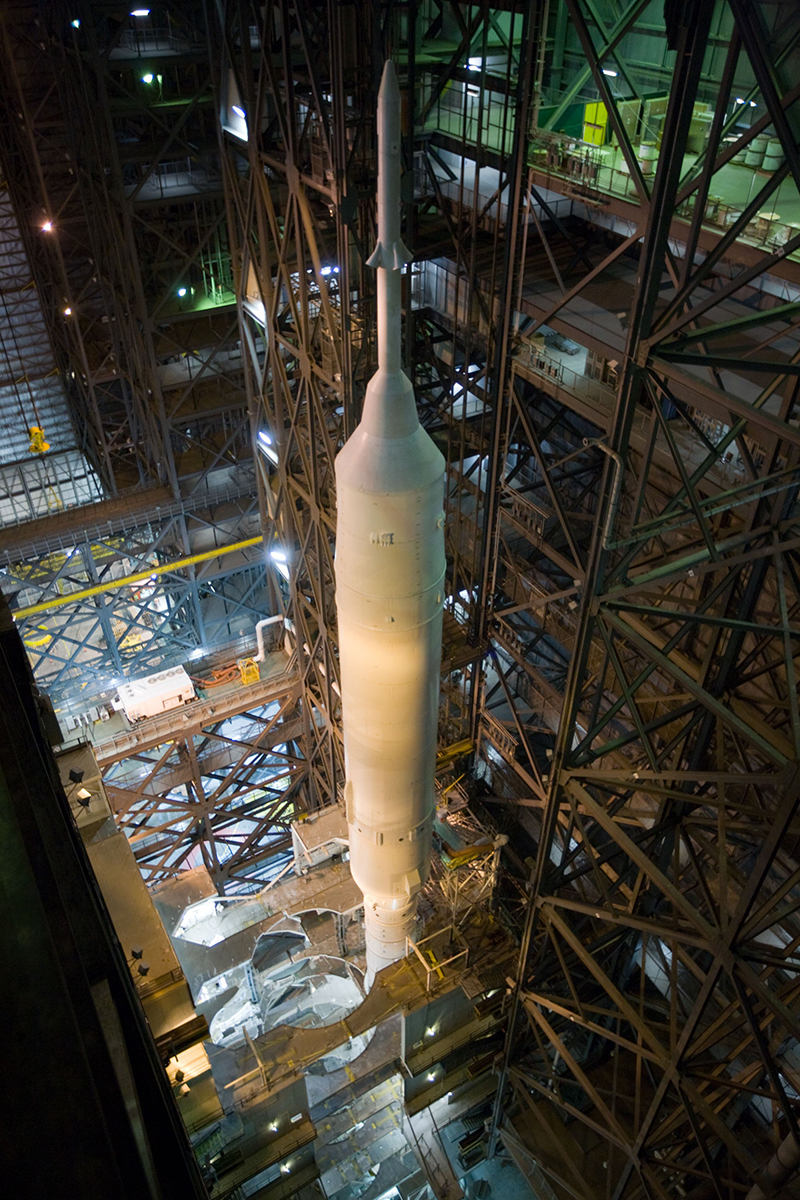
Toolsets Maintain Health of Complex Systems
Originating Technology/NASA Contribution
Monitoring the health of a machine can be just as tricky as monitoring the health of a human. Like in the human body, a variety of subsystems must work together for a machine to function properly—and a problem in one area can affect the well-being of another. For example, high blood pressure can weaken the arteries throughout the body, and weakened arteries can lead to a stroke or kidney damage. Just as a physician may prescribe medication, a special diet, or a certain exercise routine to maintain the health of a person, NASA employs a systems health management approach to ensure the successful operation of its rockets, crew vehicles, and other complex systems.
As a unique engineering discipline, systems health management prevents and minimizes problems in systems by using processes, techniques, and technology to design, analyze, build, and operate the systems. The goal is to understand a system, accurately assess its health (how well it is working), pinpoint any problems, and then support any maintenance or repair activities. Such an approach is critical to the success of NASA missions.
Partnership
To strengthen the systems health management approach used for NASA’s large, complex, and interconnected systems, Ames Research Center awarded Qualtech Systems Inc. (QSI), of Wethersfield, Connecticut, several Small Business Innovation Research (SBIR) contracts. As a result, QSI adapted its Testability, Engineering, and Maintenance System (TEAMS) toolset and then employed the technology for the detection and isolation of electromechanical problems on the International Space Station (ISS) and again for the thrust vector control subsystem and ground hydraulics for the Ares I-X test flight in 2009.
First featured in Spinoff 2001, today the toolset includes TEAMS-Designer, a program that creates a model of the system and performs a large portion of the analysis; TEAMS-RT, a software embedded in the system for real-time monitoring and diagnosis; TEAMATE, software that communicates step-by-step guidance on how to troubleshoot a problem; and TEAMS-RDS, an enterprise-level server that enables maintenance and troubleshooting from a Web-based server, as well as a collection of field failure information for further improvement of troubleshooting strategy and to enhance future designs. Together, the toolset captures knowledge about how a system fails, how the failures are detected, and then uses that knowledge to guide engineers in troubleshooting and making real-time diagnoses.
Over the past decade, QSI has received significant funding through SBIR awards with NASA and the U.S. Department of Defense, and has advanced system diagnosis and health management, two of QSI’s core capabilities. In 2002 and 2008, QSI received Space Act Awards from NASA, and in 2002, the Aviation Week award in recognition of the capabilities and advancements in TEAMS software. Now, Ames, Johnson Space Center, Kennedy Space Center, Glenn Research Center, Marshall Space Flight Center, and Jet Propulsion Laboratory all utilize TEAMS in support of NASA’s Exploration Systems Mission Directorate.
Product Outcome
QSI has also adapted TEAMS for the business and technical requirements of large-scale commercial operations. After transitioning from a provider of consulting and engineering services to a provider of software products, QSI experienced revenue growth of more than 50 percent in less than 2 years, and also expanded its presence from the United States to Japan, Israel, and China.
Originally tailored for complex research applications at NASA, TEAMS can function in much the same way for simpler applications. Whether a system propels a spacecraft or an automobile, generates power, carries data, refines chemicals, performs medical functions, or produces semiconductor wafers, the conditions that cause the equipment to fail can be modeled and analyzed, then linked to test procedures, and finally generate a troubleshooting solution.
Dr. Somnath Deb, president of QSI, explains that a failure in one subsystem can propagate to other subsystems and generate false indications. “The subsystems are usually designed by different groups of people who don’t know too much about each other’s subsystems. TEAMS connects the dots and provides a comprehensive and accurate picture of the health of the entire system.”
According to QSI data, TEAMS can substantially lower costs by decreasing warranty costs for manufacturers by 15 to 30 percent; diagnostic time across industries by 40 to 80 percent; calls to a call center by 30 to 60 percent; on-the-job training time by 30 to 60 percent; problems requiring field service by 30 to 50 percent; and repeat service calls by 70 to 90 percent.
In addition, QSI reports that one high tech company in the United States started utilizing TEAMS after comparing the time it took trained experts versus newly trained students to troubleshoot a mechanical issue. The student took 8 hours; the expert took 7.5 hours; using TEAMS, it took half an hour to troubleshoot the issue. According to QSI, field service engineers perform equally well when using TEAMS because it provides step-by-step instructions for troubleshooting.
A number of companies, including KLA-Tencor, Orbotech, Honeywell, General Motors (GM), Sikorsky, BAE, and Lockheed Martin are benefiting from using the NASA-derived technology for innovative new projects.
KLA-Tencor, a large semiconductor equipment manufacturer, is using the TEAMS tools for diagnosing and troubleshooting its suite of equipment at semiconductor fabrication sites around the world. The company expects a quick return on investment from its worldwide deployment of the TEAMS technology.
Orbotech, a supplier of inspection systems for printed circuit board production, deployed TEAMS in seven countries on three continents for its field service workforce. In this application, TEAMS averaged 75-percent accuracy on troubleshooting for new products without a maintenance history.
Under a subcontract for NASA, Honeywell selected TEAMS-RT for onboard vehicle health determination. Honeywell performed an evaluation of the competing technologies and selected TEAMS-RT for real-time diagnosis of the space flight vehicle Orion. Previously, Honeywell used TEAMS-RDS to monitor ISS data at Johnson, provide early detection and mitigation of problems, and supply continuous awareness of ISS health.
GM is also using TEAMS to evaluate how TEAMS-RDS could be used with its OnStar system, an in-vehicle security, communications, and diagnostics system. GM hopes to enable OnStar to read car engine codes and then tell the technician which part to repair. Deb explains, “This makes car maintenance more proactive because engine codes often show up before the car stalls or dies. Proactive maintenance would ensure the car drives well and the end user is not inconvenienced. Other companies are looking at TEAMS from this angle too.”
Fine-tuning its product with NASA has been extremely beneficial for QSI. “NASA wants the best, so it is open-minded and not only looks for the best, but also to bring out the best in you,” says Deb. “NASA points out what to improve and how, and the SBIRs are a great vehicle for a small business to make improvements in a technology and still obtain ownership of it. That made a huge difference in making us who we are.”
TEAMS®, TEAMS-Designer®, TEAMS-RT®, TEAMATE®, and TEAMS-RDS® are registered trademarks of Qualtech Systems Inc.
OnStar® is a registered trademark of OnStar LLC.
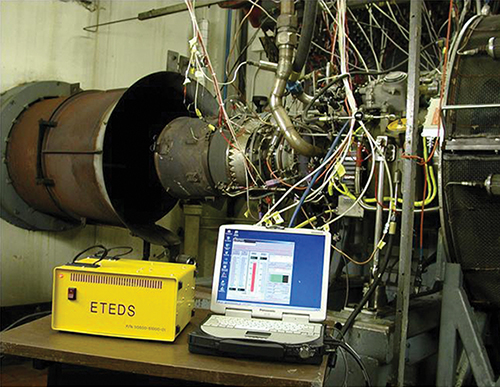
According to Qualtech Systems Inc., TEAMS software can lower service costs by decreasing problems requiring field service by 30 to 50 percent. Shown here with accompanying test equipment called the enhanced turbine engine diagnostic system, TEAMS software is used on a laptop to model the T-700 helicopter engine in a test environment.
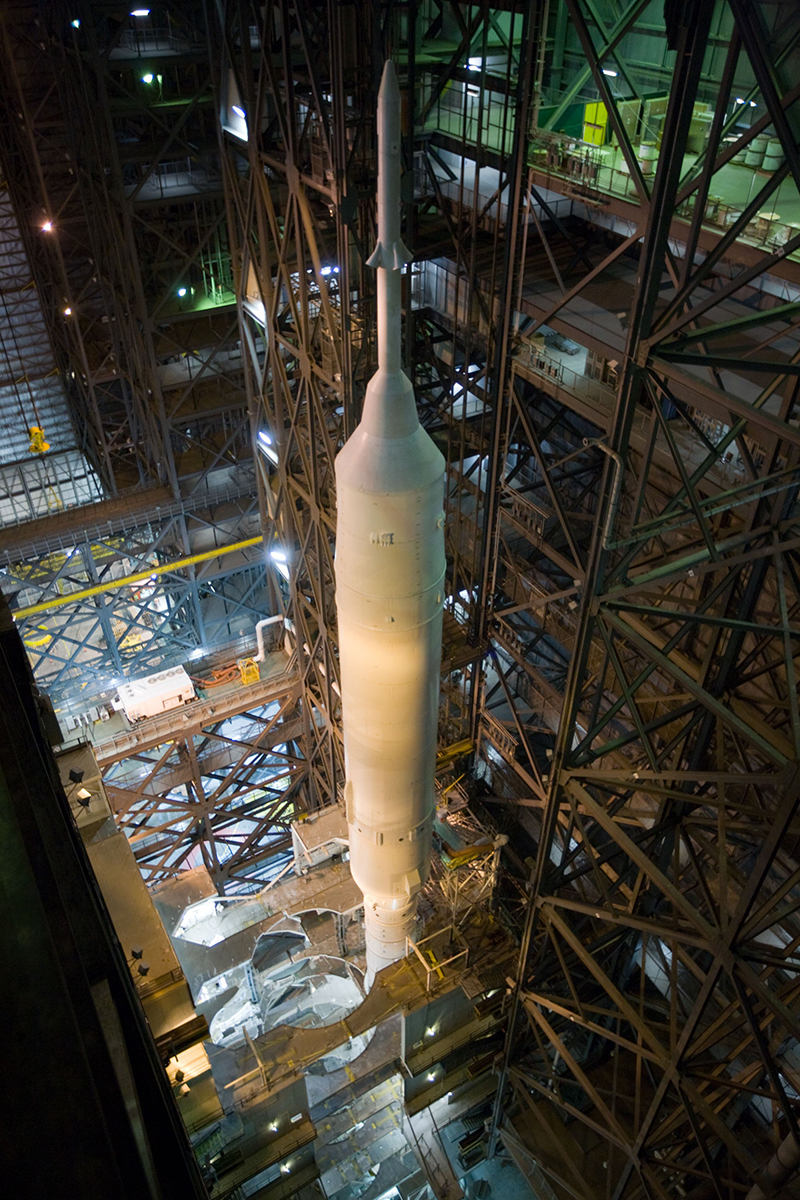
The TEAMS toolset was employed on the Ares I-X test vehicle, shown here at Kennedy Space Center’s vehicle assembly building. TEAMS is also applicable to transportation systems, medical equipment, factory systems, telecommunications, and refinery systems.