Ceramic Analysis
In the continuing quest for improved performance of aerospace systems, designers are exploring alternative materials that are stronger yet lighter than metals and have superior resistance to high temperatures. Among leading candidates are ceramics, which have already found service in aerospace propulsion systems in such high temperature Earth applications as diesel/turbine engine components and heat exchangers. They also offer performance benefits in products subjected to a lot of stress or wear, such as nozzles, valves, cutting tools, grinding wheels, bearings, and even artificial knee and hip joints.
Ceramic properties have improved a great deal in recent years due to advances in processing and composition, but they are inherently brittle and that leads to low strain tolerance and low fracture toughness. In addition, ceramic parts vary greatly in strength behavior; apparently identical parts can have vastly different fracture strength due to the variable severity of flaws in the materials. From the beginning of ceramics research, it was apparent that there was a need for a way of determining-in a product's design phase-the effects of stress and fatigue on a part, identifying all potential failure modes, and predicting lifetime capability. This was a challenge of first magnitude.
After more than 15 years of effort, Lewis Research Center provided a solution, a software package known as CARES/LIFE that accurately predicts the performance of brittle structures over time. The importance of this development is underlined by the multiple awards presented to the Lewis Research Center development team: a 1995 R&D 100 Award from R&D Magazine as one of the most significant technological advances of the year; a NASA Software of the Year Award; and the Federal Laboratories Consortium Award for Excellence in Technology Transfer. More than 300 organizations worldwide have used the CARES program in design of such widely diverse products as turbojet engines, valves for auto and truck engines, computer chips, cathode ray tubes and glass panels for office buildings. Some 65 companies are using the CARES/LIFE versions of the code.
Lewis Research Center began work on the program in the late 1970s to serve the ceramics development needs of NASA, the Department of Energy (DoE), other government agencies and industry. At that time, no code for predicting ceramic durability existed. John Gyekenyesi, head of Lewis' Structural Integrity Branch, was assigned to devise one. Members of the team who shared the Software of the Year Award with Gyekenyesi include Lesley A. Janosik, Noel N. Nemeth, Lynn M. Powers and Jonathan Salem.
The CARES (Ceramic Analysis and Reliability Evaluation of Structures) program they developed offers a cost effective means for simulating tests of ceramic components; it enables a designer to test a variety of configurations for probability of failure, and to adjust the structure's geometry to minimize the predicted failure or maximize durability. The newest version of the software-CARES/LIFE, released in 1995-has the added capability of lifetime prediction.
Among the examples of the code's utility,
- Solar Turbines Incorporated, San Diego, California is using CARES/LIFE in a DoE-sponsored development program that seeks significant performance gains by replacing metallic hot section parts in a gas-fired industrial turbine with ceramics; ceramics last longer, offer more resistance, reduce friction and weigh less.
- Philips Display Components Company, Ann Arbor, Michigan analyzed glass television tubes with CARES/LIFE to determine the forces placed on the outside of an evacuated tube and the possibility of tube implosion. The research analysis concluded that the possibility of tube implosion is nearly zero and that an implosion protection band reduced maximum principal stress by 15-20 percent and further reduced the probability of failure.
- The CARES software is in use at AlliedSignal Turbocharging and Truck Brake Systems, Torrance, California, where the company has developed automotive turbocharger wheels for a diesel engine, the first design and large-scale development of ceramic turbochargers in the U.S. AlliedSignal has delivered more than 1,700 units to Caterpillar Tractor Company, Peoria, Illinois for on-highway truck engines.
- Among a number of automotive engine applications, TRW Inc.'s Automotive Valve Division is using CARES software to design ceramic poppet valves and engine components for passenger cars. General Motors Corporation is similarly using CARES for automotive applications.
CARES and CARES/LIFE were developed in the public domain and thus are readily available to industrial firms. The codes are distributed through NASA's Computer Software Management and Information Center (COSMIC)® at the University of Georgia.
®COSMIC is a registered trademark of the National Aeronautics and Space Administration.
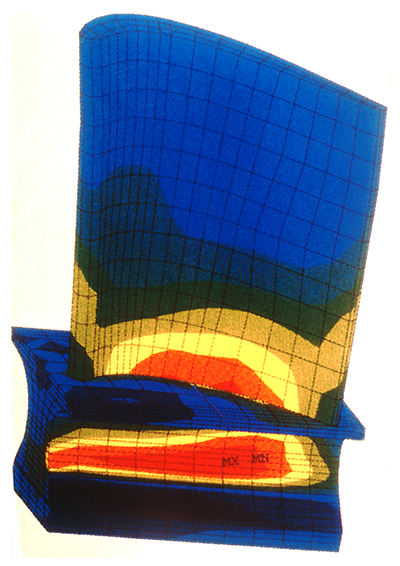
A CARES/LIFE plot shows stress levels (red/yellow highest, blue/green lowest) on a turbine blade.
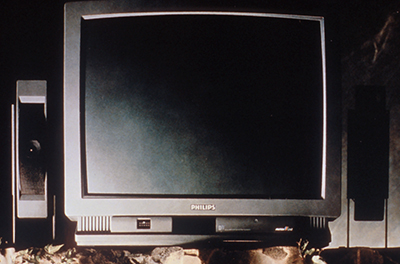
Philips Display Components Company used CARES/LIFE to analyze pressure forces on television tubes.
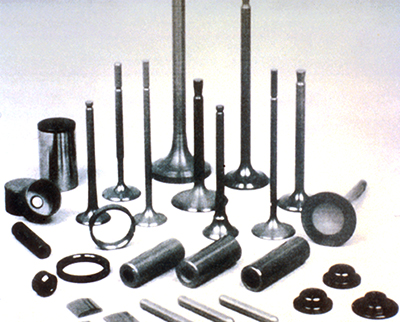
TRW Inc. used CARES to design ceramic poppet valves and engine components.
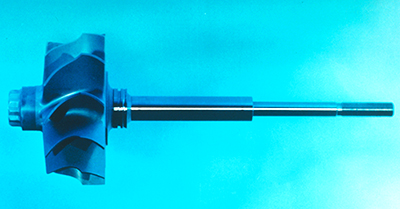
AlliedSignal's development of automotive ceramic turbocharger wheels was aided by CARES software.