build human- readable models for real-time fault detection. SensorMiner “learns” from the past performance data, develops a “signature” for nominal operation, and automatically generates a fault-monitoring system. Conventional technology has made this process both a labor-intensive and error-prone task that is often misunderstood, even by experts, according to Interface & Control Systems. SensorMiner, on the contrary, will automatically correlate seemingly unrelated data and provide rich graphical feedback to the user.
As part of a complete toolset, SensorMiner uses a combination of time warp, cluster, rule induction, Euclidean error, and state machine technologies. The result is a sophisticated temporal machine learner for real-time anomaly detection. Using time-series anomaly detection, the toolset trains a model on known good data, estimates the probability distribution, and assigns a likelihood-based score to new sensor data. The score is used to determine if real-time data have deviated from the signature for these data points. Errors, or “out of family” characteristics, are detected by the SCL expert system and corrective measures can be automatically invoked.
“The ability to automatically make predictions or help people make decisions faster and more accurately, in real time, has far-reaching implications that spread across industry boundaries,” said Brian Buckley, vice president of marketing for Interface & Control Systems. “We designed SensorMiner to identify anomalies in a wide variety of systems.”
SensorMiner’s toolset also consists of data-mining tools and a real-time monitoring system. The data-mining tools interact with a graphical front end that allows a user to display data signatures discovered by the data-mining strategies. Once a signature is captured, additional data sets can be played through a built-in simulator to exercise the monitoring system and reveal graphical results. Using SensorMiner, data-mining algorithms can ultimately be fine-tuned to increase the likelihood of detecting anomalies in the real-time system.
Interface & Control Systems software engineer Walter Schiefele has contributed nearly 2 years of research and development to the SensorMiner product. “Many artificial intelligence programs yield models that are not understandable by humans,” according to Schiefele. “Our approach was to generate models that are easily readable and graphically displayed. People can visualize the rules. More importantly, domain experts can manually trim or adjust rules in the final product.”
The company is introducing the commercially available data-mining tool to existing control system and test set markets that require advanced, real-time anomaly detection and analysis systems. SensorMiner will then be introduced to supervisory control and data acquisition and process-control system fields. The company is also inviting inquiries for partnerships and value-added resellers, for targeted commercial markets.
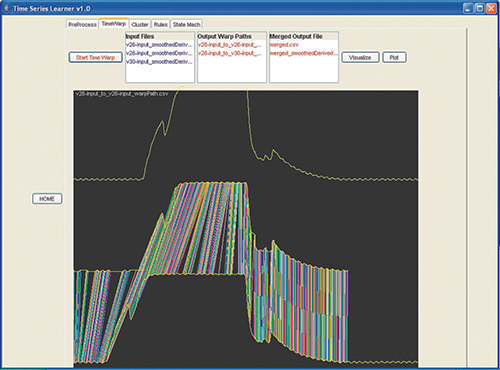
Interface & Control Systems, Inc.’s SensorMiner is a time-series data-mining tool that uses past performance data to build human-readable models for real time fault detection.
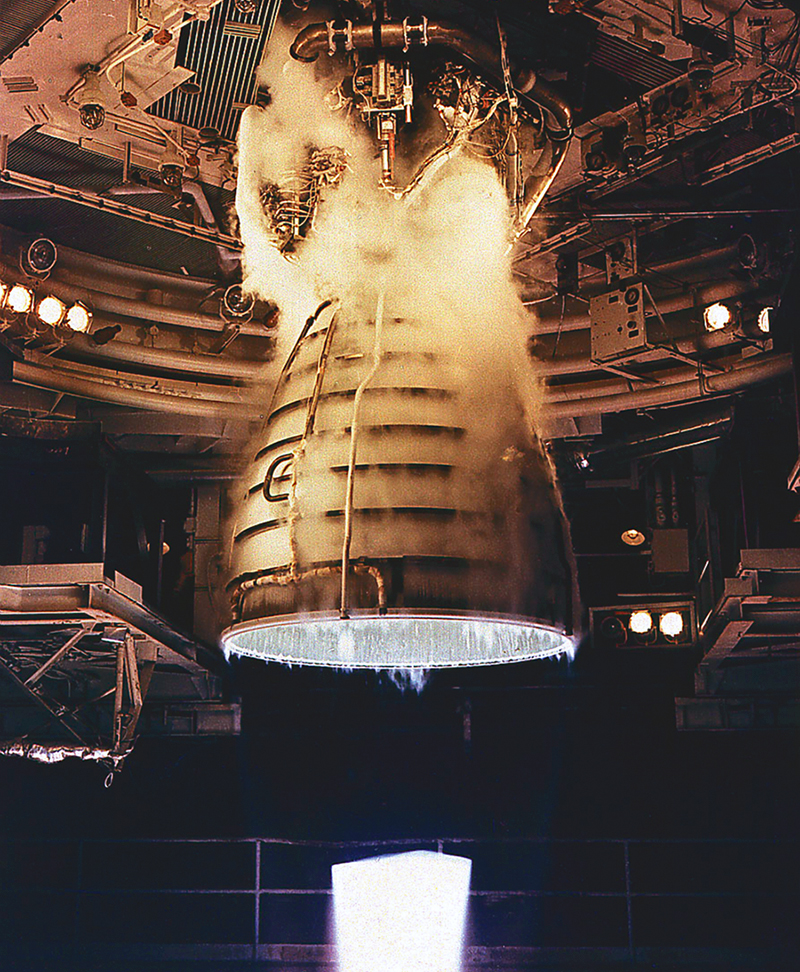
A remote camera captures a close-up view of a Space Shuttle Main Engine during a test firing at the Stennis Space Center. In addition to pre-flight testing, NASA is capable of monitoring the performance of Space Shuttle Main Engines during flight, allowing for real-time, autonomous detection of potential mechanical failures.