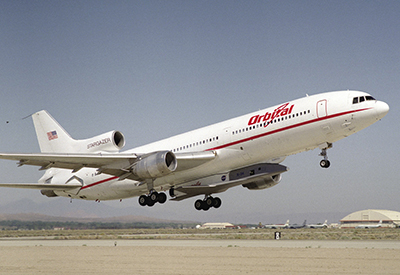
Heat-Reflecting Material Regulates Body Temperature
NASA Technology
From its beginnings, the U.S. X-Plane Program has delivered big on its objective: to advance aviation science and technology through the use of experimental aircraft. On October 14, 1947, Chuck Yeager flew into the history books as the first person to break the sound barrier when he piloted the program’s first test plane, the Bell X-1.
Fast-forward several decades, and past a multitude of other accomplishments, to the 1990s, and NASA was now looking into the feasibility of using rocket planes to reduce the cost of launching payloads into orbit. As a result, two experimental, unmanned aircraft were slated for development. Lockheed Martin’s X-33 was to be a single-stage-to-orbit, reusable launch vehicle that could reach speeds greater than Mach 13 and climb 60 miles above Earth; Orbital Sciences’ X-34 would also be a reusable launch vehicle—although it would be launched in mid-air while attached to another airplane—and capable of reaching a similar altitude.
But as with any spacecraft destined for return to Earth, their hulls would need to withstand scorching temperatures during reentry into the atmosphere, caused by intense friction with the air due to their speedy descent. NASA Ames Research Center scientists supplied the solution by inventing Protective Ceramic Coating Material (PCCM), which can be applied as a light, paper-thin coating on virtually any surface. The keys to the technology’s success are the high-emissivity, or heat-radiating agents contained in the mixture that decrease the amount of heat traveling to the underlying material. In addition, PCCM is resistant to mechanical damage and abrasion. Being that it’s water-based and doesn’t contain solvents, it’s also environmentally friendly.
Technology Transfer
Although funding for the X-33 and X-34 ended in 2001, Blacksburg, Virginia-based Emisshield (then Wessex Incorporated) had seen potential in PCCM and obtained a partial-use license for the technology from Ames in 1996, followed by an exclusive license in 2001 (Spinoff 2001, 2004, 2011). With help from the Center for Adhesion and Sealant Sciences at Virginia Polytechnic Institute and State University (Virginia Tech), the coating’s shelf life was increased, and it was optimized for metal and adapted for use with a spray gun. The technology has since been incorporated into more than 20 products. “It will work just about anywhere there is heat—from electricity to manufacturing glass and plastic bottles,” said Emisshield CEO John Olver in 2011.
Among its most popular uses is coating substrates in combustion processes such as hydrocarbon and chemical processing, resulting in energy savings, increased productivity, and less maintenance. Power generators such as biomass boilers, natural gas boilers, and steam generators reap the same benefits in addition to reduced air pollution. Furnaces that manufacture glass products also run more efficiently because of the heat savings. PCCM is even applied to commercial ovens for better heat distribution, improving the quality of baked breads.
More recently, the NASA invention has made its way into yet other markets. In 2014, Mooresville, North Carolina-based Trizar Technology licensed the PCCM innovation from Emisshield and is adapting the temperature-regulating technology for use in clothing and furniture.
Benefits
Brad Poorman, Trizar’s CEO, explains a simple truth about people’s general preferences during the hot and cold seasons. “In the summer, you want to reflect the sun away so you stay cooler, and in winter you want to absorb the heat that your body's producing and maintain it so you stay warmer longer.” He says he’s using PCCM to accomplish just that.
To understand how the technology works in hot weather, Poorman says to consider suntan lotion, which uses similar materials as PCCMs to reflect the ultraviolet (UV) light away from the skin, preventing burn. “But UVA and UVB light rays are very different from heat, so our coating, which goes on the outside of the fabric, addresses all those wavelengths by using different sizes and types of materials so that you can get a higher-UPF [Ultraviolet Protection Factor] fabric and also deflect heat, which keeps the temperature of your clothes lower.”
For cold-weather garments, the coating is applied to the inside lining, where it will deflect outgoing heat, sending it back toward the body. It’s in thermal attire that the company is making its first impact. Wyoming-based rainwear and winter adventure apparel company Cloudveil and the European Penguin brand have incorporated the technology into their clothing lines. South Korean firm Kolon Sport is also using PCCMs for its down jackets. “Both the down and our technology help you to keep your own body warmth, so there’s two types of protection at work,” Poorman says, adding that 300,000 jackets are slated for production in 2015.
For its latest venture, Trizar is also working with companies to apply the technology to patio furniture. Poorman says we’ve all experienced it: sitting on an outdoor bench or chair so hot it burns. The same goes for children’s car seats. Tests have shown that when a coat of PCCM is applied to an object’s surface, it will remain at the ambient temperature, he says. “If it’s 90 degrees out, your furniture stays at 90 degrees, versus 140 degrees if you don’t have the coating.”
No matter where the technology is headed next, a source of pride for Poorman is that the PCCM concentrate, as well as the PCCM-woven fibers and yarns the company is currently developing, is made in the United States. “Normally, in textiles a lot of the manufacturing is done in the Far East, but by making it here we can control the intellectual property,” he notes. “It pays for it to be made in the USA.”
The fact that it’s NASA technology is also paying off. “Approaching companies with a product made and used by NASA gets you so much further, faster, because of the credibility,” Poorman says. “It beats walking in the door with another technology and saying, ‘Trust me.’ They’ve heard of the Agency, and they just get it.”
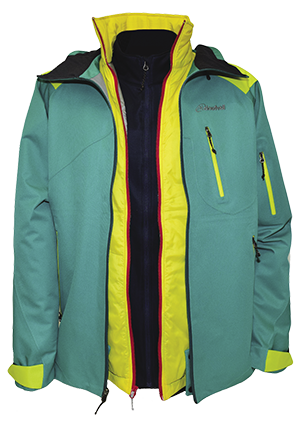
Since its development, PCCM has been incorporated into many products that require heat management. For the technology’s latest incarnation, Trizar Technology is working with clothing companies to develop apparel that keeps people comfortable in hot and cold weather. This ski jacket, made by Wyoming-based outerwear company Cloudveil, is lined with PCCM in order to retain body heat that might otherwise escape into the air.
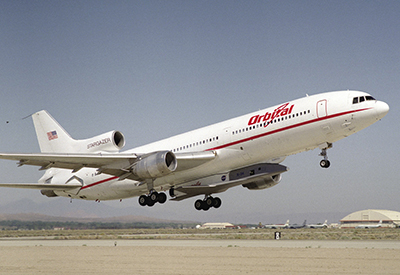
Orbital Sciences’ modified L-1011 takes off with the NASA-funded X-34 Advanced Technology Demonstrator under its belly for the first captive-carry flight on June 29, 1999. Designed to launch from mid-air, the X-34 program was initiated by the Space Agency to test low-cost, reusable launch systems for putting payloads into space. Scientists at Ames Research Center developed Protective Ceramic Coating Material, or PCCM, to protect the spacecraft from the scorching heat of reentry into Earth’s atmosphere.