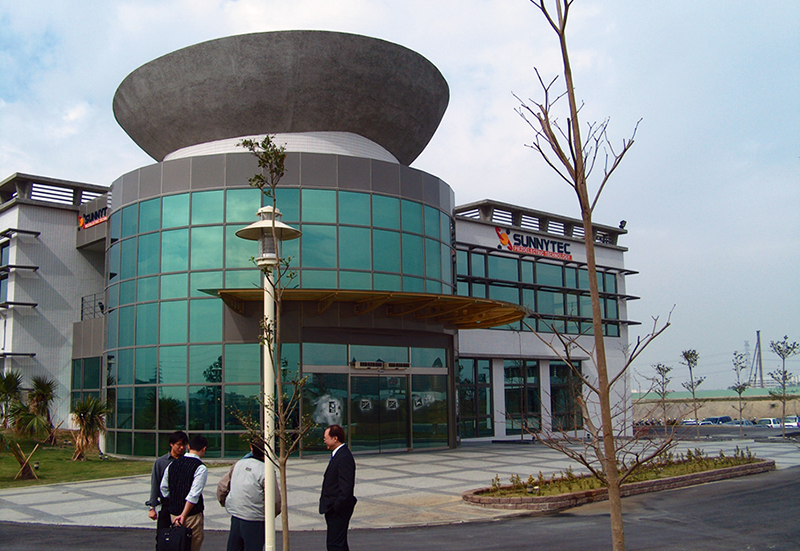
Bringing Thunder and Lightning Indoors
Originating Technology/NASA Contribution
Piezoelectric materials convert mechanical energy into electrical energy and electrical energy into mechanical energy. They generate electrical charges in response to mechanical stress and generate mechanical displacement and/or force when subjected to an electric current.
Scientists at Langley Research Center have developed a piezoelectric device that is superior in many ways to those that used to be the only ones commercially available. It is tougher, has far greater displacement and greater mechanical load capacity for a comparative voltage operation, can be easily produced at a relatively low cost, and lends itself well to mass production.
The NASA-developed piezoelectric device is also unique in that it is more efficient in extracting electrical energy from the mechanical energy that goes in. It works on a simple principle. A thin ceramic piezoelectric wafer is sandwiched between an aluminum sheet and a steel sheet and held together with LaRC-SI, an amorphous thermoplastic adhesive with special properties created by NASA at Langley. The sandwich is heated in an autoclave, and the adhesive melts. When the sandwich cools, the adhesive bonds the parts together into one piezoelectric element. While they cool, the components of the element contract at different rates, since they are made of different materials. This differential shrinkage causes the element to warp in either a convex or concave shape, depending on which way it is oriented. The shrinking of the outside metal layers places the inside piezoelectric ceramic under mechanical stress. If the element is cantilevered by clamping one side and then plucked, it reverberates like a diving board that has just ejected a diver.
This way, a small amount of mechanical energy can result in a relatively long period of electrical generation. When the piezoelectric element is used for the creation of electricity, it is called Lightning.
This same sandwiched piezoelectric wafer can also convert electrical energy into mechanical energy. Then, it is called Thunder. Electricity goes in, excites the element, and then, mechanical energy in the form of movement is generated.
Partnership
Face International Corporation, of Norfolk, Virginia, holds several licenses to the Langley piezoelectric technology, including the patent on LaRC-SI and the exclusive international marketing rights. Face is now manufacturing a commercial version in mass quantities with its manufacturing partner, Sunnytec Company Ltd., at a new plant in Taiwan.
Product Outcome
The first mass application of this piezoelectric technology is Face International’s Lightning Switch. The Lightning Switch is a wireless, batteryless, remote-controlled light switch, a way to install or replace light switches without any new wiring and without batteries. It is certified for use in the United States and Canada.
Test marketing of the Lightning Switch product started rather humbly last fall, with three mall kiosks in Hampton Roads, Virginia, and an Internet site devoted to the device.
During the test marketing, the product was also aimed at holiday shoppers who might want a remote switch for turning on and off Christmas lights. Holiday revelers who plugged the lights in behind the tree and would otherwise have to move mounds of gifts could now turn the lights on and off without having to brave the tinsel.
The Lightning Switch consists of a remote control transmitter that is modeled after a standard European light switch and a receiver that either plugs into an electrical socket or is wired into an electrical junction box. Pushing the button on the remote control generates enough electricity to send a coded radio signal to the receiver to switch on whatever is plugged or wired into the receiver.
Holiday sales at the kiosks were promising, and Internet sales also contributed to the early success, but these were essentially a marketing experiment for Face International. Serious efforts to penetrate the North American market are underway during this second half of 2005 as Face International begins offering the Lightning Switch for sale through electrical supply houses.
Although it was, in part, marketed as a device for turning on and off Christmas lights, the customers have found many additional, clever uses for the Lightning Switch. The majority of people have used it to install, replace, or rewire lighting controls without the hassle and cost of knocking holes in the walls and ceilings, or having to hire an electrician. The Lightning Switch installs in minutes and can save hundreds of dollars per switch in rewiring costs.
A popular use of the Lightning Switch is in leased or rental properties, where certain tenants may want a switch in one spot, while the next resident may want to have the switch elsewhere. With this device, both can be accommodated, and with no added expenditure by the landlord.
Other uses that customers have found for the device include a taxi-calling system for hotel bellmen; as a call-for-assistance system in assisted living facilities, nursing homes, and hospitals; a control lift for the elderly or disabled; and a signal for a casino table dealer to call for drinks or additional chips.
In addition, it has been used as a notification system for doctors to indicate to nurses when they are ready for the next patient, to trigger lights on the end of a boat dock, as a safety alert for factory floors, in foot switches for wireless tattoo guns, and to control heating, ventilating, and air-conditioning elements.
Customers have found it helpful for controlling landscape lighting, fountains, and pumps for ponds, and as a safe electrical device in wet areas, such as by pools or hot tubs. Some have even planned to employ it for grounds security, with the transmitters packaged to be put in the ground, on doors, gates, and entryways, for permanent wireless and batteryless intruder alerts.
Design-oriented entrepreneurs at retail establishments have used the Lightning Switch as a control for store fixture lighting, while art collectors have used it for backlighting framed pieces. So, while it was being marketed in malls as a Christmas light switch, consumers saw even more potential.
During this test marketing phase, Brad Face, Face International president, had even larger plans. He was in negotiations to have a manufacturing plant erected to meet the growing need for this technology in additional applications. The new plant, in Kaohsiung, Taiwan, opened in February 2005. It manufactures and assembles the Lightning Switch products as well as Lightning and Thunder piezoelectric elements. The manufacturing lines mainly consist of machinery that was designed and built for the express purpose of making these products. It gives Face International the capacity to produce 30,000 Lightning or Thunder piezoelectric elements, 30,000 Lightning transmitters, and 100,000 receivers each month. The capacity can be increased in increments of 30,000 by adding work shifts or duplicating the manufacturing line. With this capability, the company is prepared to respond to any demand.
There is a large demand developing for these products and not only in North America. Currently, Face International is in contract negotiations with housing development contractors in South Africa, where the Lightning products have the potential to save builders millions of dollars annually. Houses can be assembled quicker without electrical wiring to the switches, and at considerable savings of skilled labor and materials. The Lightning Switch can then be used to install switches in houses after construction.
Beyond the Lightning Switch, Face International has other applications of the NASA-invented piezoelectric element in development. Using the Thunder version of this piezoelectric product, Face International is working on improving hearing loss assessment technologies. Assessment of hearing loss is normally conducted by testing for minimum sound level detection. There are two forms of tests used for the basic evaluation of auditory function. The first, air-conduction testing, involves presenting precisely calibrated sounds to the ears, usually by routing the signals through headphones to the external ear canal. The second, bone-conduction testing, sends precisely calibrated vibrations through the bones of the skull to the inner ear system. Stimulation is received at the skull by placing a transducer either on the mastoid region behind the ear to be tested or through transducer placement on the forehead.
There has been a long-standing problem inherent in the construction and function of bone-conduction transducers used in auditory testing. Typically, these devices have been restricted in the usable frequency range, particularly above 4000 Hertz, and they have been limited in the amplitude with which sound can be presented to the skull. Bone-conduction transducers have relied on electromechanical components to generate the vibrations. Such transducers do not operate in a linear manner, and, as a result, individual audiometers must be calibrated to the idiosyncratic properties of the bone-conduction transducer to be used with that system. A further problem arises when the transducers are used on a daily basis. When dropped, the transducers frequently break or alter their output characteristics.
Researchers at the Hearing Center of the Hollins Communications Research Institute (HCRI), in Roanoke, Virginia, have been working on development of a new audiometric system for hearing assessment. They have partnered with Face International to create a new bone-conduction transducer that would overcome the major shortcomings of traditional transducers. The new transducers are the correct physical size, with the desired frequency range, linear operation across the relevant range, significant increases in power levels, and they come in a rugged package. The new HCRI/Face International bone-conduction transducers hold up to daily clinical use and even passed the informal stress tests of being dropped on the floor repeatedly.
Brad Face alludes to other applications, most of which are still in their infancy. But with the ability of the new manufacturing plant to create as many of the elements as he could need, and the myriad uses customers are finding for the technology, the applications are limitless.
Lightning® and Thunder® are registered trademarks of Face International Corporation.
Lightning Switch™ is a trademark of Face International Corporation.
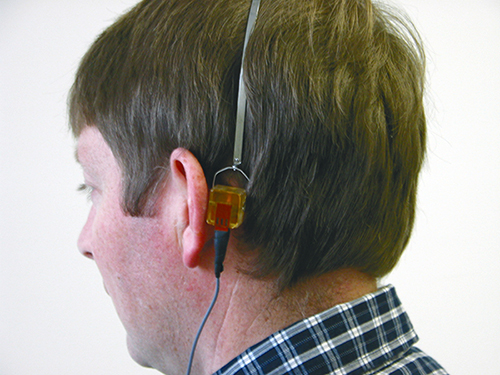
Face International Corporation has partnered with the Hearing Center of the Hollins Communications Research Institute to create durable and accurate hearing test equipment using the NASA piezoelectric technology.
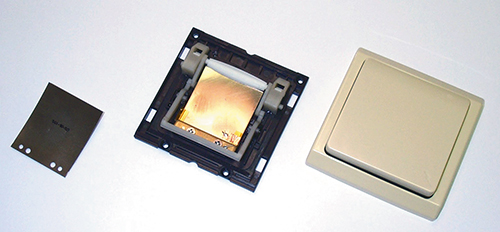
When completely assembled, the Lightning Switch looks much like a typical garage door opener.
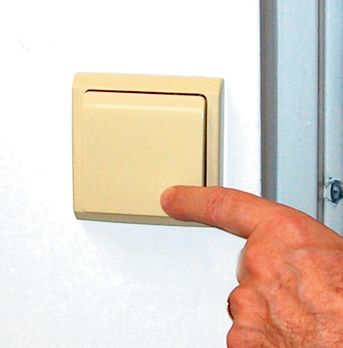
The Lightning Switch mounts anywhere and requires no wiring.
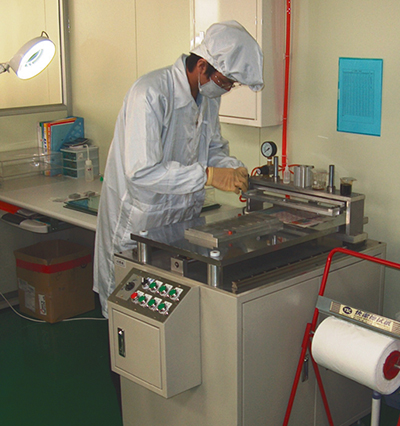
Worker in a cleanroom at the plant in Kaohsiung, Taiwan, where the piezoelectric elements are manufactured. The plant has the capability to produce tens of thousands of pieces per month.
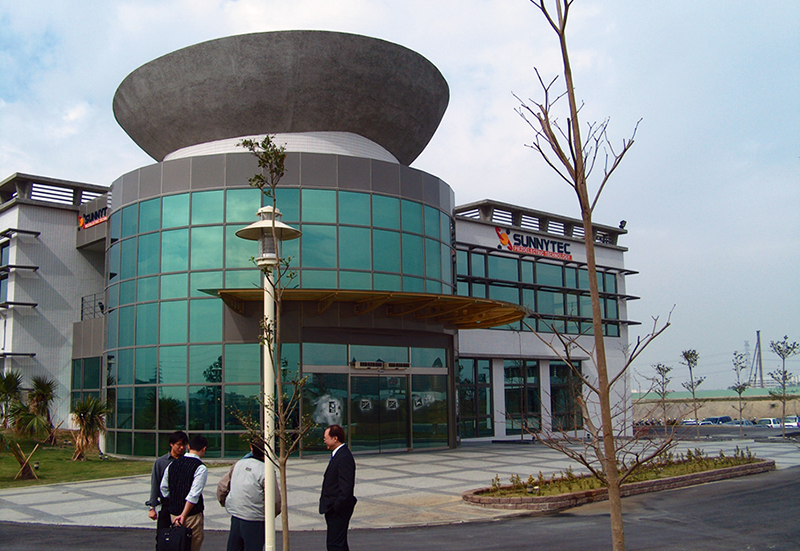
Face International Corporation has a manufacturing plant in Kaohsiung, Taiwan, where it mass produces the Thunder and Lightning piezoelectric components.