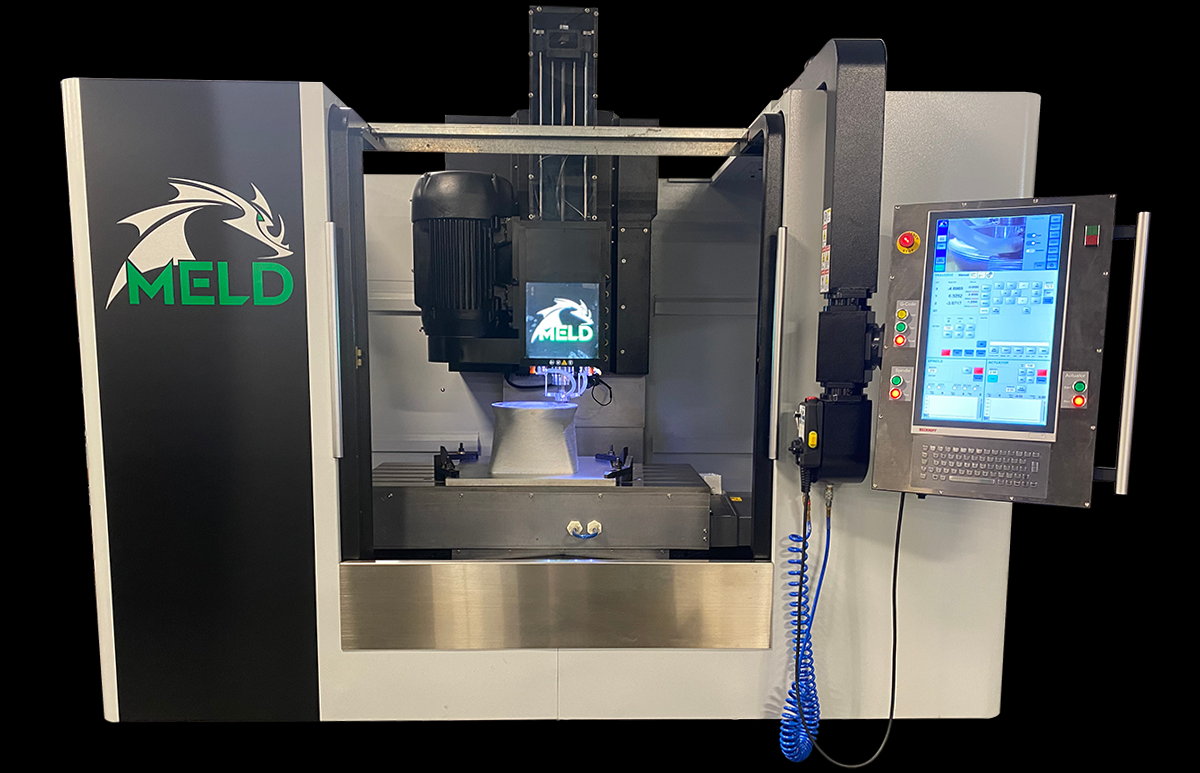
Rocket Manufacturing Meets Science Friction
Subheadline
Additive friction stir deposition builds bigger parts with more alloys
When Chase Cox and his team of engineers won NASA funding in 2014 to try a new 3D printing method by building metal parts for the Orion spacecraft, the project seemed like a long shot. The aluminum-alloy test objects, at a few cubic feet and well over 100 pounds, were outsized for any metal 3D printing process of the day, let alone one that was still in development and had never been used for aluminum.
“For what we were trying, it was at a scale that, at the time, seemed like science fiction at best,” said Cox, now vice president at MELD Manufacturing Corporation of Christiansburg, Virginia, the company that spun off from that effort. “It was a small team with a really big idea.”
Now that big idea is the basis for what is planned to be the world’s largest 3D metal printer, capable of producing entire tank hulls and other components of up to 20 by 30 by 12 feet for the U.S. Army, one of MELD’s many new customers.
The technology the team tried out under NASA funding and has since commercialized, known as additive friction stir deposition, is the only metal 3D printing technique that doesn’t melt the metal feedstock material. This gives it several advantages over the competition: It can work with metals and alloys that other 3D printers cannot. It can work in open air on a factory floor. It can build objects whose composition gradually changes from one end to another. It’s also faster than other metal printing technologies, and it can create very large objects.
MELD is now working with universities and major manufacturers around the world, and PhD students write dissertations on the technology. But when NASA awarded Cox’s team some of its first funding, “there weren’t a lot of people coming to us asking questions,” he said. “It was hard to get people to pay attention.”
Printing Up Parts
At the time, the team was part of Aeroprobe Corporation, primarily a producer of airflow-measurement and avionics instruments, and had pioneered the new additive manufacturing technology internally. The NASA funding came in the form of Phase I and II Small Business Innovation Research (SBIR) contracts from the agency’s Langley Research Center in Hampton, Virginia.
NASA was already exploring 3D printing as a way to cut weight and eliminate points of failure on rocket engines or to manufacture tools and other objects in space. But additive friction stir deposition presented the first chance to consider 3D printing rocket bodies and pressure vessels, which are usually made of aluminum alloys unsuited for additive manufacturing.
Aluminum lends itself to spacecraft and aircraft for a number of reasons. “With the right choices, we can get an aluminum alloy that’s lightweight and has got a good balance of strength and ductility and good corrosion resistance,” said Marcia Domack, who helped oversee the SBIR contracts as a senior engineer in the Advanced Materials and Processing Branch at Langley before her recent retirement. “And some of those aluminum alloys that are not weldable tend to have higher strength.”
The agency was already using a similar technology, known as friction stir welding, to join the pieces of rocket bodies. Invented in the early 1990s and improved by NASA, friction stir welding uses a rapidly rotating pin tool to generate heat by friction, softening or “plasticizing” metals to allow them to be joined without melting them. Additive friction stir deposition similarly uses a hollow spinning printhead tool to plasticize metal feedstock so it can be deposited in a thin layer. Objects are built in multiple layers.
Unlike other metal additive manufacturing methods, it doesn’t have to start with a metal powder. Since it therefore doesn’t present dust hazards or require a vacuum, it can be used in open air on a factory floor and isn’t limited by the size of a vacuum chamber.
It can be used with powders, however, to create what are known as functionally graded parts. “You can start with one material and add small amounts of another material and keep changing that ratio to create a grade in the component you’re building,” said Domack. One interest both Langley and industry have in graded materials is for building airplane bodies, which are typically made by riveting a fatigue-resistant skin onto high-strength stiffeners, she said. “One of our goals is a manufacturing process that would let you go from the skin-type material to the stiffener-type material in one piece.” This would create a stronger structure while eliminating the weight of the rivets.
The work with Langley also demonstrated that the technology could recycle titanium scraps, which could save manufacturers a lot of money. Companies that use titanium often cut and mill a block of the expensive metal down to the desired shape, generating a pile of scrap metal that gets thrown out, Domack said. Aeroprobe and Langley found they could hot-press titanium chips into a feed rod and print with it, she said. The team also proved the technology’s ability to print from feedstock made by pressing wires together.
But Domack said much of the initial work was “a lot of development of the parameters – how fast do you rotate? How hot do you have to get?”
“We demonstrated the ability to print in open air using high-strength aluminum alloys that couldn’t be printed with other methods,” said Cox. It’s the kind of work that’s now a significant part of the company’s business.
Technology MELDs with Several Industries
In 2018, MELD Manufacturing spun off to sell its printing machines and offer 3D printing services, although it remained a subsidiary of Aeroprobe. And at the start of 2023, the 3D-printing-as-a-service business spun off into another new Aeroprobe subsidiary, MELD Printworks.
Cox said most major aerospace companies have already purchased MELD machines, as have a number of universities. Several of the universities, in turn, are working with partners in automotive and other manufacturing industries to explore more widespread adoption of the technology, he said, adding that commercial airplane makers are also showing interest. Federal government customers include the military and the Department of Energy.
MELD is also licensing the technology to larger manufacturing companies so they can build their own 3D printers, Cox said.
So far, most of the interest is in applications that require low numbers of large parts, as this is where the biggest savings can be realized. “Some of these really high-cost parts have lead times of two years,” Cox said, noting that reducing that time to months with a MELD printer saves a significant amount of money.
In the two years before MELD Printworks spun off, the number of employees at MELD Manufacturing expanded from the single digits to about 40, he said. “We’ve got a team of people from all over the country, and they’re all excited at the chance to have an impact on a technology that has so much to offer.”
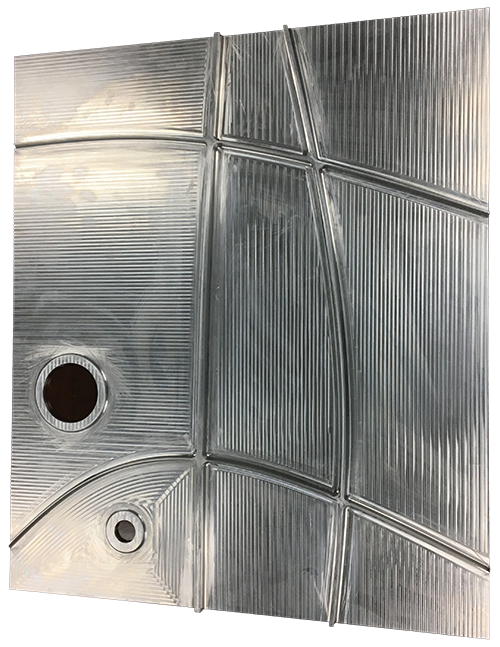
As part of Aeroprobe Corporation’s work with Langley Research Center, this panel with an array of stiffeners was created with the help of additive friction stir deposition. Airplane bodies typically wrap a fatigue-resistant “skin” material over high-strength stiffeners, but NASA is interested in combining these two elements in a single piece. Credit: NASA
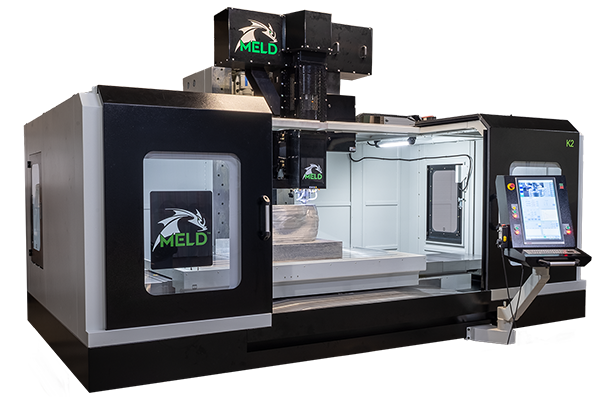
MELD’s K2 printer, intended for the production and repair of large parts, has a build space of more than 80 cubic feet. Credit: MELD Manufacturing Corporation
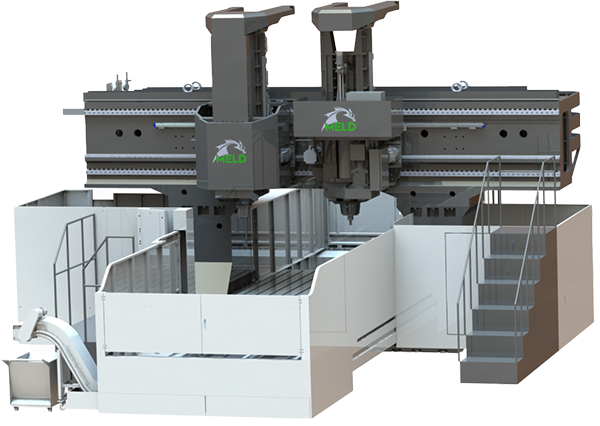
The 3PO is MELD’s largest 3D printer, incorporating both additive and subtractive manufacturing machines with an immense build space of 380 cubic feet. Credit: MELD Manufacturing Corporation
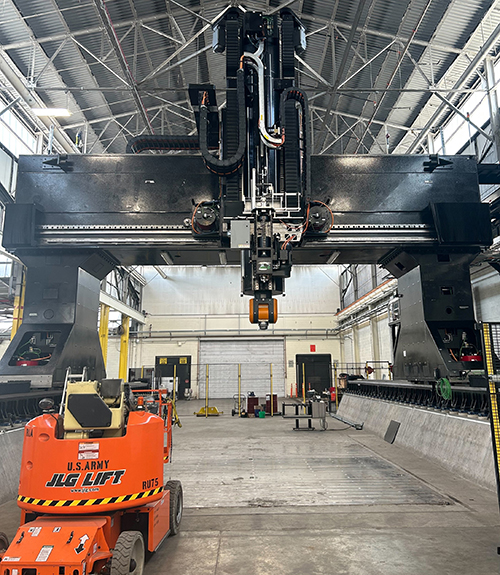
This huge 3D printer from MELD Manufacturing is being commissioned by the U.S. Army at Rock Island Arsenal in Illinois for the Army’s Jointless Hull Program, which will create single-piece hulls for combat vehicles. Credit: Rock Island Arsenal, Joint Manufacturing Technology Center
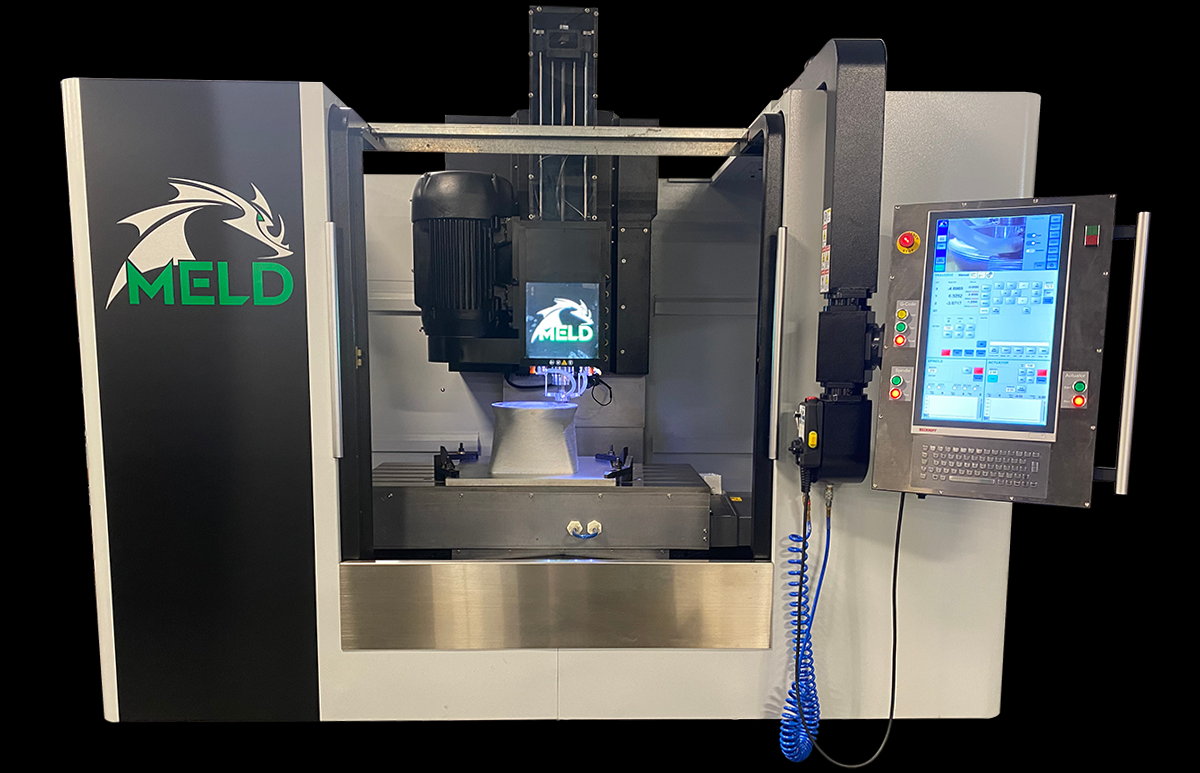
With a build volume of up to 45 by 23 by 23 inches, MELD’s smallest 3D printer, the L3, offers a large production capability relative to its small footprint. Credit: MELD Manufacturing Corporation