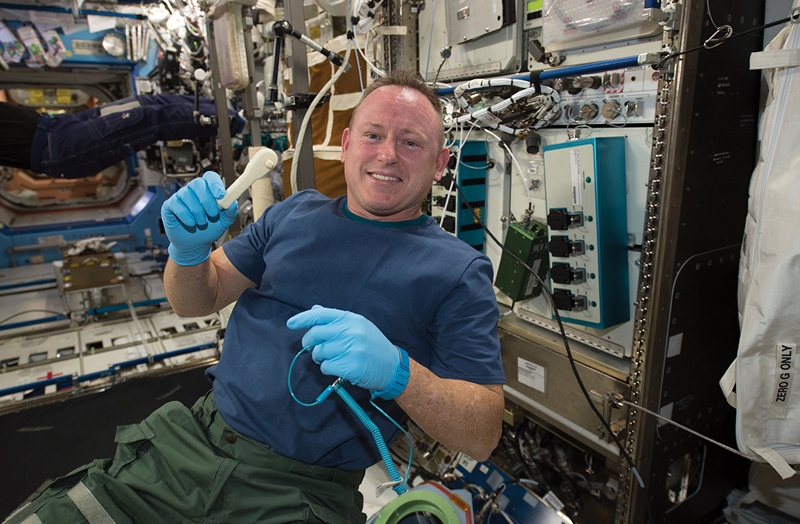
Large-Scale 3D Printer Brings Manufacturing to the Masses
NASA Technology
When the nearest Home Depot is out of reach and Amazon.com doesn’t deliver, finding spare parts or a new tool can be a challenge. That can be true whether you’re orbiting through space or in a shantytown in Kenya.
In recent years, with the spread and increased sophistication of 3D printers, NASA has been exploring a new solution: printing what it needs—so far at the International Space Station (ISS), but aiming one day to use the technology to help enable crewed missions into deep space.
The same idea appealed to a group of young innovators then working at Johnson Space Center, who hope to bring the technology to developing countries, where they believe it could alleviate some difficulties facing entrepreneurs and aid workers.
Most 3D printers extrude streams of heated plastic, metal, or other material to build objects, layer by layer. The printers follow designs created on a computer that can be shared electronically—helpful for space applications, where an engineer on Earth can create and test an object and then send the design file for printing in space.
A team including engineers from Marshall Space Flight Center and 3D printing company Made In Space built the first 3D printer ever shown to work in zero gravity. It was installed on the ISS in 2014 and successfully performed a course of 25 test prints, including a calibration coupon, a torque test, and a clip for the mini CubeSat satellites.
The most famous print in the series was the final one, a functional ratchet—the first item printed from a design sent from Earth instead of preloaded on the printer before it launched. The project, accomplished from design to successful space-print in one week, confirmed the broad potential for 3D printing for future space missions.
“If you can transmit a file to the station as quickly as you can send an email, it opens up endless possibilities for all the types of things that you can make, from CubeSat components to experiment hardware,” Niki Werkheiser, the space station 3D printer program manager at Marshall, said in an article published by NASA soon after the ratchet printed. “We even may be able to make objects that previously couldn't even be launched to space."
Technology Transfer
Samantha Snabes and Matthew Fiedler met when they were working at Johnson in 2009, but they shared another interest. Both were interested in international development work and had volunteered with the Johnson Space Center Chapter of nonprofit Engineers Without Borders. The two, along with other friends at Johnson and in their volunteer community, began musing about the similar challenges faced by astronauts out of reach of a supply chain and communities in the developing world.
The team wanted to make it possible for groups in developing countries, whether aid agencies, small businesses, or schools, to buy and use large-scale 3D printers—the company calls the printers human scale alluding to the idea that they can print full-size, functional objects as opposed to miniaturized prototypes.
“The idea was to enable someone to own their own personal factory and ultimately control their supply chain so they could print solutions locally, which we thought would have been an asset for some of our peers when we volunteered at Engineers Without Borders,” explains Snabes, who with Fiedler and four others founded re:3D Inc. in Houston to make the concept into a business.
But they couldn’t find an affordable, industrial large-scale 3D printer to incorporate into their business model. Big printers came with big price tags, around $100,000, and they weren’t built to be portable.
So Fiedler decided to build his own. The re:3D chief engineer, who traces his background to mechanical, industrial, biomedical, and biomechanical engineering, says he started building things as a kid and kept right on doing it. At NASA, he used and expanded those skills in the human research program at Johnson, in the neuroscience lab.
“We were primarily interested in mitigating the effects of microgravity for the astronaut crew,” Fiedler says, and to that end, “we not only worked with a lot of software and hardware, but we created devices and machines that would test the astronauts.
“So I would work with programming machines that would simulate motion environments for the astronauts. It translates a lot from the hardware/software side, directly into creating a machine that moves like the 3D printer,” he says.
All that experience, from his childhood tinkering days to the high-tech work he was doing at NASA, paid off. Fiedler went into his garage workshop with a blank piece of paper and some aluminum for the frame, and “from there I figured out how to put everything together to make it strong and simple, and simple to manufacture.”
Benefits
re:3D branded its printer the Gigabot. In the standard configuration, it can print items up to eight cubic feet, or 30 times larger than competing desktop models, the company says. An XL configuration can print even larger items, up to 10 cubic feet.
The Gigabot is not as sophisticated as some of the other large-scale printers available, but Fiedler estimates it delivers about 85 percent of the quality at just 10 percent of the price, with units starting at $8,550.
“The very expensive printers are expensive because that last little bit of quality is very difficult,” he says. “We didn’t try to give you that $100,000 machine, but we provide a tremendous capability that you’ve never had before for a much lower price point.”
Gigabot is also sturdy, reliable, and easy to use—a plus when you’re far away from a repair facility or can’t afford for the machine to go down, whether that’s in space or on Earth. “The best theory is to make things as simple as possible but no simpler. And that’s not an easy thing to do. I took a lot of inspiration from growing up on a farm: you can’t be breaking down on the field,” Fiedler says.
Although the original goal was to bring the printers to the developing world—and the business early on got seed money from Start-Up Chile to launch in Latin America—the founders quickly realized there was a market for their affordable, large-scale printer in the United States and other developed countries as well.
Since its start in 2013, the company has sold more than 350 units around the world, including delivering units to both Johnson and Langley Research Center—a particularly sweet accomplishment for the former NASA employees. “We’re very excited about giving them the capability as well,” Fiedler says. “I think anyone would feel good about being able to close that circle.”
But he says the bigger joy for the re:3D team is bringing manufacturing power to people and places that, unlike NASA, never could have afforded a human-scale 3D printer before. Helping push forward that objective, the company also donates a Gigabot printer to a recipient chosen through a contest for for every 100 printers sold. So far, one printer was sent to a Colombian man printing prototypes for myoelectrically controlled prosthetics, in particular arms and hands, and a second was sent to a community group in the Kibera slum in Kenya, where it is being used to teach students business skills and how to incorporate 3D printing into their projects. A third was donated to a group in Nigeria using Gigabot to promote reading in remote areas.
“The thing that I most enjoy is democratizing the capability to manufacture: offering the most capability possible for the lowest possible price. That way you can get it out to as many people as possible,” says Fiedler.
“Everyone has good ideas, but maybe they didn’t have the way to realize those ideas. Now a 3D printer can be a bridge between the imagination and the world around us, and they can use it to bring their ideas into the world.”
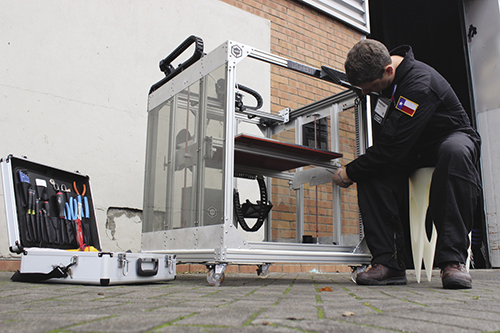
The founders of re:3D drew on experience at Johnson Space Center to design and sell a large-scale 3D printer at a low cost. Thestandard configuration prints items up to eight cubic feet, or 30 times larger than competing desktop models.
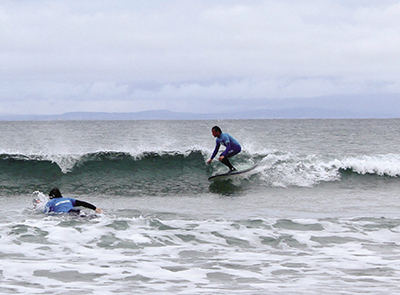
re:3D printed this surfboard in four pieces and brought it to Sligo, Ireland to surf it for an event called SurfSummit. The company says their goal is to democratize manufacturing, so as many people as possible, including in the developing world, can print their ideas in solid form.
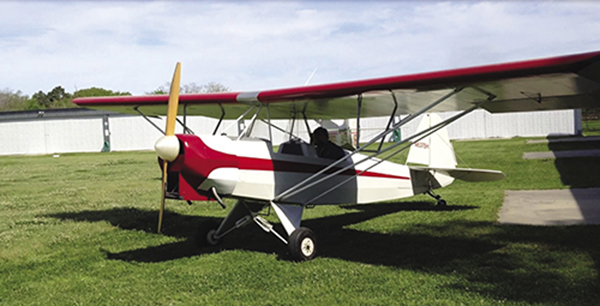
A re:3D customer printed the propeller cap for this plane—and then flew it.
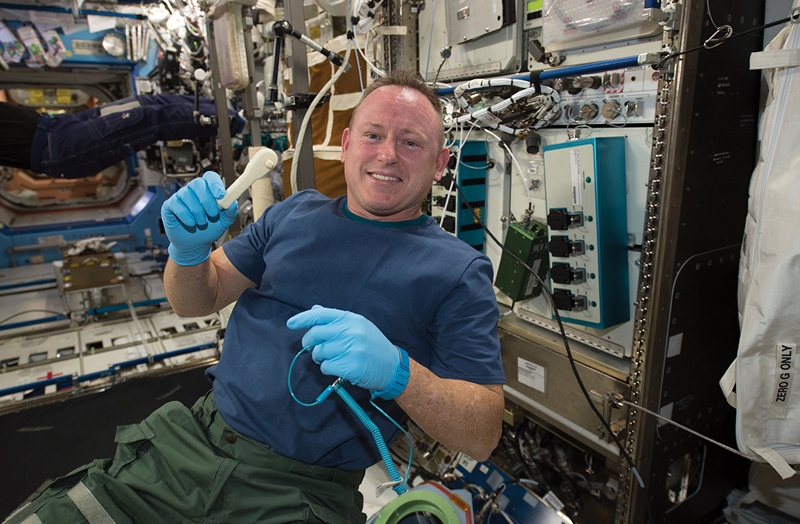
In 2014, astronauts printed a functional ratchet on the ISS from a design created on Earth and emailed into space. NASA is interested in developing 3D technology to help supply long-duration missions with items the crew didn’t, or couldn’t, bring with them.